history of mold designer
After the Second World War, people started using plastics more and there was a need for people who could design molds for plastic products. At first, these molds were made by artisans in tool and die maker shops. These artisans were skilled in making accurate steel tools and dies, and they often worked closely with the injection molding company (the person who would use the mold to make the product) to make sure the mold was made correctly.
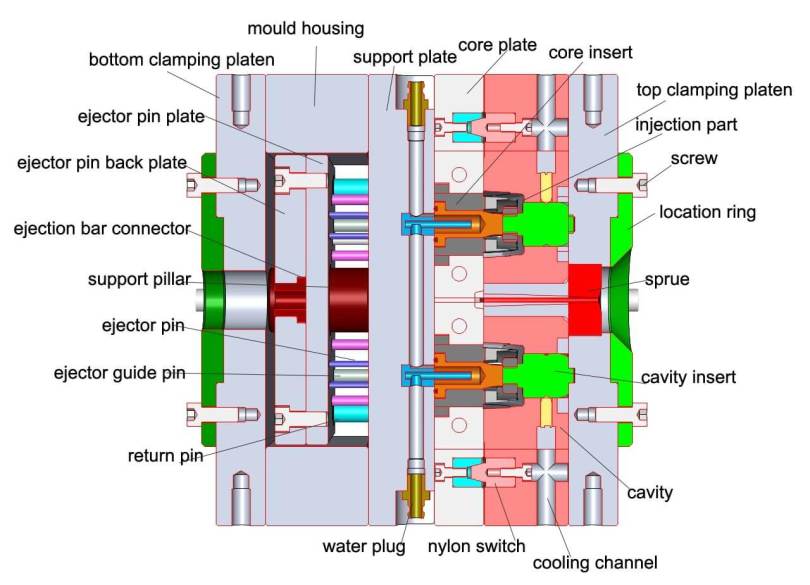
The molder draws a picture of how the mold should look. The boss then oversees the machinists as they make the parts for the mold. Once the mold is finished, the boss tests it to make sure it works well. These molds were usually good for the few existing plastics molding materials at the time and were satisfactory for the low productivity expected from such molds.
In the past, plastics were not very good quality and could only be used for a few things. But now there are much better plastics that can be used for lots of different things. And people want to be able to make these things faster.
The traditional tool and die maker had to do more and more work, so a new type of worker, called a mold maker, was created. Mold makers were good at machining and assembling, but they also needed to know a lot about the materials they were using, like plastics. Sometimes the people who supplied the materials didn't know enough, so they had to rely on the mold makers for help.
The molder was in charge of the features the mold should have, and often chose the materials it was made of. Eventually, all this information had to be put on paper so that machinists could make the mold and put it together. Draftsmen or designers became responsible for this task.
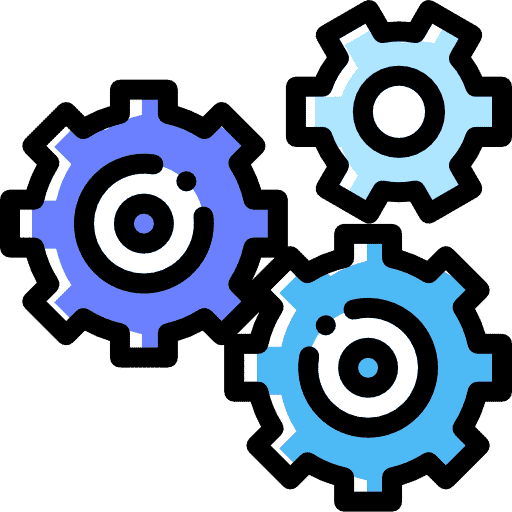
Mold designers are people who design molds for a living. They work with the molder (the person who makes the mold), the mold shop (the place where the mold is made), and the plastics suppliers (the people who make the plastic) to make sure that the mold is made correctly.
The mold designer is responsible for the construction and functioning of the molds. The mold maker builds the mold according to the instructions given by the designer.
The company started by only making assembly drawings, which are drawings that show how the final product should look when it is put together. Gradually, they started making drawings for every single part of the product, including the dimensions and tolerances. This way, any skilled machinist could make the product. The boss of the company returned to running the shop and was not involved in the design process as much.
In the past, molds had to be sent to the molder in order to be tested. However, now many mold makers have their own molding machines to test the molds. This is more efficient because the mold can be tested right away and adjustments can be made if necessary.
This is talking about how it can be expensive and time-consuming to keep sending a mold back and forth to be tested. It can be even more expensive if the mold needs to be tested multiple times. Having a machine to test the mold can actually save money in the long run, even though there is an initial cost for the machine. The mold designer needs to be involved in the testing process because they have the most experience and will be able to tell if the mold needs to be revised.
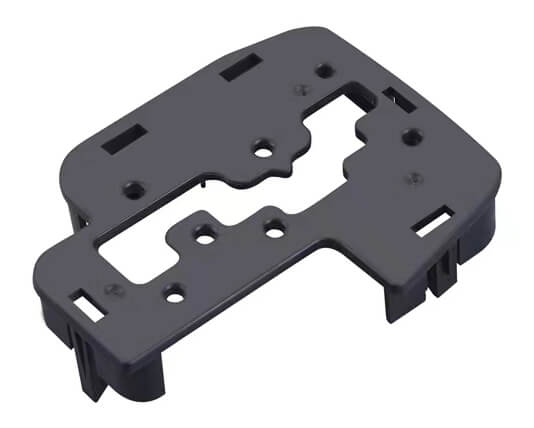
If there are any problems with the mold while it is being tested, the designer needs to be present so that they can be properly documented and fixed. A complete test report will help the molder when they are starting up the new mold.
Quite often, designers use the same methods or designs that have been used before without thinking about whether there is a better way to do it. This can be helpful because it saves time, but often the designers do not really understand why they did what they did. The method might have worked for one type of material but not for another, or it might have worked for a small production but not for a large one.
There are many different types of plastics that can be used for different things. Some plastics need to be made in a specific way to get the right shape, such as by injection molding or extruding. In most cases, a mold is needed to create the right shape for the product.
Molds for low-pressures processing are easier to build than molds for high pressures, such as injection molds. In the future, other plastics and other methods of processing and shaping them will be developed, but at the present time, injection molding seems to be the most common and economical method to produce plastic products, especially where large quantities are required.
https://www.plasticmoulds.net/history-of-mold-designer.html?feed_id=473&_unique_id=6303340dea244
Comments
Post a Comment