Here are six ways to save money on injection molding
Reducing expenses is a top priority for all businesses, regardless of size or industry. Limiting costs to low levels is the primary goal of any business owner to afford improvements and greater profits.
In the sector of plastics, it's like everything is determined by how profits are generated. However, many people underestimate the cost of molds made of plastic actually cost. But, there are ways to play the game that can be utilized to lower costs, especially regarding injection molding costs. Here are six strategies to reduce the cost of injection molding using plastic.
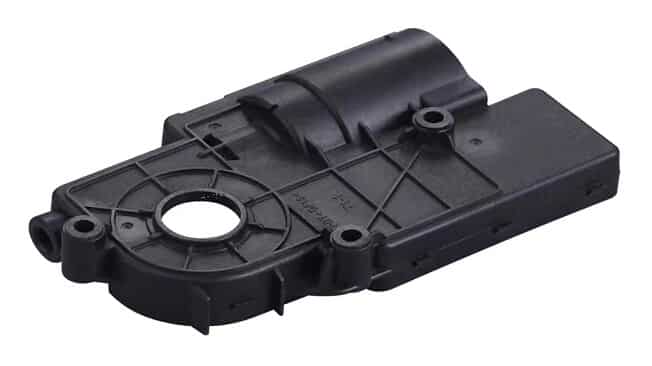
Beware of excessive use of cosmetics on the Features.
Refraining from using cosmetics and other features doesn't necessarily mean you're going to cut corners on the plastic design. Cosmetics are a great thing, but too many features will result in more costs and take more time for production. Keeping your plastic designs simple by focusing on the essentials is crucial to reducing costs for injection molding. Rims and hooks that are unnecessary are to be avoided as roundings that are not needed.
If you'd like an idea of a real-world illustration, consider the evolution of the chair made of plastic. It was constantly improved in shape and molding so that the current design can be produced with a couple of dollars. Find out more about this design here.
Make sure you stick to a lean design
Your plastic designs must be created using as few materials as possible. This design is best described as a minimalist design in the manufacturing industry. Naturally, using less material will result in lower costs, but this doesn't mean that the plastic product you are using will be unable to function as it should due to having fewer materials. The most efficient design is effective in terms of functionality and can help reduce the processing time to cool and mold. Imagine structural support as connectors and rather hollow shapes than huge ones. Companies that manufacture plastic injection molds typically assist with this.
The decision to incorporate an extra bit of your plastic design will result in additional mold work and an additional cost. Techniques like bead blasting, high-grade polish EDM, and so on could be required for your plastic model's desired cosmetics and features. If not, these methods can undoubtedly affect the aim to get a cost-effective injection molding.
The Design For Manufacturability (DFM)
DFM analysis provides possibilities to enhance your manufacturing process or the overall layout of plastic products. This includes the process of injection molding. The most valuable aspect of the DFM analysis is the ability to spot the issues present in your manufacturing system during its initial phases (from the production of plastic prototypes to the most recent), like imperfect shapes, inadequate angles, and wrongly calculated geometries. These can be used to reduce the costs of cosmetics and financial required for the project in the future.
Most of the time, the DFM analysis is done by an outside manufacturing expert who can provide input regarding how you can enhance your process and system and assist in developing the injection mold. Their expertise and knowledge can be helpful as a third party outside watching your business operations. The reduction in the cost of custom injection molding is sure to be covered by DFM analysis. Learn more about the various parameters here.
Innovative Mold Designs
The cost of injection molding is dependent on the various parts and components required to make a design in plastic. Also, the cost of molding each component plays a meaningful impact on the price of your product. To cut down on the costs of injection molding, it is crucial to develop creative and innovative ideas for the plastic you are making. Part positioning enhances the design to ensure that the mold will fit perfectly, and you will have fewer scraps left over from mold making.
Intelligent designs also eliminate the need for sprues and runners because of the placement of the correct parts. The ability to shed extra material, thanks to the design of your mold, results in a lower cost of injection molding. Another thing you can do is to ensure that all remains in good shape when ejecting and that there is no damage to the finished product or the mold design in any way.
Modification
It is not necessary to buy new molds for each batch of production you create. If you plan it well, you can reuse molds multiple times by altering them and inserting design tools that can change the mold's design and incorporate various features.
The most well-known method for mold modification is MUD Tooling process, which creates smaller molds from the base of the mold. The smaller mold is utilized for different purposes or to create other designs using plastic. Modification methods are well-known to aid in reducing custom plastic costs and are perfect for plastics manufacturers with multiple designs within their molds.
Family Mold/Multi-Cavity Mold
Making an affluent mold (also called a multi-cavity mold) is a great way to lower costs for injection molding. A family mold can incorporate multiple components inside the mold so long as the components are comparable in chemical composition and process tendencies. A family mold may be more costly than the standard mold; however, should you consider cuttings and separate tooling for each design in the mold, you can save a significant amount on the cost of injection molding.
A mold with multiple cavities mold is a good idea for companies that produce a lot of plastic. The family mold can produce plastic designs quicker because each cavity can produce an entire design of plastic in one run. It can be more expensive for tooling expenses but will eventually reduce injection molding per component cost. A family mold is the best way to reduce the cost of injection molding through mass production.
Final words
Injection molding is a standardized procedure that can be thought of as if there is no way to change the process due to its simple operation. But, as you dig into the depths of plastic manufacturing, you'll discover that there are many techniques to the process that can aid in reducing the costs of injection molding or take advantage of inexpensive plastic molds for higher-end manufacturing.
Following the six steps that were mentioned earlier on how to lower the cost of injection molding and increase your profits and earn more from spending less. There is no need to follow these suggestions because some might not work with your specific business model, but using just one or two of these strategies will make a difference to your company's finances.
https://www.plasticmoulds.net/here-are-six-ways-to-save-money-on-injection-molding.html?feed_id=330&_unique_id=62dcbb924c511
Comments
Post a Comment