Why is Investing in Injection Molds So Costly?
Are you wondering why injection molds are so expensive? In this blog post, we’ll explore the reasons why investing in injection molds is costly, and how you can save on costs while still getting quality products. So if you’re curious about how to get the best value for your money when it comes to injection molding, read on!
Investing in injection molds can be costly, but it's important to understand why. The costs of injection molds are high due to the custom tooling and design that is required. Injection molds are a one-time investment, as they are designed to last through many production cycles. The upfront costs of injection molds include design and mold creation, assembly and shipping, and tooling.
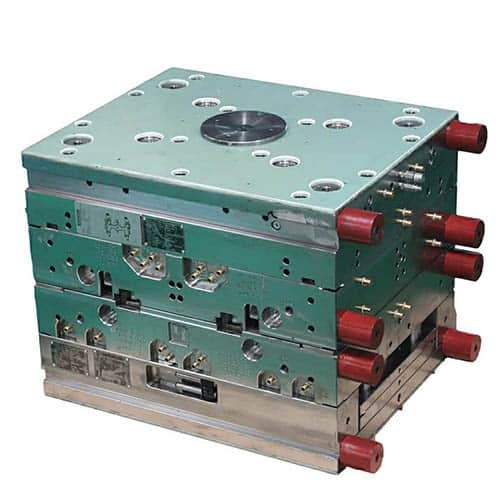
Thin wall injection molding is a specialized form of conventional injection molding that is used to produce thinner parts. Investing in injection molds is important to ensure quality production and a reliable supply of parts. Over-investing can be wasteful, but under-investing can result in a short mold lifespan and supplier reliability issues. Investing in injection molds is a worthwhile expense for companies that require well-made and reliable parts.
Definition of injection molds
An injection mold is a tool used in the manufacturing process of injection molding. It consists of a hollow cavity into which molten plastic is injected, and a runner system that channels the molten plastic from the injection nozzle to the cavity. Once the plastic solidifies inside the cavity, the injection mold is opened and the finished part is ejected.
Injection molds are typically made of hardened steel, aluminum, or other metals, and are precision-machined to produce parts with high dimensional accuracy and smooth surface finish. They can be used to produce a wide range of plastic parts, from small components to large automotive parts.
Injection molding is a popular manufacturing process because it allows for the mass production of parts with high precision and consistency, and it is suitable for producing complex shapes that would be difficult or expensive to manufacture using other methods.
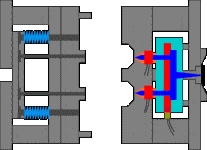
Overview of the costs associated with injection molds
The cost of injection molds can vary significantly depending on a number of factors, including the size and complexity of the mold, the material used to make the mold, the number of cavities in the mold, and the required finish and tolerances of the parts.
Some of the main factors that can affect the cost of injection molds include:
Material Costs
Injection molding is a popular method for manufacturing plastic parts, but the high upfront costs associated with creating the molds makes it an expensive choice. The primary reason for this cost is the complexity of the molds themselves. Injection molds are usually made from steel and require a high level of precision and accuracy. This means that they must be designed with intricate details and require specialized machinery in order to produce them.
The size of the part also plays a role in the cost of creating the molds. The larger the part, the more material is needed for the mold and the longer it will take to create. Additionally, the complexity of the part can also affect the cost. If a part is highly detailed or has a complex shape, then this will require more material and more time to produce.
Finally, once a mold has been created, it must be tested to make sure that it is able to produce parts in high volumes and with minimal defects. This testing process is also costly, as it requires additional machinery and personnel in order to properly test the molds.
Size and complexity of the mold:
The size and complexity of an injection mold can have a significant impact on its cost. Larger molds tend to be more expensive to manufacture because they require more material and more machining time. In addition, larger molds may also require more expensive equipment to produce, such as larger injection molding machines and handling equipment.
Complex molds with intricate shapes and features can also be more expensive to manufacture. Molds with deep cavities, thin walls, and other complex features may require more advanced machining processes and may take longer to produce. In addition, molds with complex shapes may be more difficult to design and manufacture, which can increase the overall cost of the mold.
Number of cavities:
Molds with multiple cavities can produce multiple parts per cycle, which can be more efficient and cost-effective than producing each part individually. However, molds with multiple cavities tend to be more expensive to manufacture.
