Polycarbonate injection molding,Optical Lens,LED lighting, #1 China Polycarbonate (PC) injection molding
Polycarbonate injection molding
Would you like to find a manufacturer and designer specializing in poly-carbonates injection molding that is both reliable and cost-effective(as low as $ 0.5 for some cases) with their work? If you are looking for a polycarbonate molding company in China specializing in poly-carbonates injection molding, then Topworks Plastic Mold can help you.
Having been in business for more than 10 years, we have unmatched expertise in the field of design, tooling, and manufacture of injection moulded polycarbonate products of extra wall thickness at prices that are competitive internationally. Topworks also offers the highest standards of quality.
This makes us one of the only companies that can create polycarbonate molding, manufacture, and deliver polycarbonate molding parts from concept to reality through our wide range of PC injection molding services.
Our processes make every step of the poly-carbonates injection molding process simpler, whether a concept or a work-in-progress is being developed
Our poly-carbonates injection molding involves:
- Automobile parts
- Medical instruments
- Aerospace
- Packaging field
- Electronic appliance
- optical lens
- LED lighting
The maximum wall thickness of the PC product can reach 3 cm, but the surface does not shrink, and there are no bubbles inside.
https://www.youtube.com/watch?v=ms2aPfCHdzc&feature=youtu.be
- EXTRA WALL THICKNESS POLY-CARBONATE INJECTION MOLDING CASE
#1 CASE
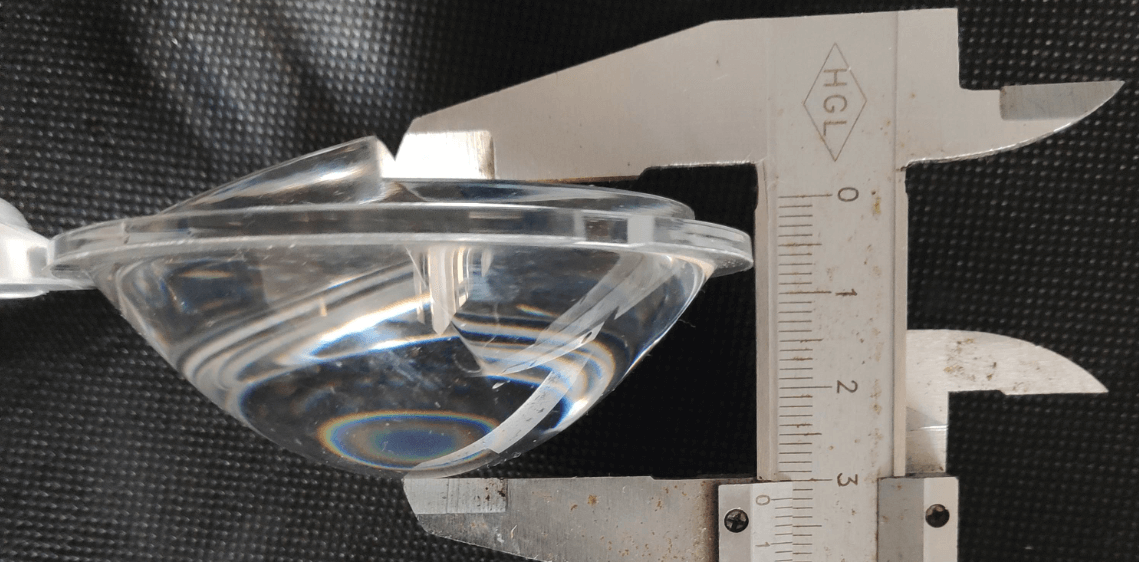
extra wall thickness 32 mm poly-carbonate injection molding
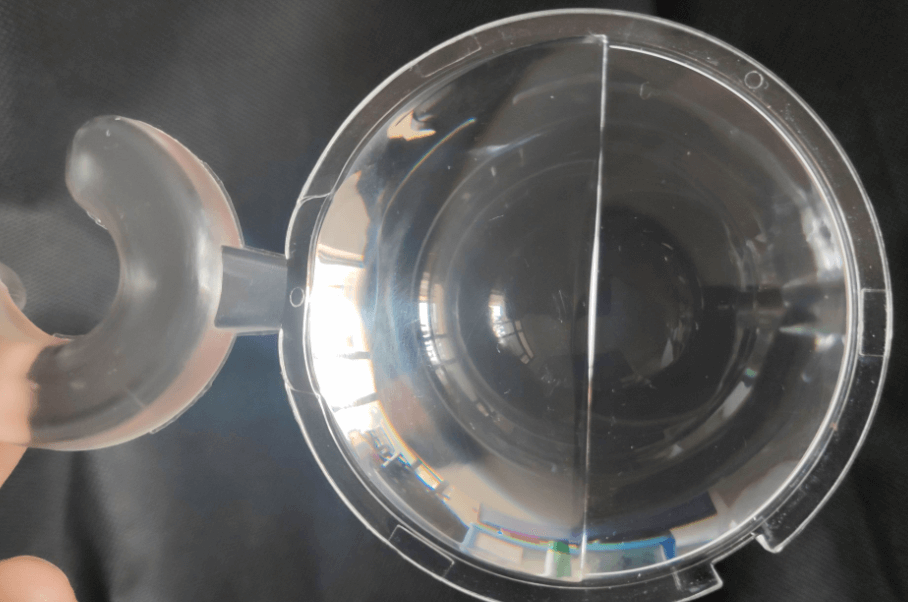
no bubble inside for extra wall thickness PC part, CAR LIGHT LENS
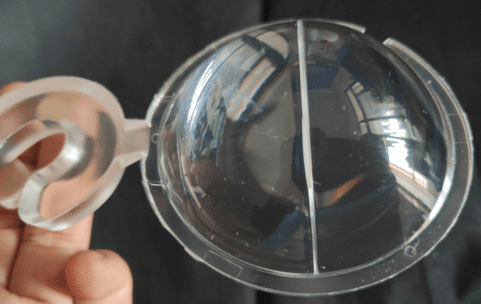
NO SURFACE SINK MARKS
2# CASE
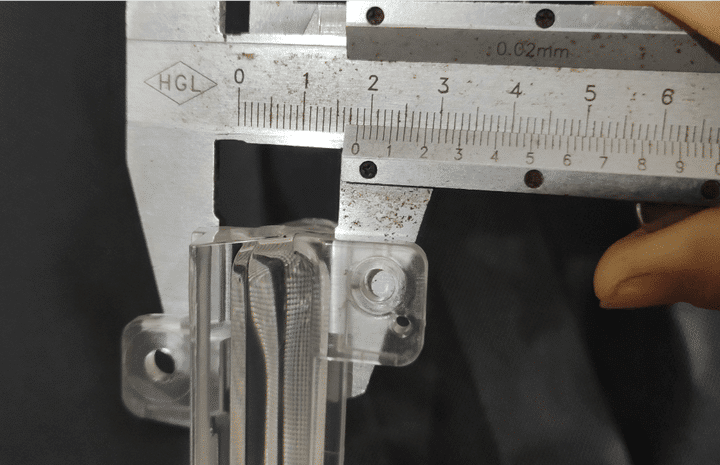
WALL THICKNESS 18MM, PC INJECTION MOLDING
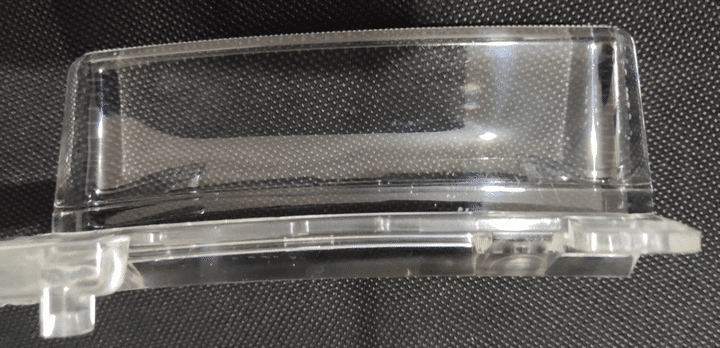
SMOOTH SURFACE, WITHOUT BUBBLE INSIDE
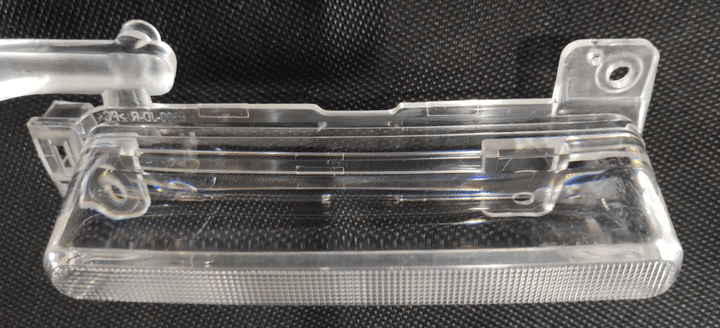
NO SINK MARKS
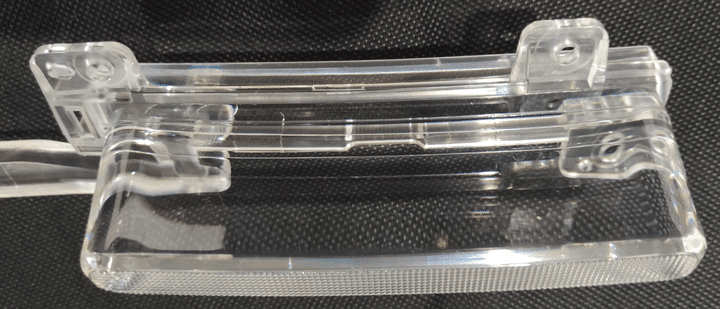
NO BUBBLE INSIDE, NO SINK MARKS
-
What is Polycarbonate injection molding?
Polycarbonate resin exhibits excellent properties like high transparency, stiffness, toughness, and creep resistance and can inject at a variety of temperatures.
Polycarbonate melt viscosity is sensitive to temperature but little to shear rate.
