Best Practice in Design of plastic mold
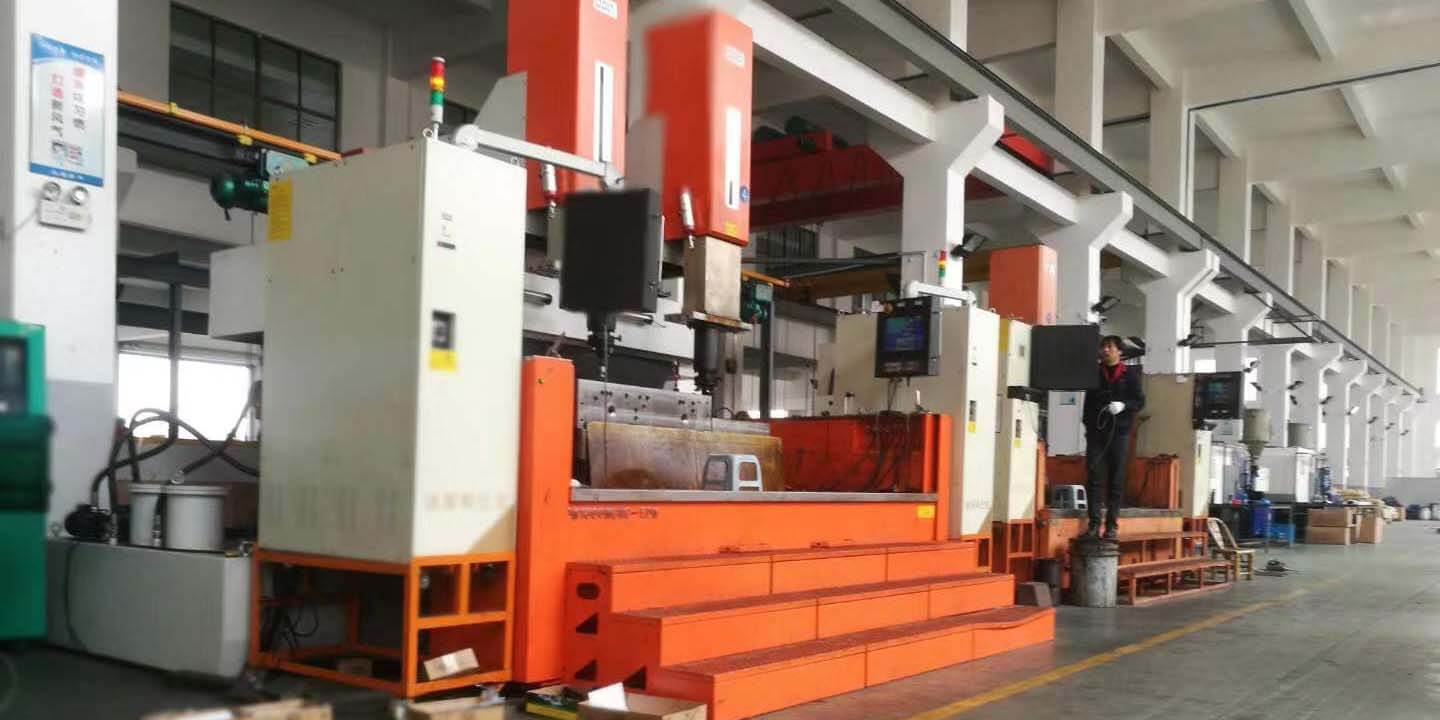
Best Practice in Design of plastic mold
Since the introduction of injection moulding, plastic mouldings have been produced in a huge variety, ranging from the basic to extremely complex. High-complexity mouldings are now possible with advances in injection molding, toolmaking, and machining.
These technological advancements have led to the development of a wide range of standard components that meet the needs of consumers today by providing more and more high-quality products regularly. Utilizing these methods can make it easier to develop and construct tools and reduce both the design time and tool-making time.
Standard components are available which provide solutions to many different types of undercut or ejection problems. Many of the standard components are designed to provide solutions to these problems.
This suggests that wherever these can be successfully integrated into a design, it would be worthwhile to use them to their full potential. Components such as collapsible cores provide a self-contained solution of great value to designers and toolmakers.
When a new component has to be moulded, it is possible to divide mould designs depending upon whether they can be based on existing, proven mould designs or not. An existing design can be used and adapted to the mold design when possible since all bugs have been fixed and their behavior in production is well known.
The need for new solutions for specific problems arises inevitably. Some can be extended from existing solutions; others require a new approach. This makes previous design experience necessary to determine whether a new direction will succeed. Design should, however, try to provide the most simple solution possible to the problem.
In the case of a new mould tool, a sample moulding may often provide beneficial information, such as gate position and size, ejector pin size and location, etc. The mold maker should use an existing mould design with a new part unless it failed to mold it previously. For reliability and product quality, simple designs always beat complex ones. It is also advisable to use tested design and mould components instead of completely new ones.
To gain experience in mould design, one must gain these skills:
- Analyze other existing general arrangement diagrams.
- Toolmaking procedures to be familiarized.
- Understanding the working of mould tools during production.
- Identify amorphous vs. semicrystalline materials, and distinguish the differences.