The number of cavities in an injection mold can have an impact on its cost. Molds with multiple cavities can produce multiple parts per cycle, which can be more efficient and cost-effective than producing each part individually. However, molds with multiple cavities tend to be more expensive to manufacture because they require more complex machining and may take longer to produce.
In general, the more cavities a mold has, the more expensive it will be. This is because each additional cavity requires more material, machining time, and design work. However, the increased cost of the mold can often be offset by the increased efficiency of the injection molding process, as well as the improved quality and performance of the parts produced.
It is important to carefully consider the trade-offs between the number of cavities in the mold and the overall cost of the molding process. In some cases, it may be more cost-effective to use a mold with fewer cavities and produce each part individually, while in other cases it may be more cost-effective to use a mold with more cavities and produce multiple parts per cycle.
Tolerances and finish
The required tolerances and surface finish of the parts produced using an injection mold can affect the cost of the mold. More precise tolerances and higher surface finish requirements may require more expensive machining processes and materials, which can increase the overall cost of the mold.
For example, if the parts produced using the mold need to have very tight tolerances, the mold may need to be machined to a higher level of precision, which can be more expensive. Similarly, if the parts need to have a high-quality surface finish, the mold may need to be machined using more expensive materials or processes, such as polishing or electroplating.
In general, the more precise the tolerances and the higher the surface finish requirements of the parts, the more expensive the mold will be to manufacture. However, the cost of the mold can often be offset by the improved quality and performance of the parts produced.
Other factors that can impact the cost of injection molds include the lead time for manufacturing the mold, the desired lifespan of the mold, and any additional features or customizations that may be required.
So why injection mold is expensive?
Labor and Overhead Costs
Investing in injection molds can be costly, but the cost is often justified by the long-term benefits. The initial design and mold build are typically the most expensive upfront costs in injection molding. The mold material itself can cost hundreds of thousands of dollars, and the number of side-action components can also add to the total cost. Additionally, labor and overhead costs associated with injection molding can be significant, as there is a higher investment of time and labor involved due to the smaller and more intricate parts that are created.
However, the advantages of injection molding often outweigh the upfront costs. This process is cost-effective and efficient, allowing for high levels of automation that reduce labor and overhead costs substantially over time. Additionally, injection molding can be used to quickly produce large quantities of parts with consistent quality. These benefits make injection molding an attractive option for many manufacturing projects, despite the high initial investment required.
Long Lead Times for Production
Investing in injection molds can be incredibly costly, with lead times for production often adding to the total cost. Injection molding is the most popular manufacturing process for mass producing plastic products. It involves injecting molten plastic into a mold and allowing it to cool, creating a replica of the original product. This process is ideal for high-volume production, as the molds have a long life span and can be used repeatedly. However, the upfront costs associated with injection molding can be quite high, as the molds themselves need to be designed and produced first. This process can take weeks or months, and the cost of production molds can range from $5,000 to hundreds of thousands of dollars, depending on the complexity of the product.
The high cost of production molds is due to the long lead times for their development and manufacture. The molds need to be made with hardened steel for long-term use, which requires a great deal of time and effort. Additionally, the molds must be tested and adjusted before they can be used in a production run. All of this takes time, which increases the overall cost of injection molds. If you are considering investing in injection molds for your production needs, it is important to factor in the long lead times and high costs associated with them. While it may seem expensive at first, it will prove to be an invaluable investment in the long run.
The High Cost of Quality Assurance
Injection molding is a highly precise process that requires a significant investment in both equipment and personnel. Quality assurance is an essential part of the injection molding process to ensure that the molds produced are of the highest quality and will last for years to come. Investing in injection molds is an expensive endeavor, as the materials, machines, and personnel required to produce them come at a high cost.
The injection molds themselves are usually made from high-grade steel or aluminum, which can be costly depending on the size and complexity of the design. Additionally, the tooling used to create the molds must be of a high quality to ensure accuracy and durability. The injection molding machines used are also expensive, and need to be fitted with auxiliary equipment such as chillers, hoppers, and dryers to ensure a successful and efficient manufacturing process. Finally, there are labor costs associated with personnel needed to operate the machines and monitor the quality of the molds.
To maximize the lifespan of an injection mold, it is important to invest in quality assurance measures. This includes regular maintenance and inspection of the molds, as well as calibration of the machines. Close attention must also be paid to the raw materials used, as any impurities or inconsistencies can lead to flaws in the finished product. Investment in quality assurance measures can often pay for itself in the long run by preventing defects or breakdowns that would otherwise require costly repairs or replacements.
