what is plastic mold?
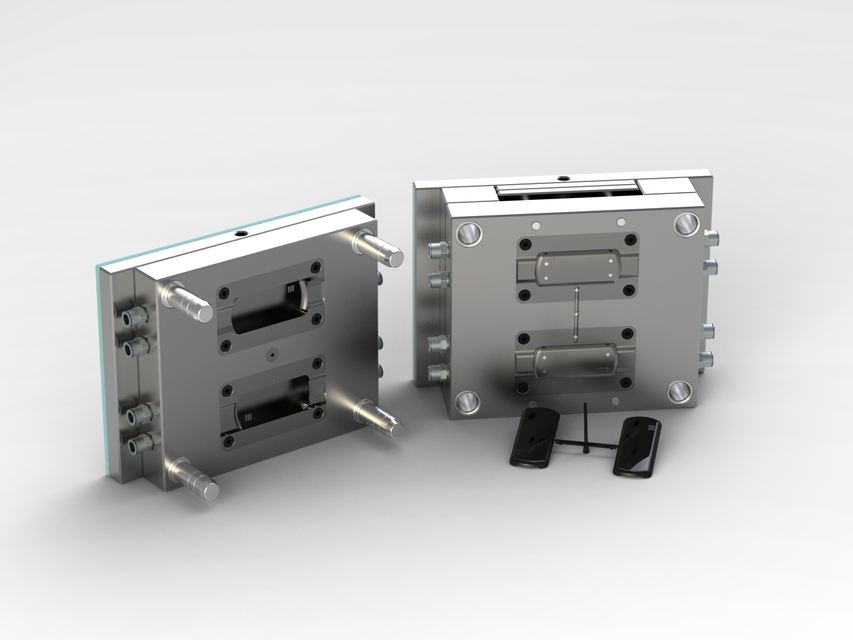
What Is Plastic Mold?
The tooling used for plastic injection molding is called a plastic mold or plastic injection mold. The plastic mold is made from a combination of steel plates and other mold components, coupled to form an overall mold, which is then reliably assembled and installed in an injection molding machine, then applies a thermoplastic resin to the desired shape to fulfill the intended purpose.
Most plastic products are molded by plastic molds.According to the molding plastic characteristics, plastic molds are divided into thermosetting and thermoplastic mold.
By its very nature, an injection mold must satisfy a multitude of demands simultaneously when the molding process is being conducted. To form a plastic component having the shape of the mold cavity, the mold must contain the polymer melt inside the mold cavity. Heat is transferred from the hot polymer melt to the cooler mold steel, in order to give injection molded products as uniform and cheaply as possible. Lastly, the mold produces a fairly repeatable ejection of the part, which makes subsequent moldings more efficient.
The injection mold is expected to perform these three functions – contain melt, transfer heat, and expel molded parts – as well as additional requirements. Taking the example of containing polymer melt within a mold, it is imperative to have the mold resist enormous forces that may deflect or open the mold, and it must contain a feed system that directs the polymer melt from the molding machine to one or more cavity in the mold.
Additionally, these secondary functions can give rise to tertiary functions when specific mold components or features are used to accomplish them. Injection molds perform a number of functions, but they should be considered only a sample of the necessary primary and secondary functions during the design phase. Even so, a skilled designer would recognize when different functions are putting conflicting requirements on the mold design. Multiple cooling lines that are tightly spaced can provide efficient cooling by conforming to the cavity of the mold.
When it comes to removing parts, ejector pins may be required at locations where cooling lines are not desired. Designing a mold in a way that satisfies the conflicting requirements is the responsibility of the mold designer. When in doubt, novice designers tend to overdesign. The tendency to do so often leads to large, inefficient, and costly molds.
The structure of an injection mold
- The mold base, which provides a secure and accurate foundation for the mold.
- The mold cavity, which is the part of the mold that defines the shape and size of the molded part.
- The core, which is used to create the internal features of the molded part, such as holes or threads.
- The sprue and runners, which provide a channel for the molten material to flow into the mold cavity.
- The gates, which control the flow of material into the mold cavity.
- The cooling system, which is used to remove heat from the mold and the molded part, and to help the material solidify in the desired shape.
