4 Stages of Quality Control in Plastic Injection Molding
There are generally 4 different stages of quality control that are performed in plastic injection molding. The first stage is the design stage, followed by quality planning and the control of each molds and test sample produce. This is followed system certification and production quality control.
Design Review
The first stage of quality control is design review. This review should take place with both internal and external designers or engineers. The purpose of this stage is to make sure that all designs are reviewed for accuracy before moving forward into production. You can use 3D printing as a way to check your design before committing resources to producing a full-sized model. The benefits of using 3D printing are being able to see what your product will look like before investing in manufacturing equipment and materials, as well as having a true sense of scale for final production models once they're complete.
This stage involves creating a detailed plan of how to manufacture your product. The plan includes the following:
Product design
The design of your product will determine how much material is needed for each part, as well as how many parts you'll need for each product batch. If you're using more than one material for your product, then this stage also includes deciding which materials will be most efficient for use during injection molding.
Part layout
Part layout refers to how you arrange all of the parts on your product when it comes time to manufacture it. The arrangement of parts can affect how quickly they're made and what materials are used during injection molding. For example, if you have several parts that could be molded using two different materials, then choosing one over another might save time and money during production since there will be less material to use.
Mold Pre-Production Part Inspection
Quality control is the process of ensuring that a product meets all requirements. It's an essential part of any manufacturing process, and it can be broken down into four stages: mold design, pre-production inspection, production inspection and post-production inspection.
Mold Design
This is where you prepare for the production of your product by designing the mold that will be used to produce it. The mold is then made using a variety of materials, depending on what you're making. For example, molds used in injection molding are usually made from aluminum or steel alloys, while some other processes use ceramic materials or even sandstone molds instead.
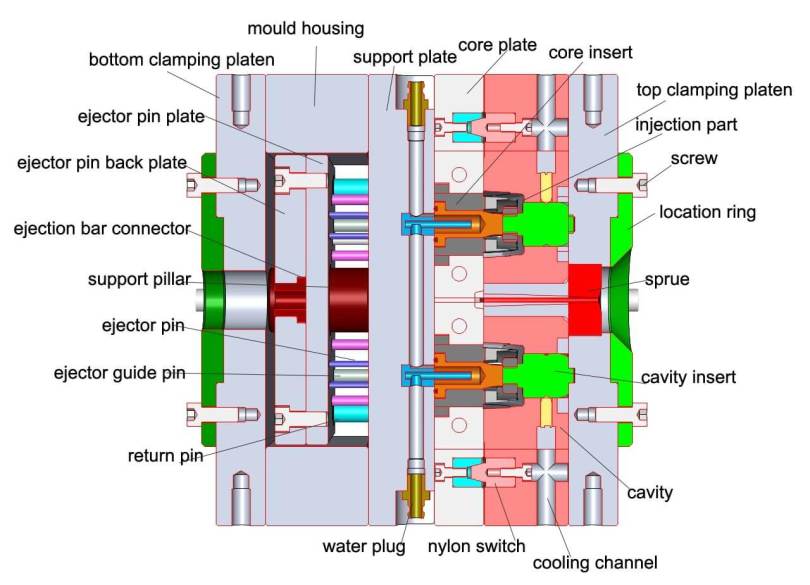
Pre-Production Inspection
This stage involves inspecting the parts produced during the injection-molding process before they're shipped out. It's also known as "first article inspection." This ensures that each part meets specifications and any defects are identified before they reach customers' hands. Inspectors perform visual checks on each part and use measuring equipment to ensure that sizes, weights and tolerances are correct according to your specifications.
They also test functionality by testing whether parts fit together properly and whether they seem strong enough for use in their intended application (they may not always work perfectly straight out of the mold, after all). In addition to visual inspection and testing, inspectors may also take x-ray scans of parts or perform other types of non-destructive testing (NDT) to ensure that they're safe and functional.
The main types of defects that can occur during plastic injection molding are:
- Non-uniformity in color and texture
- Misaligned or missing holes
- Incorrect size of holes, thickness and other dimensions
- Incomplete filling of cavities (flash or short shot)
In Process Quality Control
The quality control process begins with raw materials that must be checked to ensure they meet specifications before they are used in the injection-molding process.
The second step is to check the injection-molding machine's temperature and pressure controls, as well as all of its other components, so they are working properly. This step ensures that the material will be properly melted before it enters the molding machine, which helps eliminate defects such as air bubbles in finished parts or poor surface finish on molded parts.
The next step involves checking for particulates (foreign materials) in the molten plastic that could cause problems during injection molding. Once particulates have been removed from the plastic, it can be injected into a mold.
The final stage of quality control involves checking for voids or other defects in molded parts, ensuring that each part comes out of an injection-molding machine properly formed and free of defects.
Quality control ensures that all parts coming out of the injection mold are of high quality and meet customer requirements.
There are four main stages of quality control in plastic injection molding:
- Inspection – The first stage involves inspecting all parts coming out of the injection molding machine using a visual inspection, weight measurement and dimensional check (using a micrometer).
- Testing – In this stage, samples are taken from each batch for testing. The test results are used to determine if there are any defects in the material or tooling.
- Repairs – If there are any defects detected during testing, they will be repaired before continuing with mass production. Repairs can be done by replacing defective parts or modifying them to make them work as required by customers.
- Documentation – The final stage involves documenting all repairs made so that it can be referred back to when needed later on during future production runs.
It provides the following benefits:
- Ensures that all products meet standards or specifications
- Identifies defective parts and materials
- Helps identify opportunities for improvement
- Tracks product manufacturing costs
Final Inspection
1) Final Inspection - This involves checking each part for defects before it leaves the factory. Each piece is inspected by hand before being packaged and shipped out so that only perfect pieces make their way into customers' hands. This process ensures that the product is of high quality and is free from defects,including scratches, bubbles or other imperfections. If any problems are found, they’re corrected before packaging and shipping.
The inspection is carried out by highly trained individuals who are able to identify any problems with the parts and materials used in production. This means that only perfect products are shipped out, ensuring that customers receive only the best quality goods.
2) Package - The package must be strong enough to withstand any damage during shipping. It should also include instructions on how to install or use your product safely in case something goes wrong on your end. If possible, consider using recyclable packaging materials whenever possible because they are better for both your environment and ours!
Final words:
It is also possible to automate two or more of these stages so that certain quality tests are done automatically, immediately, and repeatedly. The number of quality checks depends on your equipment and is subject to change according to the number of production runs in each area. However, a system like this would improve overall plastic injection molding manufacturer efficiency.
https://www.plasticmoulds.net/4-stages-of-quality-control-in-plastic-injection-molding.html?feed_id=784&_unique_id=6352105c7b2a0
Comments
Post a Comment