automotive injection molding
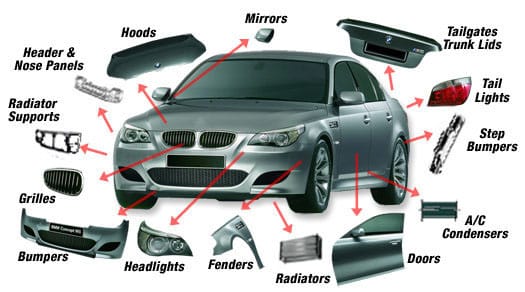
We offer automotive injection molding package that caters to both small and medium businesses for the entire plastics manufacturing process, making custom automotive plastics molding accessible to all. In our plastics injection molding automotive production Package, we allow you to mold plastic automotive injection molding or mix plastic with other materials such as metal, electronic, or paper. Components and assemblies are available on request.
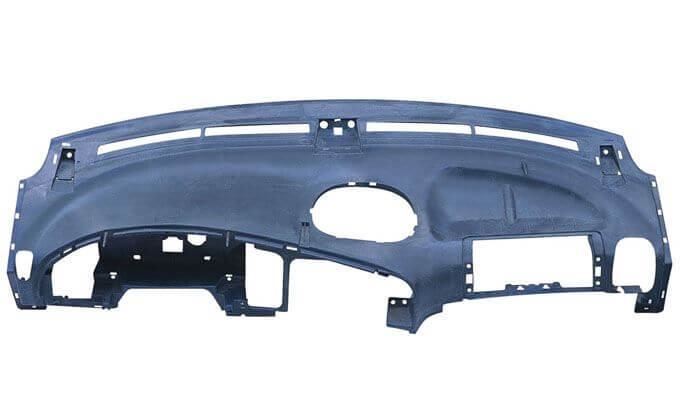
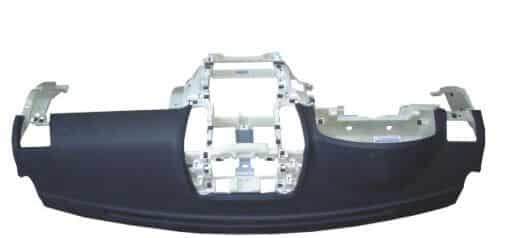
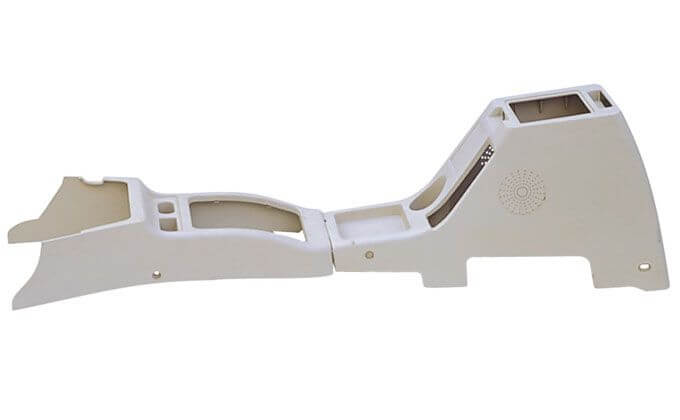
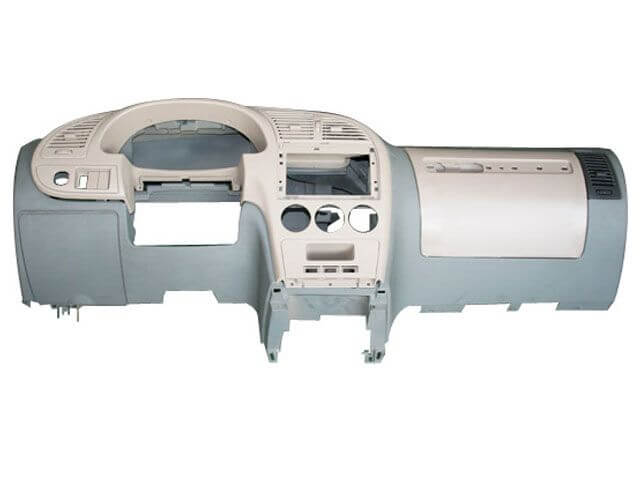
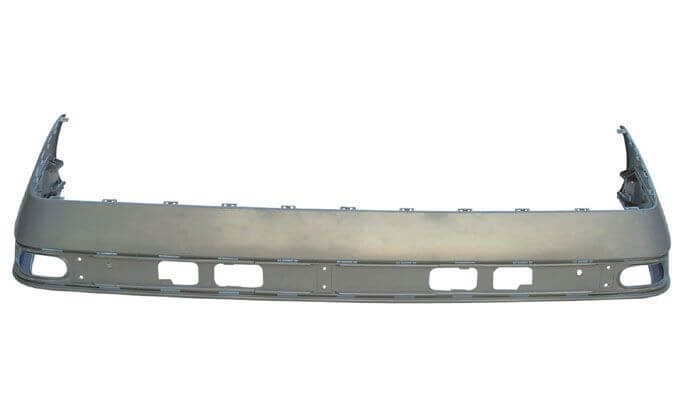
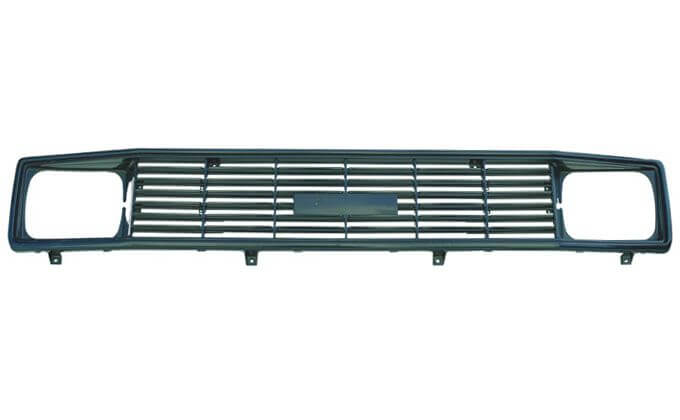
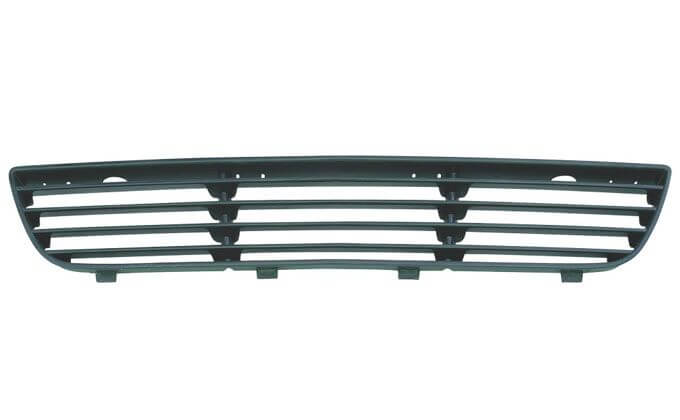
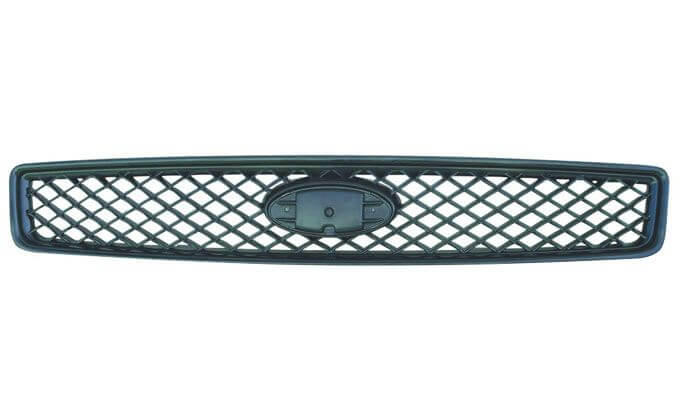