- The ejector pins, which are used to push the molded parts out of the mold cavity once they have cooled and solidified.
The structure of an injection mold can vary depending on the specific application and design requirements. In general, however, an injection mold consists of the following main components:
In addition to these main components, an injection mold may also have other features, such as slides and lifters, to create complex movements and shapes in the molded part.
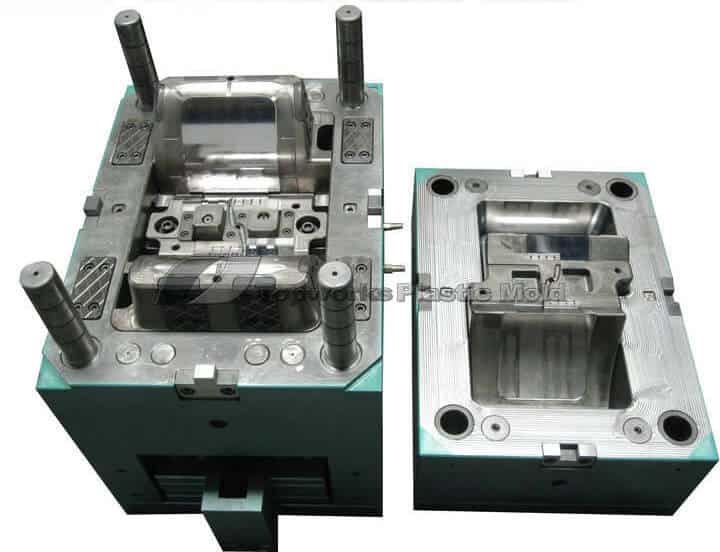
Based on the molding process, the plastic mold is divided into
- injection mold,
- blow mold,
- casting mold,
- pressing mold, and so on.
The injection mold comprises two main sections: the moving half and the fixed half.
The moving half is mounted on the moving platen of the injection molding equipment, and the stationary half is mounted on the stationary platen.
Over the injection molding, the moving and the stationary half are shut to develop an injection structure and a cavity structure.
Once the mold is open, the moving half and the stationary half are split up to clear away the plastic item from the plastic mold.
To decrease the mold design and developing period, the majority of the plastic molds work with standard mold bases.
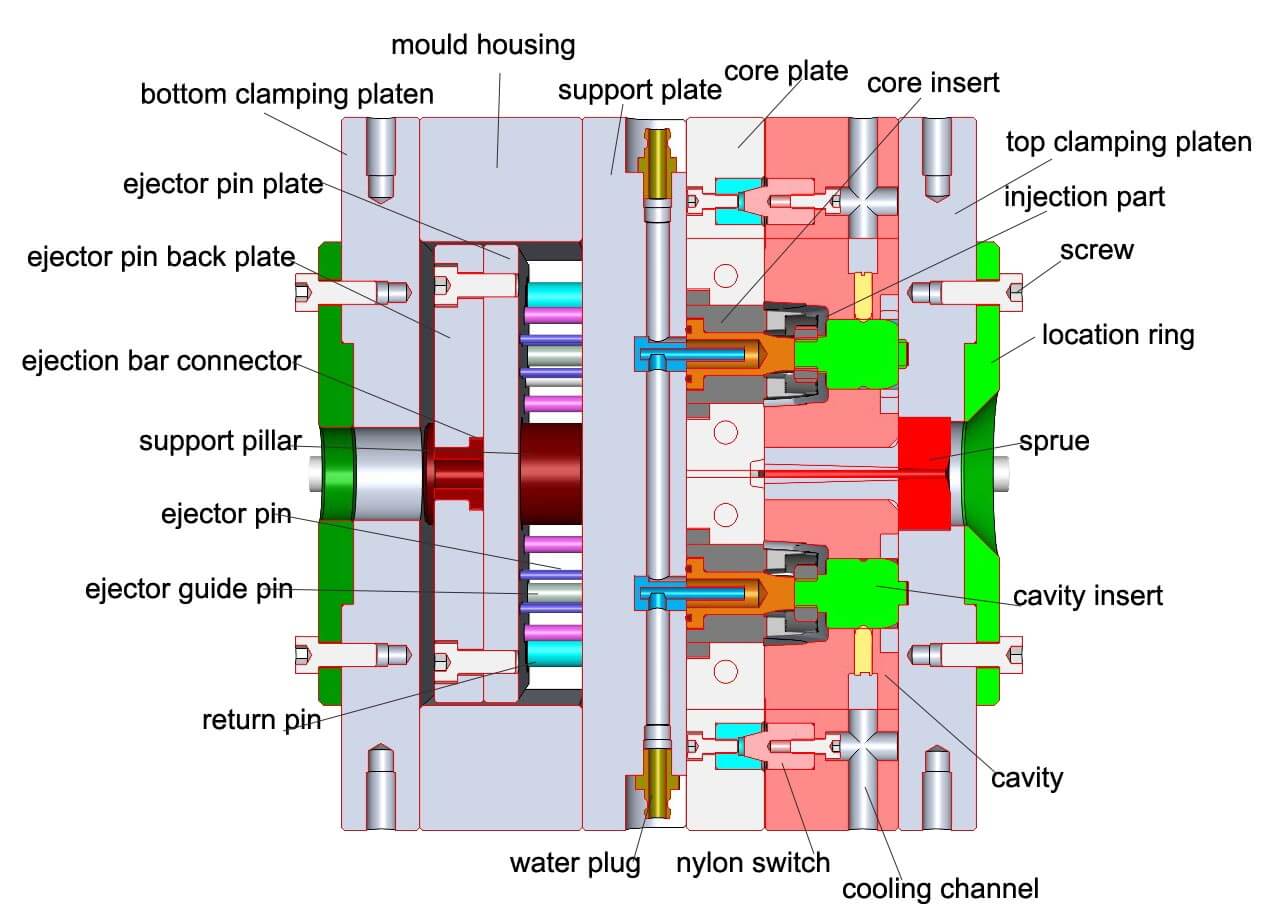
The injection system and the part forming system are in direct contact with the plastic, and they change with the different plastics and products.Those 2 systems are the most complex and most varied parts in the mold and require the highest finish and accuracy.
The part-forming process refers to the melted plastic heated by an injection molding machine is injected into the mold cavity.After cooling and solidification, it gets the molded products. Which simplifies as mold close - injection - pressure - cooling - mold open - ejection.
