Safety aspects of housekeeping at injection molding plant
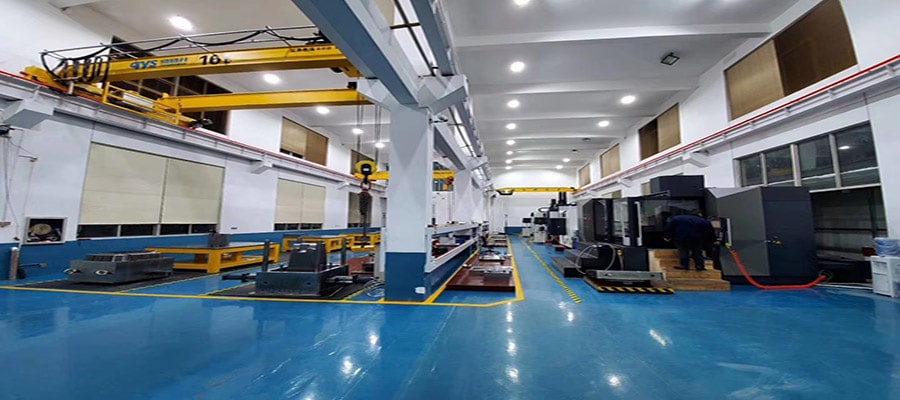
Safety aspects at injection molding plant
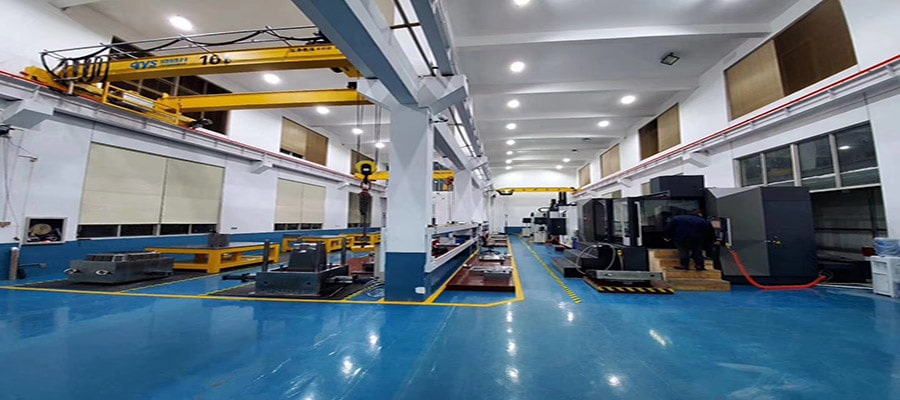
Generally, there would not be many accidents at the molding shop if all aspects of good housekeeping were strictly observed.
In the pursuit of production, good housekeeping is often neglected, sometimes with disastrous consequences.
Oil spillage
It has already been mentioned that spills of granules on the floor have occurred and leakages of oil in the mold shop. Granules, oil, and water are often combined in the mold shop.
Oil spillage on the floor for hours or even days can be almost lethal. Many contractors get the idea that rags and sawdust will absorb oil spills, but the fact is that this does not work.
The only thing you need to start a serious fire is a cigarette end or a spark.
Oil can be soaked up with proprietary materials, which render it almost non-flammable, but it is best not to spill oil in the first place.
When water leaks occur during maintenance work, it is recommended to use drip trays to avoid this kind of hazard.
If there is an unfortunate accident that results in oil spillage, it is best to clean it up, clear the floor, and then with the right detergent solution, rewash the floor.
There have been many investigations that indicate very few floors in injection molding shops are ever clean!
https://res.cloudinary.com/dl8a9jvpa/video/upload/v1574769261/Workplace_Safety_-_whiteboard_animation_health_and_safety_cartoon_tfuh4j.mp4
-
Flexible pipes and leads
There are often flexible wires and flexible water, and electrical connections that are draped across machine perimeters. This is not good housekeeping; it could easily be a safety hazard.
A forklift truck or a crane that lifts the mold can cause damage to the pipes and wires.
It might appear that there is not a lot of danger in a water leak, but there could be a severe or fatal accident in the event of a brittle electrical lead.
All flexible leads need to be clipped neatly into position before they are used and
Mold temperature controllers should be as close as possible to the machine as this will allow accurate control of these temperatures.
An additional safety hazard exists if any of these connections can be run over on the floor. Even if people just tread on these leads, it even occurs as even treading on these leads could cause trouble.
It is advisable to color-code all auxiliary connections to the machine with distinctive markings to identify them easily.
-
Machine guards
Machine guards are a thing to be concerned about, especially if there is any possibility that hot plastic could be sprayed over an operator, and it is better to have a guard made of something sturdy and transparent like a Perspex Acrylic Sheet or Polycarbonate Sheet.
Most small workshops are able to shape these materials quite easily.
Oftentimes, expanded metal guards installed on machines won't offer adequate protection when hot materials are being sprayed out.
Fluids such as hot water, hot oil, and glycol can pose a safety hazard, and regular checks should be made to ensure that flexible connections to the mold are not being abraded while opening and closing the mold.
The protective sheet of plastic already described will serve to reduce the risk of a fractured lead.
-
Disposing of purgings and hot material
One of the most important rules of good housekeeping requires that hot and purging materials should not be left on the machine because this can cause burns and unpleasant sensations, which can take a long time to heal.
