#1 China overmolding company for insert molding,co-injection,2k molding
China overmolding and insert molding
Want to find a trustworthy manufacturer and designer in China that specializes in overmolding and insert molding so that you can depend on their work to be reliable and affordable? Providing reliable and budget-friendly services of overmolding and insert molding, Topworks Plastic Mold is dedicated to offering the highest quality products at a cost-effective price.
With over ten years of experience, we offer our customers unmatched knowledge and experience in the field of designing, manufacturing, and tooling of overmolding and insert molding products at competitive prices across the globe while maintaining a commitment to quality.
The wide range of overmolding and insert molding services we offer means that we are in the unique position of being able to create overmolding and insert molding tooling and manufacture overmolding and insert molding parts from concept to reality.
The simple nature of our processes provides an extremely fast and simple injection molding process for the development and production of complex work-in-progress and prototype parts.
What overmolding and insert molding we supply?
As a supplier of high-class rubber and overmolding,insert molding and co-injection parts, Topworks has successfully supplied the services for single and multi-component 2K molding projects in the various fields of
- Personal care,
- Automotive parts,
- Medical care,
- Cosmetics and electronic products
and casting the technological value to more production throughout the world.
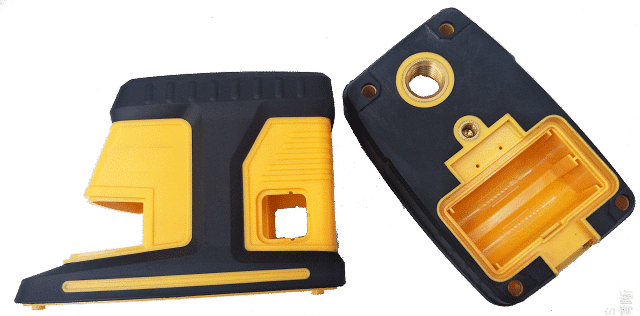
Why choose us for overmolding and insert molding ?
- Precision manufacturing at ±0.01mm
- Implementing advanced overmolding(insert molding) product designs
- Standardization of mold parts
- Rapid and high precision positioning of mould components
- Manufacturing process control from beginning to end to satisfy client's overmolding(insert molding) demands
- MAKINO (V99) Large multi-cavity multi-component mold size control
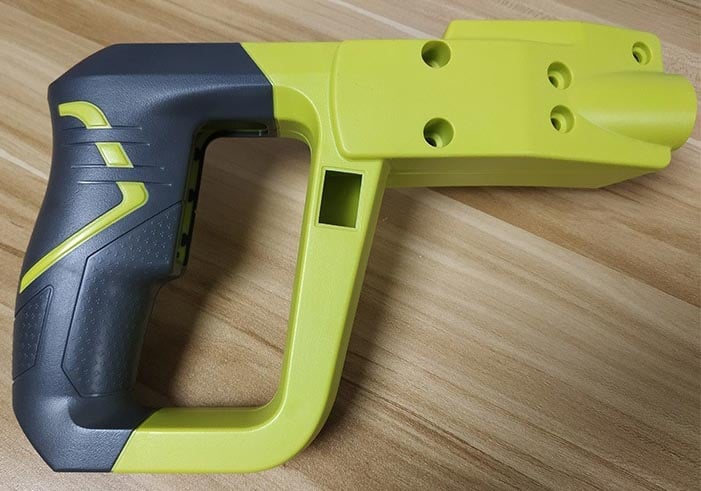
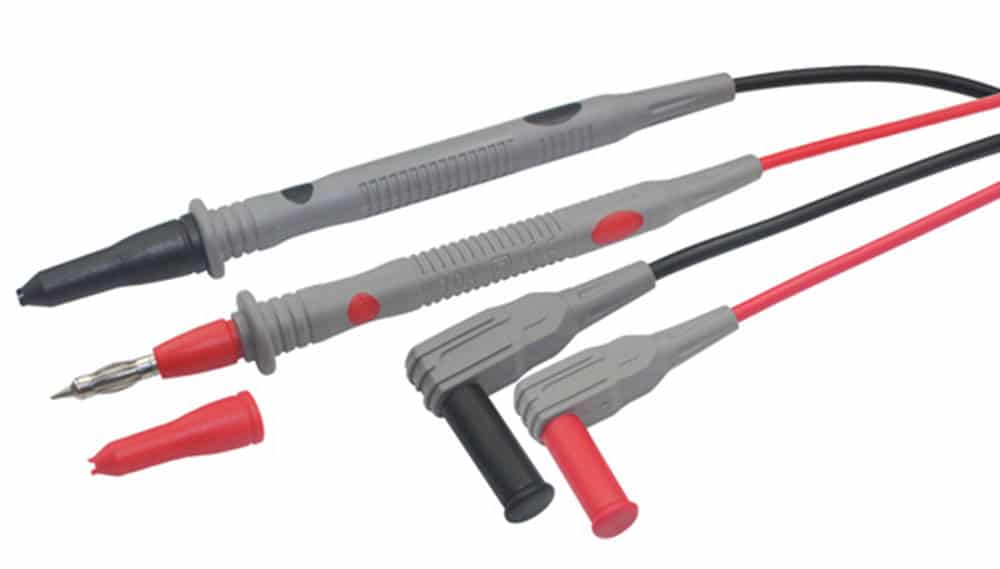
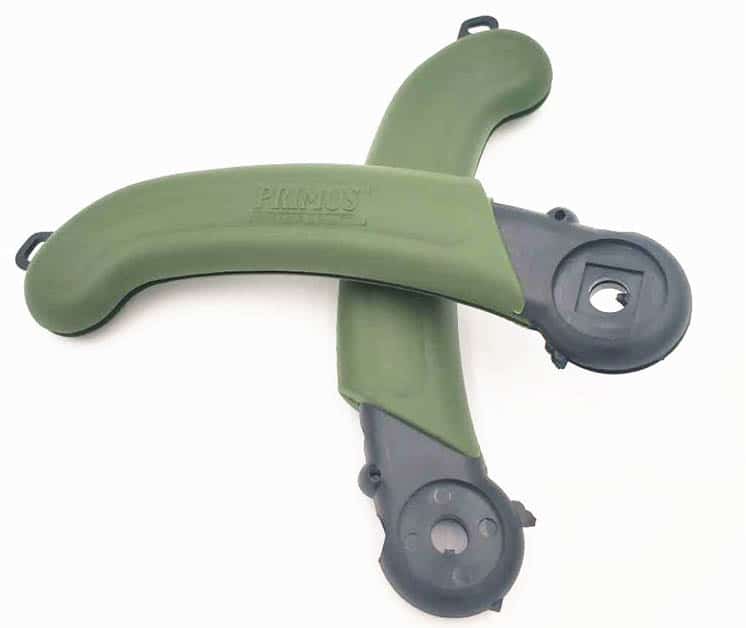
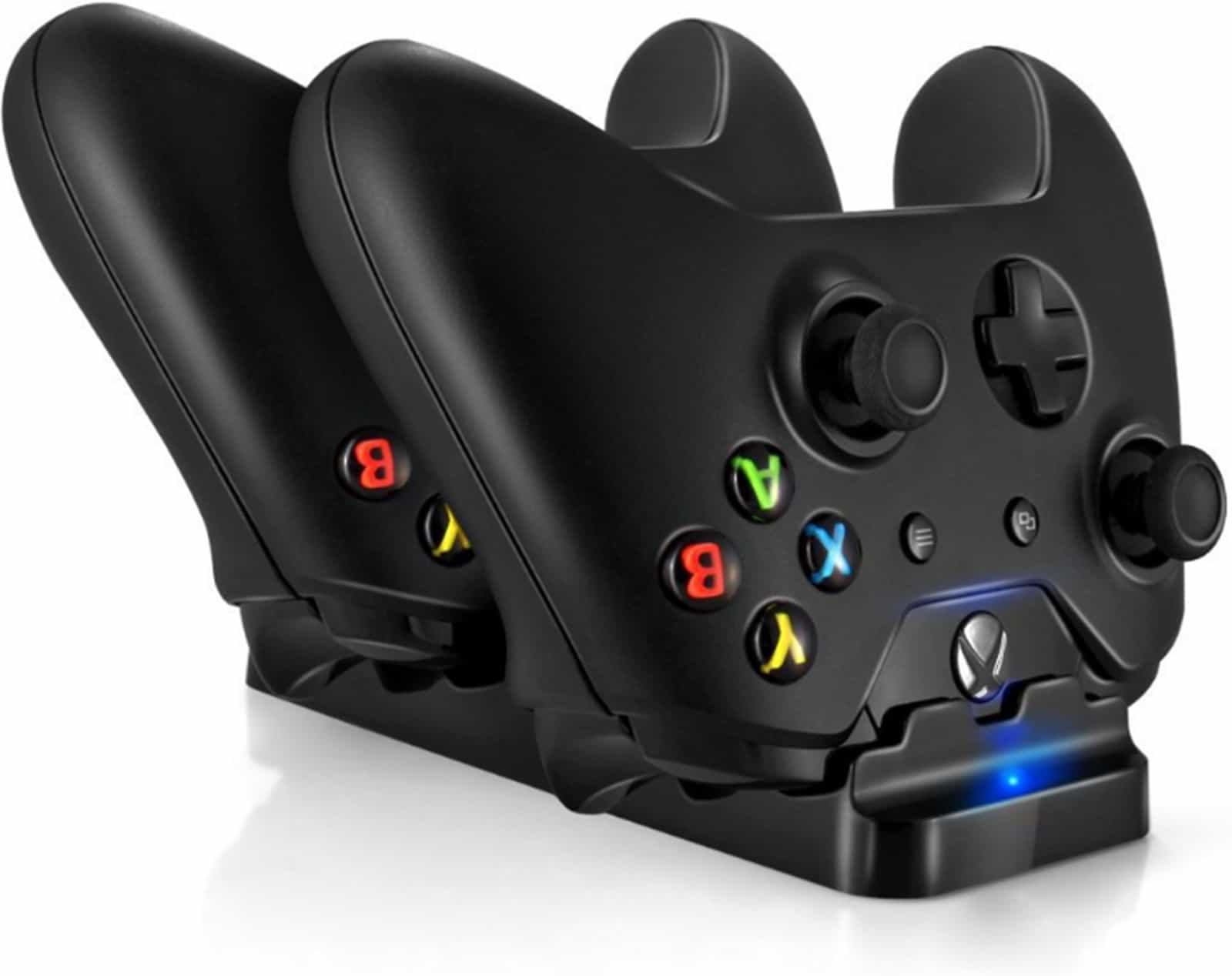
Overmolding Project Management
- One to one project engineer contact
- Plan & track overmold manufacturing process
- Update customer's requirements & feedback
- Arrange delivery of trail overmodling samples
- On site management of mold until mass production begins
Overmolding After-sales Service
- International service capabilities
- Rapid response support (7x24 hrs)
- Professional communication (English speaking engineer over 10+ yrs)
Principle of two-color injection molding
Double color mixing injection molding
It has two barrels, and the structure of each barrel are the same as those of ordinary injection molding barrels.
Each barrel has its own passage to the nozzle, and opening and closing valves 2 and 4 are also installed in the nozzle . During molding, after the molten material is plasticized in the barrel, the opening and closing valves 2 and 4 control the sequence of molten material entering the nozzle and the proportion of discharged material.
And then the molten material is injected into the mold cavity from the nozzle. Various plastic products with different color mixing effects can be obtained.
Double Pattern Injection Molding
It also has two barrels 1 and 5, and its nozzle structure is somewhat special.