The plastic injection mold is generally composed of the following parts:
- mold base: generally choose standard mold base from standard mold base manufacturing factories, such as LKM, DME, HUSCO...
- the mold insert: it is used to form plastic products; a plastic mold factory normally makes it by itself; most of the processing time is spent on producing mold inserts.
- Mold auxiliary parts: they include location ring, nozzle bushing, support pillar, ejector plate, guide bushing, guide pin, lifting ring, and so on.
- The four major systems:
- Injection system(runner): Injection system refers to the flow path part before the melted plastic enters the cavity from the nozzle, including the main runner, the cold slug, the sub-runner, and the gate. It is directly related to the molding part quality and production efficiency.
- ejection system: ejector pins, blade pins, and sleeves.
- heating and cooling system: hot runner, preheating device, cooling water;
- venting system: venting slot, parting surface venting, ejector pin venting, and insert venting;
- special mechanism: if the product has the undercut or sidewall hole, the plastic mold needs to design the side core pulling mechanism (also called the slide), the inclined core pulling mechanism (also called the lifters), the oil cylinder (when the side core pulling distance is long).
Classification of injection mold:
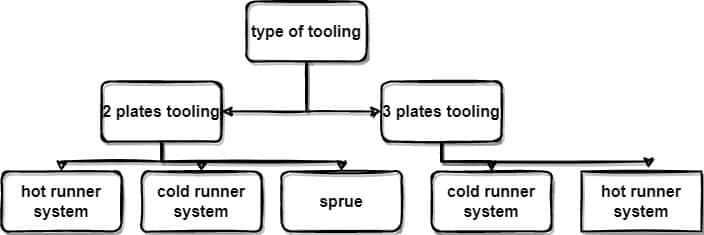
- 2 plates mold: another name of the sprue gate mold, also known as the single parting line type plastic injection mold, its characteristic is the simple mold structure, but the sprue is a part of the injection molded part, and it needs to be manually removed later, and plates mold structure is widely used for various kinds of mold.