Plastics retain heat for a very long time and have a very high heat capacity.
Acetal is best disposed of directly into the water, especially if they begin to decompose.
Even though formaldehyde, the product of the decomposition of acetal plastics, is toxic to humans in large doses, it is lachrymatory. It will drive the workers away from the factory much before doing any major or lasting damage.
-
Ventilation
The importance of good ventilation in housekeeping cannot be overstated. Some plastics contain additives that can lead to some toxicity, while others might contain a tiny amount of suspected material.
PVC is an example of plastic under scrutiny on the suspicion that the monomer VCM might have some biological effects.
The risk of VCM liberation during the injection molding of PVC is extremely low; however, a special apparatus for removing VCM should be used instead of the machines usually employed for the process.
Every plastic mold shop should have adequate airflow, which results from opening windows and doors and extractor fans in the ceiling above the machines.
-
Lighting
Lighting is of importance, particularly for safety reasons. Lamps, tubes, and reflectors should be cleaned regularly, and broken lamps should be replaced as soon as possible, even if they're in an inaccessible place.
That's right; obviously, when faulty switches have been identified, they should be taken out of service as fast as possible and replaced.
A considerable amount of energy can be saved by switching off unnecessary lights, but this should never be done to such an extent that it compromises safety.
Lighting standards for various types of industries are mentioned in factory legislation and must be strictly followed.
-
Safety glasses
Some operations that are associated with the fabrication of plastics must be carried out while wearing safety glasses.
On the other hand, it is important that operators working on granulating machines be provided with eye protection since the small particles that sometimes tend to escape the feed throat can harm the eyes.
-
Lifting tackle
To ensure continued safety on the job, lifting equipment, including slings, A-frames, and fork trucks, should be examined by an experienced and trained technician. All containers, as well as large plastic molds, should be clearly marked with the maximum load capacity.
A fork-lift truck can be injured if too much weight is slung from too far along the fork. Every mold should, for preference, have its own lifting eye, and no makeshift slings should be employed.
It is not recommended to sling any mold with an ordinary rope, and you should always use the proper equipment.
Whenever heavy equipment, such as molds, is being handled regularly, it is prudent for the operator to wear safety boots or shoes.
The steel toecaps in these shoes can help preserve the person's feet in the event of an accident.
-
Ladders、scaffolds、etc
Ladders and scaffolds must be sturdy and durable.
Some of the portable steps sometimes seen in molding shops are a little vulnerable to accidents when the floor collapses when anyone mounts the steps. These steps are made with castors and spring-loaded stabilizers, which contact the floor while mounting the steps.
When the weight does not actually rest on the steps, they are free to move. This is disconcerting to the operator, who has a sack of granules weighing over twenty-five kilograms on his back.
Strong wooden steps, a hand-rail, a platform, and non-skid steps, specifically designed for the machines, are much more convenient than the standard concrete steps.
On the floor, a non-skid surface should be provided for bridges over pipes on troughs.
When long ladders are used to access a specific area, they should always be secured securely, and two people should always be employed to enclose the entire area around the ladder.
-
Airlines
Airlines and filters must be periodically inspected, water traps bled clear, and filters replaced. If water is accidentally blown from airlines into electrical equipment, especially printed circuit boards, there can be a lot of damage.
The practice of blowing the dust off clothing by using an air hose is extremely dangerous and should never be permitted. Air will easily enter the body from either a hole in the clothing or a small injury caused by an air embolism.
-
Fire-fighting equipment
The fire-fighting equipment used in the molding shop should always be accessible, and all persons working in it should know that all equipment has to be kept in a safe place and that they should be able to use it correctly.
Sprinkler systems are one of the best guards against fire. They can be installed, then paid for by the insurance company within a short time.
Nevertheless, the damage caused by its operation can be considerable, and it is recommended that extra precautions be taken in the storage.
Asbestos fire blankets can be used in those cases where clothing ignites or where the fire is small and can be easily contained.
In the same breath, it is also advisable to make sure the building has strategic points, static water tanks, or fire buckets available at all times.
-
Noise
The noise in the molding shop should be prevented or reduced as much as possible since it is a huge health and safety risk.
Panels are often removed from machines during maintenance without being replaced. This makes the machine less effective in preventing dust and dirt from entering and is also louder.
Dense blockboard screens can greatly reduce noise from noisy machinery and result in a more pleasant working environment.
We suggest using strong blockboard cabinets to protect portable granulators in the molding shop. This will help reduce noise and eliminate dust. Where an operator uses a large granulator for several hours, ear muffs should be provided.
Naturally, the greatest contribution to noise reduction in the molding shop (and efficiency improvements) will be made by removing the individual power sources and installing an isolated, soundproof room for the hydraulic fluid reservoir, in which the motors will be located.
The situation used to be the same during the days of compression molding when all of the machines were connected to a central supply system, and the only noise was the soft whistling of steam from the steam trap.
-
First-aid equipment
Minor accidents will inevitably occur, and the provision of appropriate equipment for their treatment may prevent them from developing into something more serious.
First aid personnel is responsible for ensuring that the equipment is maintained at all times.
A dust-removal bottle is useful in case the operator gets dust in his or her eyes.
https://www.plasticmoulds.net/safety-aspects-of-housekeeping-at-injection-molding-plant
Comments
Post a Comment