design
Plastic Molding Part Design
What is a product "Designed for Production"?
To satisfy the requirements of designing for production, a product must be functionally sound, it must have sales appeal, and it must be competitive in price.
In order for a product to be made economically by plastic mold, it must be designed so that the most appropriate materials and processes will be utilized.
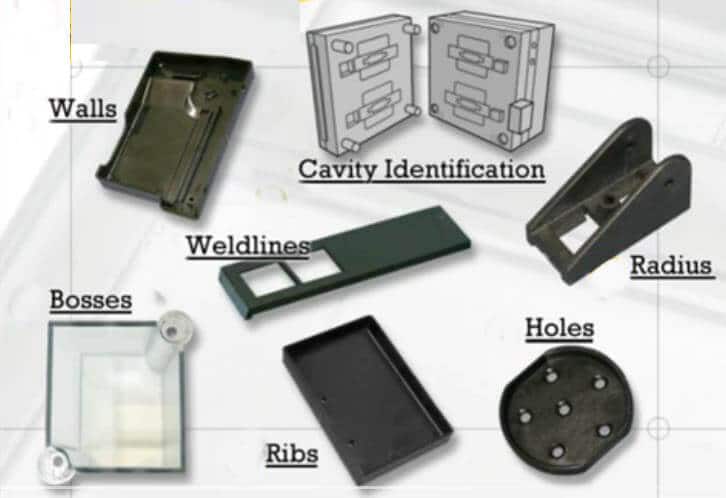
plastic part design
An engineer cannot do an effective job of product design unless he knows or is supplied with adequate information as to how his designs will be produced.
Therefore, the principal problem of engineering for production is sound functional design plus the selection of the materials and the processes to be used so that the new product can be produced on a competitive basis.
In choosing these materials and processes, the functional designer must make many modifications and changes in his original conception.
The shape, color, size, tolerance requirements, texture, weight, and functional design itself may be affected before the ideal design is developed that is functionally sound, has sales appeal, and is economical to
produce within the required time.
Plastics offer designers the opportunity to optimize their designs by studying various design parameters including material composition and product structural geometry in order to meet different product requirements.
Many structural plastics may exhibit a low modulus of elasticity, which is, in fact, one of the key defects in their design. Plastics, in general, are commonly used for applications requiring substantial static and/or dynamic loads.
In order to address the problem of shape integrity under load, low modulus structural plastics are designed shape-wise and/or thickness-wise to take advantage of their low modulus and achieve maximum stiffness.
Plastic products of this type comprise most of the plastics produced worldwide.
-
Structure Design
A reasonable and optimal molded part structure design can not only simplify plastic injection mold manufacture, reduce the cost of the mold, but also simplify its molding process to improve the good quality rate of products.
Before the design of plastic parts, a designer should learn about the function, environmental conditions, and loading conditions (including dynamic and static load), understand relations between different parts, and the effect of the assembly.
Plastic parts function should be accurate and as detailed as possible, the more comprehensive the plastic parts design is, the better the design of the plastic parts can meet the requirements.
More on Video
Tolerances:
A high degree of accuracy in molded parts is expensive to achieve.
On small tolerances as close as -0.002 in. On large pieces, tolerances of about 土0.001 to 0.002 in. per in. are obtainable.
Tolerances closer than actually mandatory should not be specified; as specified accuracy increases, cost increases disproportionately.
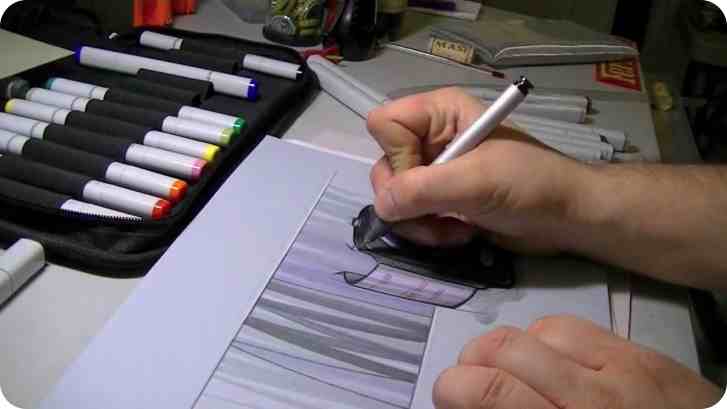
Though it is difficult to generalize about design factors for injection, compression, and transfer moldings, the following design rules should be considered:
- Use sufficient draft on long thin shapes to permit their withdrawal from the mold.
- Minimize coring. When cores are used they should be easy to withdraw.
- Avoid internal and external undercuts; they make removal of parts difficult and require considerably more expensive molds.
- Provide ample fillets on inside comers, and avoid sharp external edges and comers except at the parting line of the die.
- Avoid large flat areas. Dappling or otherwise breaking up the surface is recommended.
- Keep tolerances as liberal as possible. Excessively close tolerances add to cost because of increased die costs and a high rejection rate.
- Avoid abrupt changes in wall thickness.
- Locate parting lines so that flash can be removed easily without marring surrounding areas.
- Locate holes for easy coring.
- Use ribs to achieve desired strength and stiffness. Ribs permit materials savings by reducing section thickness.
- Use inserts for threaded holes where high stresses are anticipated or where considerable wear is to be encountered. Round inserts are preferred.
https://www.plasticmoulds.net/design
Comments
Post a Comment