Real cost of plastic mold tool and injection molding
Plastic Mold and Injection Molding Cost
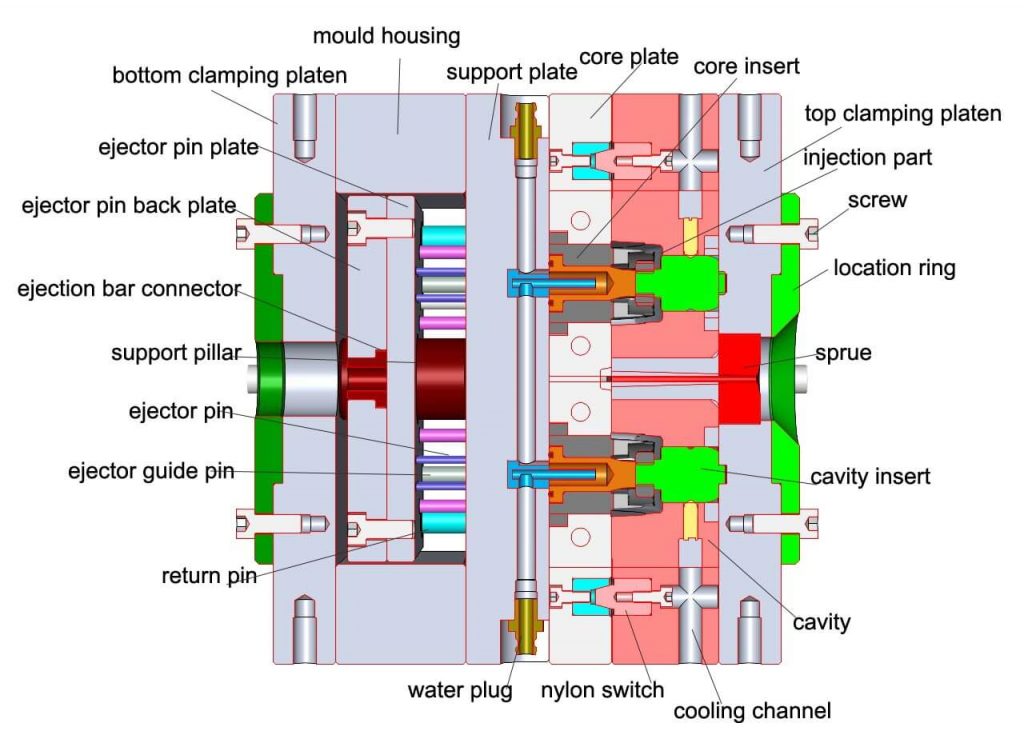
plastic mold cost
Many buyers who purchase injection molds from China are solely focused on saving money.
However, this isn’t the right attitude to take since you’ll ultimately want a mold that works properly and is reliable instead of just being cheap.
To determine How much a plastic mold tool and injection molding, some factors are considered:
- part complexity,
- cavity count,
- tolerances,
- tooling materials,
- cam mechanisms in the tool,
- tool life expectations,
- resin grade and aesthetics.
These costs are indeed amortized over the number of parts to be produced; however, the real cost includes the time required for the molding process and the processes needed to build the parts.
Thus, a hot-runner tool may cost more than a two-plate tool initially; however, they do not require a separate operator to separate parts from runners, as the part cost may be lower than if the injection molding plant is used a two-plate tool.
Purchasing departments should not have sole responsibility for purchasing tools because there are too many factors that they may not understand. Tools should be required to be specified beforehand. The goal is to have the lowest cost for the right tool to make the parts according to specifications by competent molders.
When buying a mold, it is important to pay attention to the areas of interest that need to be addressed. The checklist on mold design and the injection mold specification sheet cover these areas of interest.
In the early stage of product development, the design and sales departments should take mold costs, production costs, and the final piece price into account.
It will enable management to decide your direction. It is not difficult to estimate the cost of a mold, but you should consult all parties concerned.
If you request a quotation for tooling, you should have the preliminary design complete, final drawings, and a sample of the part if possible.
Part drawings and specifications should include the following information:
- 1. Dimensions that determine the complexity of the cavity and part tolerances.
- 2. Various surface finishes are required.
- 3. The requirement for tight tolerance as well as the number necessary.
- 4. In square inches, the area is covered by the part's length and width.