The polycarbonate resin has no melting point but has a very high viscosity, and it hydrolyzes at high temperatures.
PC injection is easily cracked.
Increasing the PC injection molding temperature is an effective way to increase the fluidity of the melt instead of increasing the pressure.
To reduce the pressure loss of melt, the runner path and gate should be short and thick; simultaneously, a higher PC injection molding pressure must be maintained.
The resin PC must be sufficiently dry before injection molding so that the water content does not exceed 0.02% ;
In addition, the PC resin should be insulated during the PC part injection molding to prevent re-absorption;
Not only should the design of a reasonable PC molded product be ensured, but also the process of Poly-carbonate injection molding should be properly controlled, for instance, by increasing the mold temperature and further processing to reduce or eliminate internal stress.
The Poly-carbonate injection molding process should keep adapting to the conditions of the PC product over time.
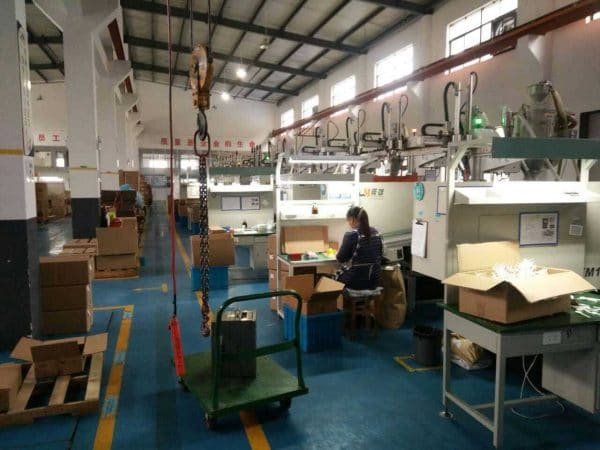
Process:
Drying of raw materials
Even in very low moisture, poly-carbonate injection molding can cause hydrolysis, breakage, molecular weight reduction, and strength reduction.
