ABS Injection Molding,China #1 ABS plastic part manufacturer,best price
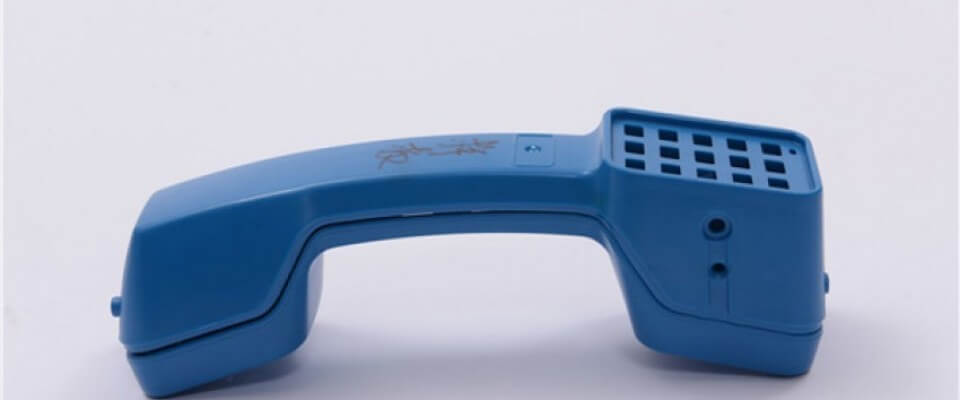
ABS Injection Molding
Are you in the market for an ABS injection molding manufacturer and designer that will improve the profitability of your business? Look no further than Topworks Plastic mold, a China injection molding company and providing full-service, custom ABS plastic injection molding.
We aim to be your partner. We are enabled to design, manufacture, and distribute the ABS injection molded products at prices that are internationally competitive and that meet the highest quality standards.
Because of this, we can take your ABS injection molding concept from paper to reality by offering a wide array of tooling, manufacturing, shipment services.
Our process will make your process simpler; whether your ABS injection molding product is still strictly a concept or is already a work-in-progress, or you are currently working with the copy of ready ABS injection molding parts, every stage of your product lifecycle will be streamlined for you.
Due to its good mechanical strength and comprehensive performance, ABS injection molding plays an important role in electronics, machinery, transportation, toy, and other industries, especially for a large box, decorative parts that need electroplating.
[ngg src="galleries" ids="8" display="basic_thumbnail"]-
ABS plastic injection molding design
The wall thickness of products requires uniformity.
The wall thickness difference of ABS plastic injection molding products should be controlled within 25% to prevent stress concentration.
To prevent the bosses from breaking, the root of the bosses needs to be R angle or reinforced ribs.
In snap joint design, the root of the snap joint needs a radius.
The size of the R depends on the wall thickness of the product. The ratio of the R angle to the wall thickness should be above 0.3.
As the ratio increases, the internal stress gradually decreases, but the sinks of the product on the surface should also be solved.
The design of the cooling channel of the mould should ensure the uniformity of cooling and avoid the internal stress caused by uneven cooling and contraction.
-
Drying
In general, heat-resistant ABS resin will absorb moisture in the air during storage and transportation.
The water absorption rate varies with the air humidity, generally between 0.2% and 0.4%.
The ABS material must be fully dried to reduce the water content of the material to below 0.05%, preferably below 0.02%; otherwise, surface defects such as spray and silver streaks may occur.
The drying temperature of heat-resistant ABS resin is higher than that of ordinary ABS, usually 80-95℃, and the drying time is 3-4 hours.
-
Temperature
The injection molding temperature is a parameter that should be noted during the processing.
The temperature must ensure the heat-resistant ABS is fully plasticized.
Increasing the molding temperature will obviously reduce the heat-resistant ABS's viscosity, increase the resin's fluidity, and make the flow distance longer to ensure that the cavity could be filled easily.
-
Holding pressure and time
For heat-resistant ABS, reasonable holding pressure and time directly affect the internal stress in the ABS plastic parts.
The holding pressure increasing will make the molecular gap smaller, the range of chain segment movement smaller, the volume smaller, the density larger, the force between molecules increased, which can decrease the shrinkage and improve the internal quality of the product, but it will lead to greater internal stress.
Therefore, ensuring the appearance quality of the product, it needs to try to choose a lower packing pressure.
The holding time is set according to the gate seal time with cooling.
The screw is pushed forward again, and no pressure is applied to the ABS molded product.
If the holding time is too long, the material will be easily filled too much, the molecular gap will become smaller, and the internal stress will become larger.
Whereas, if the holding time is too short, the product will shrink easily, and its size will be unstable.
The holding time should be set to the shortest time when the product weight does not change.
-
Mold temperature
It is suggested to use a temperature controller to keep the ABS mold temperature for heat-resistant ABS.
The recommended mold temperature is 60-80℃.
Higher mold temperature will often produce good flow, higher weld line strength, and less internal stress, but it will appropriately extend the molding cycle.
Whereas, if the mold temperature is lower than the recommended one, the internal stress of the product will be too high, which will lower the performance of the product and may lead to undesirable states such as crack, screw hole crack.
-
Feeding
When ABS plastic is injected into an injection molding machine, the injection quantity per shot is only 75% of the standard injection quantity.
To improve the quality and size stability of the parts, the surface gloss, and color uniformity, the injection quantity should be 50% of the nominal injection shot.
-
Solutions to Deformation of Large Plane ABS Injection Molding
If the ABS injection molded parts have a large plane, the shrinkage will be large.
Due to the extremely serious molecular orientation arrangement of large-scale ABS injection parts and uneven cooling of the mold, the shrinkage of the ABS injection parts in all directions is inconsistent, which makes the thin large-plane ABS injection parts prone to deformation and distortion.
Sometimes, one side of this injection-molded part is designed with ribs, and then the part will definitely bend towards the side with ribs.
It is indeed a problem to completely solve the deformation problem of large-plane ABS injection molded parts. The following are some effective measures to improve the deformation:
- Change the 1 gate to a multi-point gate (usually a three-plate mold), and it is better to reach more than 4 points with more than 24-ounce injection machines. In this way, different gates can reduce the degree of molecular alignment, and it can reduce the disparity of contraction in different directions.
- Properly increase the mold temperature, ABS material is usually kept above 60℃ to reduce the cooling rate of injection molded parts. It could reduce the deformation caused by the rapid cooling temperature difference and reduce molecular orientation.
- The most important thing is to increase the injection pressure and holding pressure and greatly extend the injection or holding time. And it will increase the size of the injection molded part, reduce its shrinkage; thus, the degree of deformation will be significantly improved. Therefore, extending the time for injecting or holding pressure (for example, extending 10 to 15 seconds) has become an important way to solve the deformation problem.
- If the above three measures fail, the last resort is to fix the shape immediately after demould.
First of all, the ABS injection molding parts should be ejected out of the mold early.
Then, they should be placed on the workbench and fixed with clamps while they are still in a high-temperature state (it should still be very hot, which is crucial).
The design of the fixture needs to be appropriate. At the same time, the degree of resilience of the ABS injection molded parts should also be considered; usually, the resilience will stop after 12 hours, and the lower the injection part temperature is, the larger the amount of resilience will be.
https://www.plasticmoulds.net/abs-injection-molding?feed_id=73&_unique_id=629ea21c639b6
Comments
Post a Comment