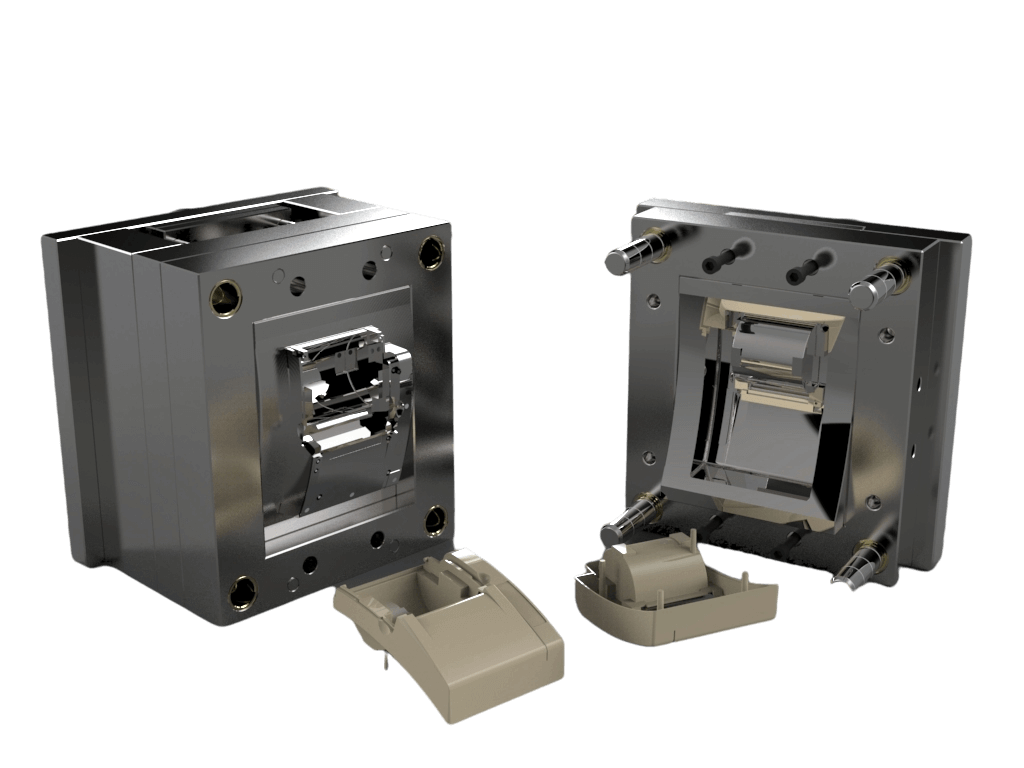
plastic mold
How to?
Analyses of the predesign
In general, it is advisable to conduct some pre-design analysis before starting to design the construction of a building. It is an obvious statement, but you need to qualify it. Design as many moulds as you can first if you are not a mould designer. Develop at least three different approaches for splitting the line, ejection position, and gate position. This is the time to consider cavity construction, water cooling, etc.
Designers should emphasize solving problems, which can be difficult when they have little or no experience in the industry. Look at every moulding and try to detect its shape and how it was formed, its split lines and gates, how it was ejected, and any special features.
GA reading
As a result of this, you also gain a lot of valuable experience. Even experienced designers can't read and understand most GAs in ten minutes. To fully understand how the tool design works in most cases, it takes hours rather than minutes.
This can be illustrated by the fact that a toolmaker will often contact the designer to clarify certain aspects of the drawing that he does not understand. If the drawing is unclear or even incorrect, it may be that the toolmaker is having difficulty understanding it; it may also be that the drawing is too complex for the toolmaker to comprehend.
It is not as important whether the designer has committed an error or whether the toolmaker does not understand the drawing. It is the willingness of both parties to resolve the problem. Such discussions frequently occur in practice.
Concepts related to toolmaking
Mold tool designers should ideally have some experience in toolmaking before designing a mold. There is no doubt that it is a prerequisite that you be certain that what you are designing can really be produced.
For those who have not had any experience in toolmaking, it is recommended to regularly visit a toolmaker to acquire an understanding of the various toolmaking techniques. In these circumstances, most toolmakers are reasonable and usually quite willing to conduct a short teaching session. Designing mould tools does not require a high degree of skill or expertise on the part of the toolmaker. Despite this, it is impossible to design mould tools without knowing whether what is being designed can be produced.
A mould design must also reflect the unique plant and equipment of different toolmakers. Others are equipped with relatively basic operations, while others have sophisticated computer-controlled machining centers. In addition, all tool makers have the following common equipment and machinery:
- A drilling machine
- Turning lathes
- Machines for milling
- Machines for grinding surfaces and cylindrical surfaces.
- Electro discharge machining
Examining Mould Tools
This is a noticeable shortcoming when you consider that many mould designers never see their production designs. For two reasons, all designers would be required to participate in the initial sampling trials:
- It is common for molds to be complex and have many intricate details, which must be explained to the sampling technician. Several broken items have occurred due to incorrect understanding of complex unscrewing mechanisms and phased latch controls.
- Mold designers can obtain valuable insight into their design and implement modifications to make the product more efficient.
A lot of instruction can also be obtained from watching other mould tools in operation to observe other people's designs. It is also a good idea to inspect mould tools as they are being serviced or repaired. This can highlight areas for improvement in the future, such as seized-up parts, excessive flash, excessive wear, etc.
An Overview of Good Design Practices
- Make your design as simple as possible.
- Utilize standard components to the fullest.
- Avoid new, unknown designs and use tested designs.
- Analyze any existing samples that indicate gate positions, block locations, sinks, distortion, etc.
- Make sure the toolmaker has the correct equipment.
- Conduct sampling trials for feedback and to guide sample technicians.
https://www.plasticmoulds.net/practice-design-of-plastic-mold.html
Comments
Post a Comment