Besides the normal nozzle function, it can also be rotated by a gear 3 installed at the rear. During molding, melting materials with different colors are plasticized in the charging barrels 1 and 5 respectively, and the gear 3 drives the rotating shaft 4 to rotate, so that melting materials with different colors alternately enter the mold cavity, thus obtaining plastic products with different colors and patterns radiating from the center to the periphery.
two-color injection molding requirements
Material requirements
The 2 materials for two-color injection molding must meet two basic compatibility demands: adhesion and compatibility.
Design of Soft and Hard material
There must be a certain melting points temperature difference between the two materials.
Generally, the temperature difference is to be 60℃, and it is recommended to be at least 30℃. The melting temperature of the first shot material is high. Generally, the first shot material is PC or PC/ABS, and the second shot material is TPU or TPE.
PC injection molding is 0.6-0.7mm thick and software material injection is 0.4mm or more.
over-molding need widen the contact area for 2 material as much as possible, making grooves increase the adhesive force, or adopt core pulling in the first shot, inject the second material into the first shot, and rough the surface of the first shot mold should be as much as possible.
Advantages of Two-color Injection Molding
Compared with classic injection molding, two-color injection molding has the following advantages:
- The 2K molding main raw materials can use low viscosity material to reduce the injection pressure.
- The 2K molding main raw materials can use recycled plastic, both environmental friendly and economy.
- Meet the special requirements of some products, make plastic parts more beautiful and colorful. For example, soft plastic is used for the surface material of the thick product, and hard plastic or foamed plastic is used for the main body to reduce the weight.
- lighter or cheaper plastics can be used in unimportant parts of over-molding parts to reduce product cost.
- The expensive and special performance of plastic material could be used on the important and special area , such as electromagnetic interference prevention, high conductivity and other plastics
- Proper combination of surface material and core material can reduce residual stress of 2K plastic parts, increase mechanical strength or optimize surface performance of products.
- Products surface like marble texture can be obtained.
https://www.youtube.com/watch?v=wwyQU4YHfPU
2K Injection molding is that granular or powdery plastic is fed into a heated barrel from a hopper of an injection machine, heated and melted, plasticized into a viscous fluid melt.
The material was pushed by the high pressure of a plunger or a screw of the injection machine, injected into a mold cavity at a large flow rate via nozzle and gate, maintained in the shape given by the mold cavity after pressure maintaining, cooling and shaping for a certain period of time, and then opened and molded to obtain plastic products.
the above is an injection cycle.
The injection molding process can be abbreviated as:
feeding-plasticizing-injection-pressure maintaining-cooling-demoulding.
The details cycle:
- (1) The heating and pre-plasticizing barrel and screw will forward ,convey and compact the plastic from the hopper under the drive of the transmission system.
Under the mixing action of shearing and friction of the heater outside the barrel, the plastic melts inside the barrel . A certain amount of molten plastic has accumulated in the head of the barrel.
Under the pressure of the melt, the screw slowly recedes.
The retreating distance depends on the amount required for one injection by the metering device.
When the predetermined injection amount is reached, the screw stops rotating and retreating.
- (2) Mold clamping, the mold clamping mechanism on the injection machine pushes the movable mold half and the fixed mold half to close tightly so as to ensure that sufficient clamping force.
- (3) The injection section moves forward. When the mold close, the entire barrel moves forward to make the nozzle of the injection machine fully fit with the sprue of the mold.
- (4) Injection and pressure keeping. After the mold close and nozzle completely seal the sprue on the mold, the injection hydraulic cylinder shot the high pressure oil to push the screw to move forward inside the barrel, injecting the melt accumulated in the head of the barrel into the cavity of the mold with sufficient pressure.
The plastic volume will shrink after the temperature drop.
In order to ensure the compactness, dimensional stability and mechanical properties of the plastic products, a certain pressure should be maintained on the melt in the cavity of the mold to supplement the melt.
- (5) Pressure Relief .When the melt at the gate of the mold freezes, the pressure can be released. At the same time, the melt is cooled and solidified in the mold cavity to make a plastic product.
- (6) mold opening and products ejection .After cooling and shaping, the mold clamping mechanism opens the mold and pushes out the plastic products in the mold.
https://www.plasticmoulds.net/overmolding
Comments
Post a Comment