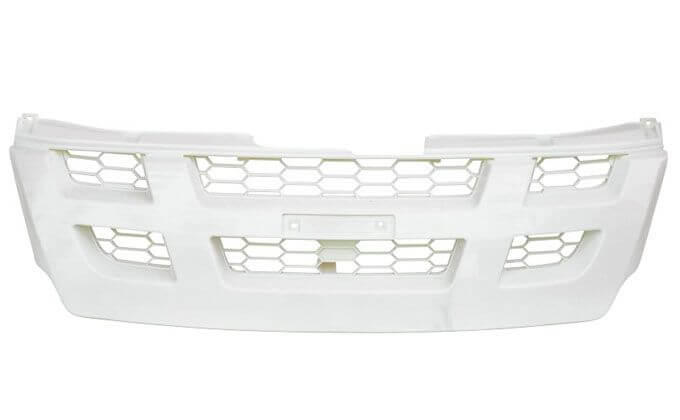
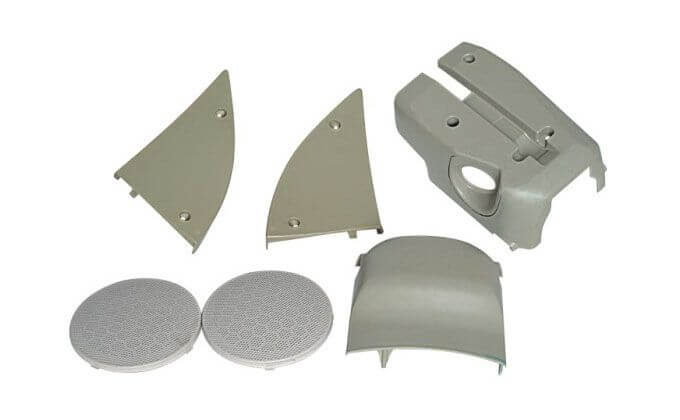
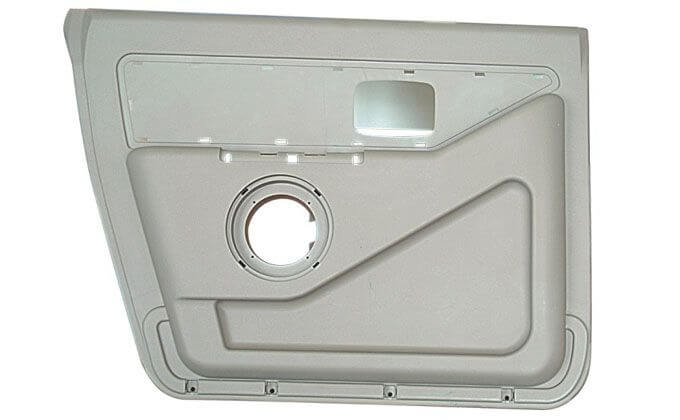
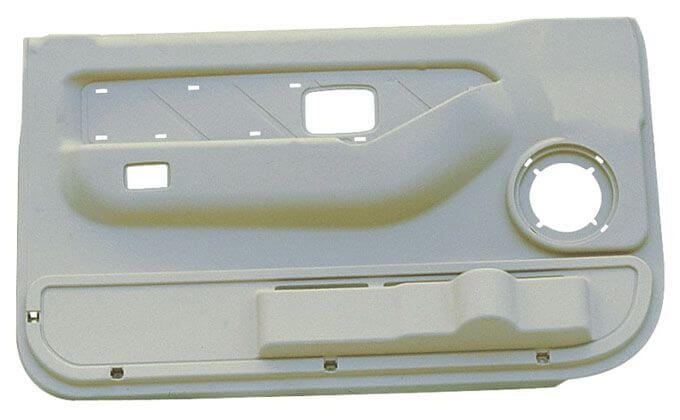
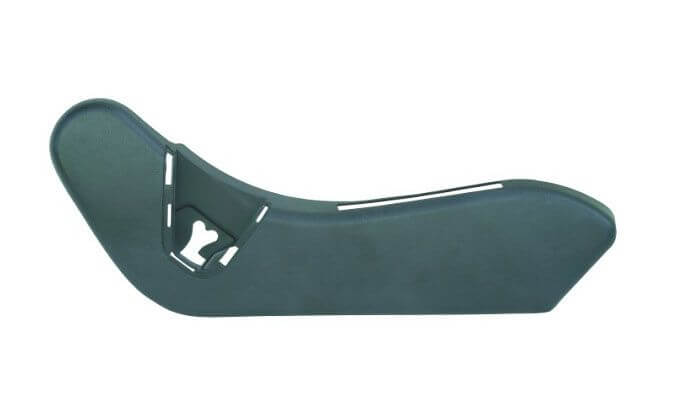
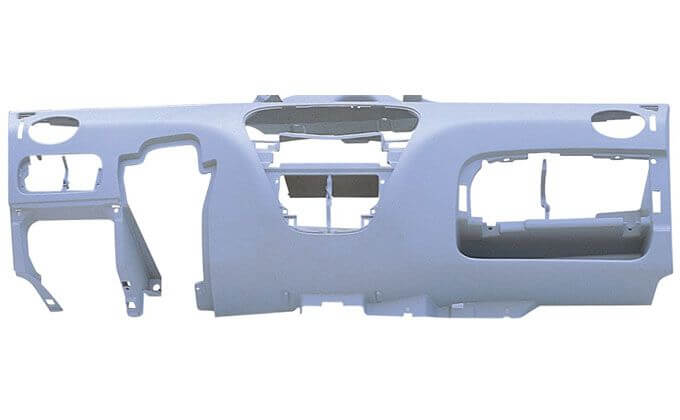
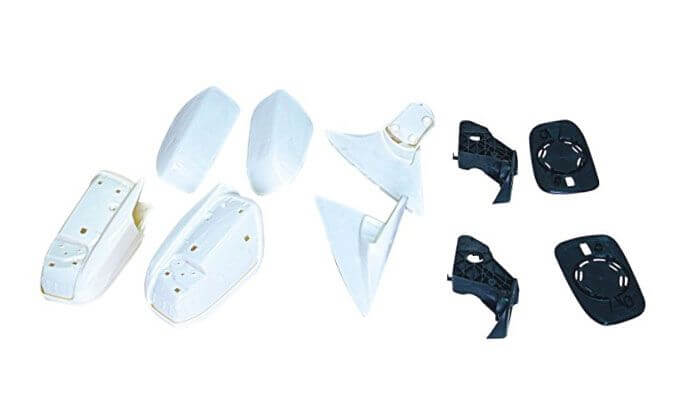
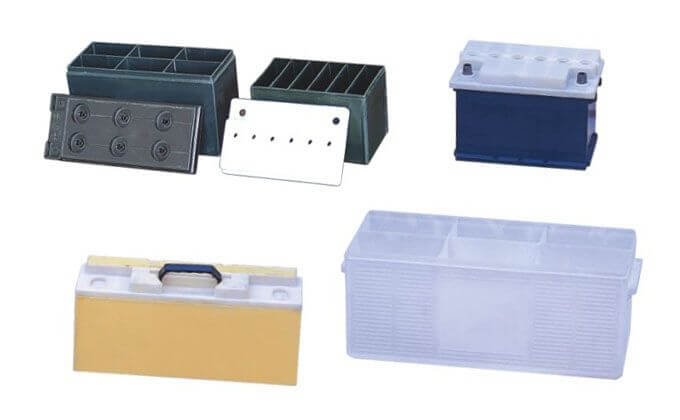
Automotive mold planning, automotive injection molding design, and mold creation are very significant aspects of Towpworks Plastic Manufacturer's productions. For some buyers, the cost of automotive injection molds can be very high even for simple designs. However, through our own tool shop, we reduce the development time and cost of automotive injection molding . In addition, we bundle individual mold orders to minimize costs. If you work with us, a plastics manufacturer with extensive experience, you do not need to start from scratch.