- 3 plates mold: the pinpoint gate mold and the double parting line type injection mold. Its gate characteristic is pinpoint, and the gate cross-section is small. The injection molded part appearance is good, and because it does not need the manual removal of the gate later, it is advantageous for the automation production. But three plates mold structure is more complex, and the cost is higher. It is generally applicable to small and medium plastic parts. And plastic molding material is with good fluidity.
Difference:
The most significant difference between the three plate mold and the two plate mold is that the three plate die has an extra runner plate (automatic remove runner).
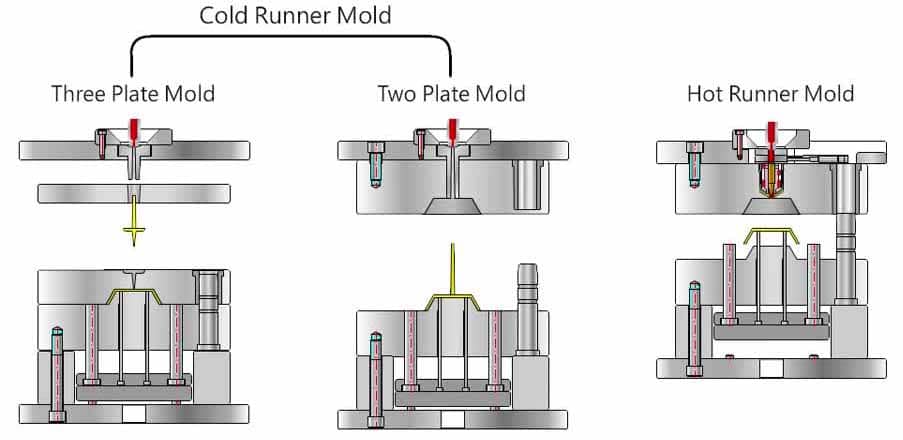
The main plastic mold system
There are four key concepts to consider when designing a mold, and the next few lines provide information on how to design a mold.
1.Runner
To design a good runner, its geometry, size, and layout also should be correct, in addition to its cooling ability, ejectability, and minimization of regrinds. It is best to fill all cavities at once using a balanced runner system to minimize cycle time and ensure the greatest possible dimensional integrity of the molded product.
The long and thin runners or any runner shaped like a half-moon or a half-circle need to be filled at higher pressures to prevent the mold from cooling down prematurely and causing incomplete parts. The length of a long and thick runner leads to an increase in regrinding, which, in turn, reduces the efficiency of the molding process.
In cases where the runners' intersections should have ejector pins positioned to eject with sufficient force, ejecting the runner should still be possible. On the ejector portion of the mold, it is preferable to have runners installed to be forced out with the ejector.
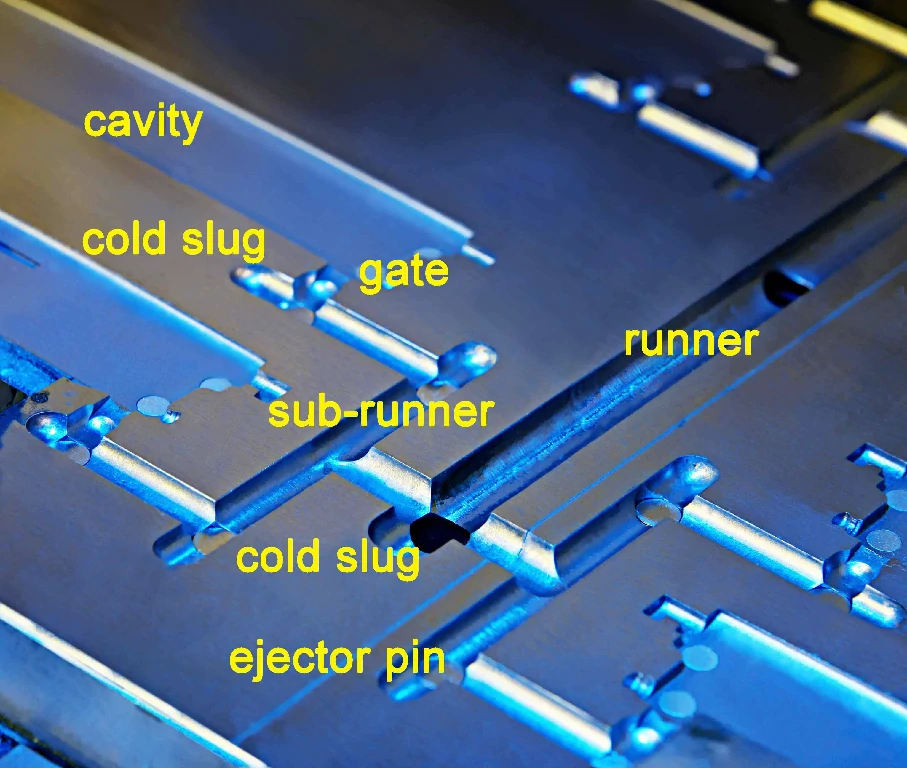
Main Runner
This is a portion of the mold that attaches the nozzle of the injection molding press to the sprue. The top of the sprue is concave for touching with the nozzle.