The High Cost of Design Changes
Investing in injection molds can be incredibly costly, particularly when it comes to design changes. The up-front costs of designing, testing and tooling a mold can be extremely high, making it difficult to spread the cost across many parts. Furthermore, the lead-time and costs of mold tool manufacturing are often challenging for businesses to manage. Moreover, the design freedom of injection molded parts is limited due to the complexity of the process.
If a design change is required, it can involve significant time and cost in re-designing, re-testing and re-tooling the mold. This can involve significant investments in personnel and equipment, as well as increased lead times for production. As such, it is critical for businesses to carefully consider the design of their injection molded parts to minimize the potential for costly changes down the line.
The Risk of Faulty Molds
Investing in injection molds is costly because of the risks associated with faulty molds. If a mold is not designed and crafted to the highest standards, it can cause major problems during the injection molding process. Poorly designed and constructed molds can result in inaccurate parts, wasted time and materials, and potentially dangerous situations.
The lead-time and costs of mold tool manufacturing are often challenging for low volume production, where the investment in tooling can be significant. To ensure a quality mold, well-designed tooling and higher precision build are essential. The more complex the part's geometry, the higher the costs of production. Metal Injection Molding (MIM) is inherently positioned to manufacture high-volume parts with its robust tooling, but MIM also requires a great deal of up-front investment.
Accuracy is very important when producing injection molds. Insufficient precision will directly affect the accuracy of mold clamping, which can lead to inaccurate parts and wasted materials. Single-cylinder injection is often used for low-volume production due to its simplicity, compactness, low capital cost and low residence time. However, this method is not as accurate as other methods and can lead to faulty molds.
In conclusion, investing in injection molds is costly due to the risks of faulty molds. Poorly designed and constructed molds can lead to inaccurate parts, wasted time and materials, and potentially dangerous situations. Accurate mold
Keeping Up With the Latest Technology
Investing in injection molds can be a costly endeavor. It requires high tooling costs and long set up times, and manufacturers must ensure that the injection molds they create are of the highest quality. The injection molds must be able to withstand the rigors of the injection molding process, which includes high temperatures and pressures, as well as repeated use over time. In addition, manufacturers must ensure that the injection molds are properly designed and tested to ensure that they are able to produce parts that meet the required specifications.
The tooling costs associated with injection molding can be very high, depending on the complexity and size of the product being produced. For example, if a manufacturer needs to create an injection mold for a complex product, such as a medical device, the tooling costs can be quite significant. The type of material used for the injection mold also affects the cost and complexity of the design.
The set up time for an injection mold is also quite long and requires a great deal of planning. It is important to ensure that the design is accurate and properly tested before it is implemented. Manufacturers must also ensure that the molds are properly maintained throughout their lifespan in order to ensure they continue producing parts that meet the required specifications.
Overall, investing in injection molds is a costly endeavor that requires manufacturers to invest in high-quality tools and materials and spend time on design and testing. However, manufacturers must do so in order to keep
Maintenance and Repair Costs
Investing in injection molds is a costly endeavor but one that is necessary for many manufacturing processes. The upfront cost of designing and creating a mold can be hundreds of thousands of dollars, and the cost of assembly and shipping can grow linearly. Additionally, the mirror-polished surfaces of plastic injection molds are very sensitive and require more surface cleaning, protection, and maintenance. This is why it is important to invest in an injection mold that is designed to last for years.
On one hand, injection molding is often the most cost-effective way to get plastic parts made. However, it requires an upfront investment and requires project management expertise to make sure that the process is efficient and cost-effective. Additionally, more complex molds such as unscrewing mechanisms can be more expensive as they are considered long-term investments. To ensure that the molds last and remain cost-effective, it is essential to document maintenance, revisions, and repairs regularly.
In conclusion, investing in injection molds can be costly due to the upfront cost of design and creation as well as the need for ongoing maintenance and repairs. However, the cost is worth it in the long run as injection molding can provide a cost-effective way to get plastic parts made quickly and efficiently. It is important to invest in an injection mold that is designed to last for years and to regularly document maintenance, revisions, and repairs to ensure that the molds remain cost-effective.
https://www.plasticmoulds.net/why-is-investing-in-injection-molds-so-costly.html?feed_id=1054&_unique_id=639d240a52d8b
Comments
Post a Comment