Therefore, before the molding, the moisture content of the polycarbonate raw material should strictly be below 0.02% to avoid a decrease in the mechanical strength or the bubbles and silver streaks on the surface.
PC is extremely sensitive to water, so it must be fully dry before injection to reduce its water content to below 0.02%.
https://www.youtube.com/watch?v=J2Dk0GBVDKY&feature=youtu.be
-
Injection temperature
Poly-carbonate injection molding depends on the shape, size, and structure of the product.
Generally, the temperature is between 270 and 320 °C in the molding.
If the material temperature is too high, over 340 °C, the PC will decompose, the product's color will become darker, and defects such as silver, dark stripes, black spots, and bubbles will appear on the surface.
At the same time, physical and mechanical properties are also dropped significantly.
PC is also sensitive to temperature; melt viscosity decreases with increasing temperature.
Barrel temperature is 250 ~ 320 ° C. (preferably not more than 350 ° C), and appropriate barrel temperature is good for PC plasticization.
If necessary, the internal stress should be removed by annealing:
The oven temperature is 125~135°C for 2 hours and naturally cooled to normal temperature.
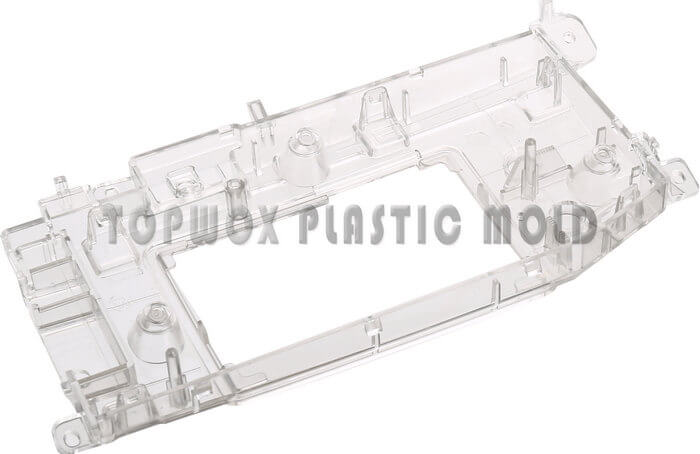
-
Injection pressure
injection pressure greatly influences the physical and mechanical properties, internal stress, and molding shrinkage.
It has a great influence on the appearance and releases property of the products.
Too low or too high injection pressure will cause some defects in the products. The injection pressure is controlled between 80-120 MPa.
For thin-walled, long-flowing, complex-shaped products with small gates, to overcome the melt flow resistance and fill the cavity in time, the higher injection pressure is selected. (145 MPa).
Due to the poor fluidity, high-pressure injection is required for poly-carbonate injection molding. Still, it is necessary to eliminate the large internal stress of the parts (may cause cracking) later.
-
Holding pressure and time
The holding pressure and the holding time also greatly influence the internal stress of the PC product.
If the holding pressure is very small, the product is difficult to fill and firm.
There are usually shrinkage marks on the surface and a vacuum blister inside.
And if the holding pressure is too large, large internal stress can easily be around the gate.
In processing, high temperature and low pressure work together to solve this problem.
The choice of holding time should be determined by the thickness of the product, the size of the gate, the temperature of the mold, etc.
Generally, the small and thin products do not require a long holding time.
On the contrary, the thick wall PC molding products should have a longer holding time.
The length of the holding time is determined by the gate sealing time.
-
Injection speed
There is no obvious influence on the performance of Poly-carbonate injection molding.
A thin wall, small gate, or deep cylindrical object is generally injected at medium or slow speed, preferably multi-stage injection:slow-fast-slow.
-
Mold temperature
Mold temperature control: 85~120 °C, generally at 80-100 °C.
For complex shapes, thin-wall Poly-carbonate part injection molding, the temperature can increase to 100-120 ° C, but it can not exceed the distortion temperature.