The one end diameter of the sprue needs to be a little bigger than the nozzle size (0.8 mm) to prevent excessive streaming and avoid the two from being clogged due to wrong positioning.
The size of the one end is determined by the item's dimensions, generally 4-8 millimeters. The size of the runner ought to be increased inwards at an angle of 3° to 5° to aid the ejection of runners.
In addition to the correct runner geometry, size, and layout, good runners must also be cool quickly, ejectable, and have very little regrind. For filling all cavities simultaneously, a balanced runner system is necessary, which minimizes cycle time and allows the molded product to remain dimensionally intact.
Long and thin runners or half-moon runners require higher injection pressures to ensure that parts aren't rendered incomplete if the mold cools too quickly. Long and thick runners result in more regrind, which decreases the effectiveness of the operation. Ejector pins should be in place to expel the runners at the convergence of the cold runners.
Runners should be installed at the core half of the mold so that the ejector should be able to push these out of the mold.
Sub-runner
This is basically a small channel joining the primary runner and each cavity for the multi-cavity plastic mold building. As a way to come up with the melted resin occupies the cavity in equivalent velocity, the layout of the runners for the mold needs to be symmetrical and equidistantly spread.
The form and dimension of the runner impact the stream of the plastic melt, the discharge of the item, and the mold building. In many cases, the trapezoidal or semi-circular cross-sections are employed for runner design, and they are machined on ejection half of the mold for the ejector pin to push out.
The exterior of the runner has to be finished to minimize the stream resistance to produce a quicker filling speed. The dimensions of the runner vary according to the sort of plastic material, the dimensions, and the thickness of the item.
For most thermoplastics, the runner's cross-sectional circumference is not over 8 millimeters, Maximum 10-12 millimeters, Minimum 2-3 millimeters. The cross-sectional region needs to be created as small as possible to decrease the resin misuse and shorten the cooling period.
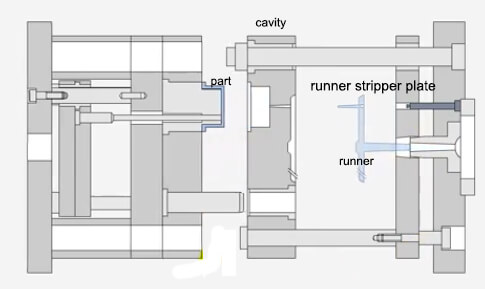
Cold Slug
It is deemed a prolonged runner situated at the far tip of the main runner to capture the cold resin among the 2 cycles, therefore avoiding the possible blocking of the main runner or the gate.
Should the cold resin blend directly into the cavity, the interior stress will probably stem from the injection-molded item.