The automotive injection molding components don't only include elegant dashboards, seat floor mats, and other automobile plastic features that attract buyers. These options may offer an element of protection; however, hidden under-the-hood plastic auto components control a car's overall performance and safety.
More than 40 kinds of basic polymers and plastics are found in cars. It's not an issue considering that about 1/3 of the parts of a vehicle are plastic.
Despite many kinds of plastic material on market, however, approximately 70 percent of the material used in automotive plastic components is derived from four polymers that include polypropylene (PP) as well as polyurethane (PU) as well as polyamide (PA) polyvinyl chloride (PVC).1 Utilizing any one or all of them for automobile plastic design is best when done in partnership with an established injection molding supplier.
The knowledge of materials and industry insight of a skilled injection molder can be invaluable. They ensure that the car's plastic components and the vehicle systems on which they are installed comply with National Highway Traffic Safety Administration (NHTSA) standards.
Certified injection molders can select the most suitable polymers for use in cars based upon the performance requirements of manufacturing processes, as well as designs in the automotive part geometry to maximize the benefits of their products, for example:
SAFETY and Performance of CRASH
Even with the recent developments in automobile plastic componentry, safety is the most critical factor in selecting drivetrain and engine components. Polymers have to be proved efficient in limiting the impact of vehicles and crushing and passing a variety of other automotive test criteria. The plastics industry can keep up with technological advancements in automobile safety.
FUEL EFFICIENCY/LIGHTWEIGHT
In contrast to most metals, plastic is able to combine high-quality rigidity with the ability to be lightweight. The continuous advancement of polymers in automobiles permits OEMs to regularly replace heavy metal with light plastic elements, which offer superior performance, low specific gravity, and improved fuel efficiency. Automotive plastic components can also enhance the performance of onboard crash avoidance systems and performance systems.
WEAR AND WEAR Resistance
Some plastics can endure extreme weather conditions, including intense UV rays from the sun and rapid temperature fluctuations, and extreme wet and dry conditions -- many of which render metal a non-sensical alternative. Most plastic auto parts can take the rigors of wear and tear caused by rugged terrains.
PROPERTY RETENTION over the range of temperature for service
The best plastics will keep their integrity throughout temperatures ranging from 40 degrees to 200 degrees F without compromising on performance. This makes them ideal for applications that require under-the-hood protection.
COST-EFFECTIVENESS
Compared to metal, plastic component prices are usually less expensive because it is an injection molding process with faster cycle times. Additionally, color concentrates can add color to plastic parts before molding and removing the expense of painting. In addition, for assembly, one injection-molded piece eliminates the need for welded joints and fixers.
Additionally, OEMs are assuming more responsibility for sustainability by working with suppliers committed to zero- or low-waste initiatives and the use of recycled materials -- goals that are not achievable with metal. Injection molders are charged with refining processes to include recycling and scrap reduction to support the circular economy and effectively control costs.
Compatibility with mechanical FASTENERS
Plastics work well with connectors and metal fasteners in the automobile assembly. They also provide the ability to bear loads with elasticity as well as high tolerances and precise molding to fit into the tight areas within larger vehicles.
The dominance of plastics in the automotive industry is a testament to the characteristics of their protections, advantages, and properties they provide. Working with an expert injection molder to determine automotive plastic design possibilities and the appropriate plastics used in automobiles increases the benefits of plastics. It decreases the automotive sector's dependence upon metal.
https://www.plasticmoulds.net/automotive-injection-molding?feed_id=83&_unique_id=629ea28f73673
Comments
Post a Comment