The mold wall temperature could be high to reduce the temperature difference between the mold wall and the PC material part, reducing the internal stress inside.
-
Screw speed and backpressure
Due to the high viscosity of PC melt, it is beneficial to plasticize and help good venting.
The rotation speed of the screw should not be too high.
Generally, it is suitable for 30-60r/min.
The backpressure control is preferably between 10-15% of the injection pressure.
-
Additives
Poly-carbonate injection molding should strictly control the use of release agents in the process, and the use of recycled materials should not exceed three times, and the usage should be below 20%.
-
Mold requirements
1) Design the runner as big and short as possible.
For less pressure loss, plastic mold adopts circular cross-section runners.
And runners need grinding to reduce the flow resistance of the melt.
2) The injection gate can be of any type, but the cooling water channel diameter is not less than 15mm.
-
Injection machine requirements
The maximum injection volume (including runners, gates, etc.) of the Poly-carbonate injection molding product is required to be no more than 70-80% of the nominal injection volume;
Clamping pressure: 0.47 to 0.78 tons per square centimeter of finished product projected area (or 3 to 5 tons per square inch);
Machine size: The weight of the finished product is about 40 to 60% of the capacity of 1 shot.
If the machine is expressed in polystyrene (Aussie), it needs to be reduced by more than 10%.
Screw: The length of the screw should be at least 15 times of diameter, and the L/D is 20:1. The compression ratio is preferably from 1.5:1 to 30:1.
The stop valve at the front end of the screw should adopt a sliding ring type.

Why silver streaks and how to prevent in poly-carbonate injection molding?
Silver streaks refer to the pattern of streaks formed by water in plastic when the Poly-carbonate particles are not entirely dried before molding due to inadequate drying procedures in the manufacturing process.
Or, if the sufficiently dried material particles remain in the hopper for longer than intended, the absence of adequate insulation will cause the hopper to re-absorb moisture, resulting in a larger than specified water content.
The resin degrades during the melting process when the moisture in particles vaporizes due to high temperature in the cylinder.
The Co2 accumulates inside the molten resin, and when filling, it flows into the cavity with the Poly-carbonate to form silver streaks.
As a result, the plastic part is severely damaged and often appears with a silver streak along its surface. This type of condition is relatively common and easy to identify.
The part is usually distributed more uniformly along the flow direction and occasionally on the entire surface.
The key to removing these silver streaks is to dry the pellets completely, and the moisture must be below 0.02 percent.
For this reason, it is important to control the drying conditions for raw materials and to measure the water content of the pellets before molding.
https://youtu.be/6EAIc293c6E
Tips
For the production of polycarbonate injection molds, a standard inspection process can be used.
Take two small glasses and sandwich one pellet between those two glasses, and heat the plates at 280-300 degrees.
As the pellet is gradually heated and melted, it is pressurized to be crushed. Observe for bubbles in the material; if there are none, it is ready for the next step; if there are bubbles, it needs to be dried more.
If moisture absorption in the hopper is causing the silver streaks, it is recommended that the heat preservation device be installed or improved.
And the amount of each feed should be controlled not to cause the dry pellets to stay in the hopper for too long and absorb moisture again.
In general, the maximum stay should not exceed 30 to 60 minutes.
Currently, most of the hopper's heating and heat preservation devices are infrared bulbs installed in the upper region of the hopper, and the power can be adjusted based on the size of the hopper.
An average heating capacity of 25 to 30 W per square meter of the area is required.
-
Decompose
The silver streaks result from the resin's superheated decomposition, which generates a gas (carbon dioxide), resulting in the appearance of silver streaks on the plastic surface.
The melt thermally decomposes for many specific reasons.
- the barrel's temperature is too high;
- dead angel in the barrel or nozzle;
- the residence time of the melt in the barrel is too long;
- the molecular weight of the resin has been reduced.
Therefore, the impact resistance, the surface texture, and the performance of the plastic part are all affected.