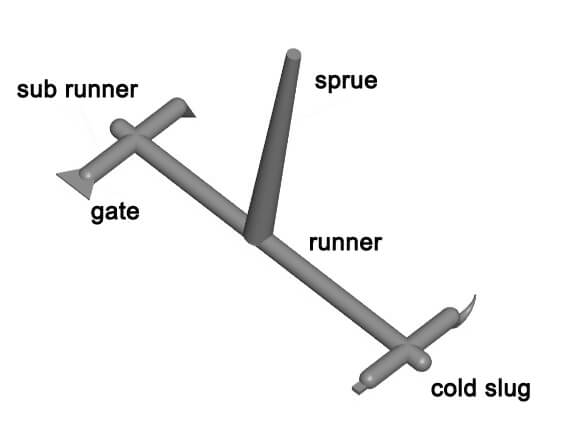
The Cold slug features a diameter around 8.5-10.5 mm and 6.5 mm deep. To be able to help ejection, the base is usually grabbed by a puller. The tip of the puller needs to be created to be a zig-zag catch or a depressed slot to ensure that the cold slug might be easily removed in the course of ejection.
2.Temperature Control for cooling
As the injection mold is filled with plastic, it needs to be cooled so that the plastic can solidify and retain its shape. There are various ways to cool an injection mold, and the most effective way depends on the size and shape of the mold.
To meet up the mold temperature demands of the injection molding procedure, a temperature control technology is necessary to regulate the heat level of the mold.
For injection molds to inject thermoplastics, the cooling system is usually built to cool the mold. The most popular way of mold cooling would be to drill cooling water lines inside the mold and work with moving cool liquid to take out the mold's heat.
Along with heating the mold, hot liquid or vapor should be considered within the water lines, and a heating bar might be mounted within and around the mold.
Mold cooling is an essential metric for determining the quality of the product given to the customer in terms of dimensional integrity, physical properties, surface finish, shrinkage, and the strength of weld lines.
Irregular cooling inside a long cavity will result in poor warpage control. Cooling all core pins is imperative, especially if the ratio of length to the diameter of the core exceeds four. Hot core pins result in surface imperfections and prolong the molding process.
The heat transfer efficiency of a water layer on the pins is much higher than that of the air layer. Ejector pins for flexible resins need cooling before ejection.
The ability to control the temperature of the sprue puller pin area reduces the time it takes to cycle the mold and the number of interruptions it causes during the ejection process.
For effective temperature control, the fluid flow must be high-volume and turbulent.
Prohibiting corrosion within the water lines is achieved by using stainless steel mold plates; other ways to prevent corrosion include plating the cooling channel or adding rust inhibitors into the water. The mold plates must be thick enough to accommodate the cooling channels of proper size.
some facts:
Injection mold cooling systems need to take the location of the cooling lines into account when designing them. Ideally, 12-18mm should be left between the filling and the coolant in the cavity. Coolant lines centers should be approximately 5D apart.
Moreover, cooling lines should not be placed near where the melt flows finally meet, as this can impede plastic flow.
Another factor to consider is the length of the coolant channels. The longer the coolant channel, the more difficult it is to process and the worse the cooling effect. The number of cooling line elbows should not exceed five. The distance between hoses should also not be less than 30mm.
mold width vs diameter of cooling channel
Mold width | Diameter of cooling channel |
width < 200mm | 5-6 mm (or 3/16″-1/4″) |
200mm6-8mm (or 1/4″ – 5/16″) | |
400mm8-10mm (or 5/16″-3/8″) | |
500mm10-13mm (or 3/8″-1/2″) | |
Another factor to consider when designing an injection mold cooling system is the type of cooling used for the mold core. The core insert is the part of the mold that contains the cavities in which the plastic is injected.
- For cores insert with a diameter less than 10mm, natural cooling can be used. This means that no special cooling lines are needed and the heat can dissipate through convection.
- For cores insert with a diameter between 10 and 15mm, inlaid cooling can be used. This means that the core is cooled from the inside by channels that are machined into the core itself.
- For cores insert with a diameter between 15 and 25mm, a jet cooling system can be used. This system uses nozzles to spray coolant directly onto the mold core.
- For cores insert with a diameter between 25 and 40mm, a cooling bladder + spacer system can be used. This system uses a bladder filled with coolant that is placed around the mold core, and spacers are used to keep the bladder in place.