- 5. All functions that operate within the mold (caming, unscrewing).
- 6. Tolerant-based tooling requirement balance.
- 7. Resin was used to form the part.
- 8. Tolerances and part volume should determine the number of cavities.
- 9. Different types of tools include two-plate, three-plate, hot-runner, etc.
Decide on the number of materials and standard components to be used and calculate costs from the suppliers' catalogs after answering the questions above.
Mold makers must prepare a list of manufacturing processes and assembly processes and the various items involved in production; these must include the
- cavity(ies),
- the cooling requirements,
- the location of cooling lines around the cavity,
- the ejector system,
- and any other operational procedures required.
Compute how long each procedure takes, and figure out the hourly wage rate for each procedure. Add in external labor costs for heat treatment, finishing, polishing, surface texture, etc., to get a feel for everything that has to be done.
The purchasing department can achieve greater efficiency and accuracy by acquiring this information, enabling them to evaluate and budget for a specific job more accurately and efficiently.
A first-time mold buyer, particularly one who is unaccustomed to mold design and construction, will often have difficulty compiling this information. Often, the wage rates and length of time required for production will be only estimates.
It is important to collect information from suppliers to determine the exact cost of new equipment.
By specifying how the tooling provider must prepare its quote, the buyer can gather specific information, such as a breakdown of components, functions, and schedules.
The cost of mold design can range from $3000 for straightforward designs with few or no revisions to $7000 for constant revisions. Mold design costs are about 5 to 10 percent of a simple job.
It generally takes between 4 weeks to 10 weeks to design, machine, build, finish, and qualify a tool for injection molding. To avoid shipping and transporting the mold back and forth, choose a tooling source capable of performing injection molding on the tool.
The best way to learn in the mold estimating process is to consult mold builders specializing in molds similar in size and complexity to the one being produced.
Examine the quality of their work and their equipment, processes they use, and the range of services they offer.
Solicit quotes from the tool builders and manufacturers who own molds. If you do not have mold builders, you may need to contract a molder. During this phase, it is important to be able to describe the part requirements fully.
This process can eliminate the additional expense and result in a piece-part price that is even lower. With these abilities, the tool will initially cost more but ultimately results in a piece-part price that outweighs the cost of the tools.
Why those important for injection molding cost
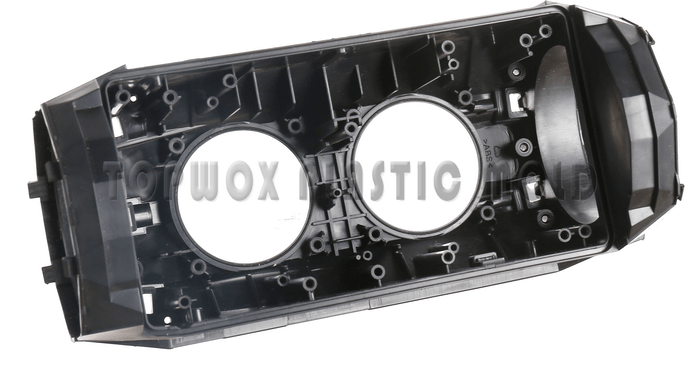
injection molding cost
- Part size- bigger parts mean a bigger mold, which means that bigger steel will increase the steel cost for the injection mold.
- Part design- the more complex a part is, the more detailed the mold has to be. Some complicated parts will require special features to be added, such as lifters or sliders. Therefore, you should be open to advice from your mold maker and see if there’s anywhere that you can alter the part design to save on injection mold costs.
- Materials: Depending on the part material of choice, the injection mold will have to be made of a particular material. For instance, if corrosive plastic-like PVC is to be used, the mold will have to be stainless steel to avoid any damage, ultimately bump the price up.
- Part finish requirements- where parts have high gloss surface requirements, then more expensive steel and precise technical polishing will be vital, adding to the price.
- Production volume- higher volume molds need more cavities, and so the mold will be larger. They also require a higher steel grade to last for longer, which impacts the injection mold cost.
- Country of manufacture- different countries have different wage rates. If your mold is made in a country where labor costs are low, then you’ll naturally save money. In China, the average cost of an injection mold is around 40% less than in western nations.
https://www.plasticmoulds.net/plastic-mold-tool-cost
Comments
Post a Comment