Their appearance can recognize this type of silver streaks, and their distribution on the plastic parts does not follow a regular pattern.
Moreover, the presence of a decomposing silver streak can often be accompanied by the darkening of the plastic parts or the appearance of brown spots, which are especially clear in the hot runner, which can be used to determine if the material has decomposed.
PC material decomposes due to various reasons, and the appropriate interventions should be taken according to those causes.
- If the barrel's temperature is too high, the section's temperature should be lowered;
- If the barrel or nozzle has a dead angle, clean it and get rid of it;
- If it's from too long a melt residence time, the molding cycle should be shortened.
- If still failing, the injection molding machine could be replaced with one having a smaller processing capacity.
-
Structure
The streak of silver is caused by the mixing of air with molten material in the molding cavity. This is due to the unreasonably complicated structural design of the plastic parts or insufficient or inconsistent wall thickness.
They cause the material to expand or contract rapidly when the mold is filled with molten material.
This type of default mainly affects the appearance of plastic parts rather than their strength and impact resistance.
Structural silver streaks are characterized by the fact that they are fixed in shape and position when the process conditions are set.
The silver wire is typically found along the injection direction, and the silver streaks are generally located behind the abrupt cross-section changes.
The structural silver streaks are created by sudden changes in cross-section and significant irregularity in wall thickness. Consequently, the plastic parts often have surface defects, such as depressions and shrinkage, and sometimes even bubbles are generated within the plastic parts.
Structural silver streaks are prevented by adjusting the injection speed. When the cross-section of the plastic part does not change much, the injection speed can be lowered.
When the injection speed is low, the flowing material can be smoothly introduced into the mold cavity, which results in the flow material not being mixed with air when passing through those sections, and silver streaks can be avoided.
The short shots may be caused by excessive slow injection speed, which may require adjusting other process conditions.
When there is a great variety of cross-sections, the injection can be increased to a higher speed and injecting pressure so that the gas is forcibly released from the parting surface.
If the silver streaks cannot be eliminated by increasing the injection speed or increasing the injection pressure, improvements in the plastic parts structure and the mold venting system may be helpful.
-
Sprue and runner
The silver streaks occur due to an unreasonable design of the gating system or partly blocked gates.
The causes and solutions :
(1) A large sprue draft causes the flow material to leave the sprue walls at the initial injection stage, which causes gaps.
When the mold cavity is gradually filled, the air is mixed within the flow material and trapped in the mold cavity to cause silver streaks to appear.
The main feature of silver streaks is that they are distributed in the injection direction.
To eliminate streaks, injecting resin into the air first and subsequently checking if the sprue is appropriate could avoid the possibility of resin decomposition.
If the angle exceeds 10 degrees, the above can occur.
A 4-6 degree angle is suitable.
If the angle is too small, demoulding will be difficult, and material flow will be hard.
Adjusting injection speed helps silver streaks, but the most common solution is to trim or replace the sprue.
(2) A design where the gate cross-section is too small can lead to turbulence, causing the melt to mix with the air, leading to the generation of silver streaks near the gate.
The streaks in this type are predominantly radial in the distribution in the direction of injection with the gate as its center.
Enlarging the gate or changing the dimensions of the gate to eliminate the streaks can solve this.
It is more effective to reduce the injection speed when the gate is under-reworked.
(3) The cold material at the nozzle causes the gating system to become blocked during the injection process.
The blockage of the runner or gate is similar to that caused by a gate that is too small.
When identifying silver wire, one should seek to detect traces of cold material in the injection system.
The solution is to raise the temperature of the material in the mold and the temperature of the nozzles.
-
Venting
This type of silver streak occurs due to air being trapped within the PC flow path and cannot be expelled during the molding process.
The principal characteristics of this condition are that distinct weld lines accompany it and that silver streaks often occur near weld lines, while they do not appear in other parts.
https://www.plasticmoulds.net/polycarbonate-injection-molding.html
Thanks, l like you! l am tkbmold, injection molding parts made in china
ReplyDelete