- For injection molds with a large core insert diameter (greater than 40mm) and a small height (less than 40mm), it is inconvenient to guide the coolant through the injection mold. In this case, it is better to use a cooling plate system. This system uses a cooling plate that is placed on top of the mold core. The coolant is then pumped through channels in the plate and flows around the mold core.
The final factor to consider when designing an injection mold cooling system is the type of coolant used. The most common type of coolant is water, but other options include oil, air, and CO2.
- Water is the most effective type of coolant, but it can cause corrosion if it is not properly filtered.
- Oil is less effective than water but does not cause corrosion.
- Air is the least effective type of coolant but is also the safest, as there is no risk of corrosion.
- CO2 is a very effective type of coolant but is also the most expensive.
When designing an injection mold cooling system, it is important to take into account all of these factors in order to create a system that is both effective and efficient.
3.Venting
This is a not deep groove cut in the mold to release the air within the cavity or the soft plastic material introduced.
Should the melted resin is shot into the cavity, this kind of trapped air in the cavity needs to be released out of the mold via the grooves at the end of the streaming front in time.
Or else, the item will likely have voids inside(especially for transparent resin injection molding), vulnerable weld lines, um-completed shot -. Perhaps the build-up of air would produce excessive-high temperatures because of the high pressure to make the item charred.
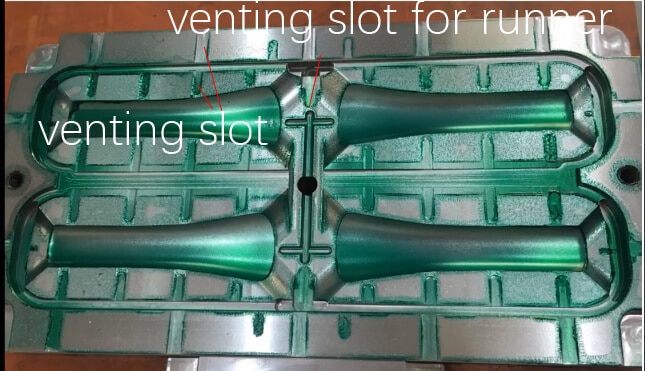
The venting grooves might be situated both at the end of the melt stream and on the P/L of the mold. The last-mentioned place is a shallow slot that is a depth of 0.03-0.2mm and a width of 2-6.5mm cut on the cavity side of the plastic mold.
The vent grooves won't escape much-smelted resin throughout the shot since the melted resin will cool down around this location and congeal the grooves. The placement of the vent grooves ought not to be confronting the operator to avoid an unexpected splash shot of melted resin. The gap between the ejector pins and the ejector hole, between the ejector bar stripper plate and the core insert, may be a method to release the air.
plastic mold venting slots size:
[table id=4 /]4.Ejection
Ejector pins, sleeves, stripper rings, or stripper plates should work without obstruction to realize consistent ejection.
A guided ejector system allows for precision alignment of the core and pins and will also bear the loads so that the pins do not wear out and go out of alignment. An early return system is another safety feature that should be included.
The early Return system drives all ejector pins into seated positions before the mold closes, ensuring no accidental contact with the ejector that has not fully retracted. Every mold incorporating ejector pins or sleeves under any slides should have a protector pin.
To prevent the ejection pins from colliding with the slides, this lock secures it in the retracted position. Plastic mold should use special ejection systems for parts that consist of flexible, thin-walled, deep sections that are difficult to eject.
How to choose plastic mold steel:
[table id=9 /]Mold Development Process
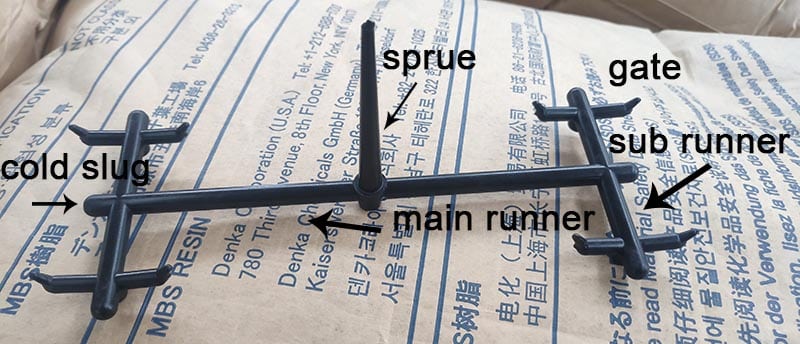
The figure above illustrates and describes an iterative mold development process as is commonly used in mold design, since there are considerably higher levels of interaction between the product design, mold design, and injection molding process.
In order to reduce the time required to develop a product, it is common for the product design and the mold design to be done at the same time. It is true that a product designer can easily estimate the cost of a preliminary part design just by considering the dimensions, thickness, and material of the final part.
In the instance that a mold design could be developed based on this information, a preliminary mold design would be created, and a preliminary quotation would be provided.
Molders will need to design a rough mold for the purpose of doing this preliminary quote. In addition to designing the rough mold, molders will need to estimate critical processing variables such as clamp tonnage, machine hourly rate, and cycle times.
Once the quote has been accepted, the engineering design can begin.
First and foremost, the mold designer will consider many factors before mapping out the design of the mold, such as the type of mold, the number of cavities and their positions, as well as its size and thickness.
Once that is done, each of the subsystems of the mold needs to be designed, which turns out to sometimes mean redesigning subsystems that have already been designed.
In some cases, the cooling system might have to be redesigned, depending on where the ejector(s) are placed.
When the mold design is fully developed, the mold base and other materials can be customized and ordered at the same time to reduce the development time.
The concurrent engineering approach should not be used to design fuzzy aspects of the product. In fact, many mold manufacturers order the mold base and plates upon confirmation of order, so that it arrives in the right time and place.
The lead times typically associated with mold development are now measured in weeks instead of months due to these concurrent engineering practices.
For generations, mold-makers have been creating molds at a faster pace to satisfy the needs of their customers, who have traditionally paid more for faster services.
In the midst of increasing competition, customers are becoming more and more insistent on guarantees regarding mold quality and delivery times, with penalties being applied to missed delivery dates or poor quality levels.
To verify the basic functionality of a mold, molding trials are conducted after the mold has been designed, machined, polished, and assembled.
The moldings will be sampled if no noticeable deficiencies are present, and their quality will be evaluated in relation to specifications. When the mold and molding process are good, they can produce a good product, but they need to be tweaked to increase its quality and to reduce the cost of the product.
There are, however, some instances in which molds contain "fatal flaws" which are not easily repaired and may have to be scrapped and a totally new mold designed.
Elements of a Plastic Mold
Designers and people interested in creating a mold should realize that molds are basically made up of a number of different elements from which to choose a design that is appropriate for use.The following elements are essential to every injection mold:
1. Determination of the cavity space(s) with corresponding cores ( molds can have up to 144 cavities for preform mold).
2. A conduit for conveying (hot) plastics from the machine nozzle to the mold cavity.You can choose from
- Cold runners (two or three plate)
- Hot runners (of various types)
3. Ventilation:Natural venting or vacuum venting are both options.
4 A cooling system designed to allow the molded product to be ejected from the cavity
5. Various options are provided for ejecting the molded article:These include
- Hand removal
- Sleeves and pins for ejectors
- Stripper
- Ejection by air
- Force ejection
- Various methods of in-mold product removal methods
- Automated removal methods
6. Attaching the mold to the machine:Several methods are available
- Molds are limited to one machine
- Mold can be used on more than one machine
- Easy mold change options
7. Aligning the cavities and cores:The following methods may be used:
- No alignment feature
- Brass bushings and pins (2, 3, or 4)
- Leader pins and bushings between ejector pin plates
- Taper locker between individual cavities and cores
8. A number of (mold) plates would be required here to support and back the above elements.
Although each of these features can increase the cost of a mold (often quite significantly), they can also improve the productivity of a mold and lower the cost of a product.
If you are looking to choose the most suitable (and most economical) mold for a particular application, these factors may not all be necessary.
Plastic Mold Gates:
The gate of plastic mold refers to a short flow path between the runner and the cavity, which is the entrance of the resin into the cavity.
It is a channel connecting the runner and the cavity.
The cross-sectional area of the gate can be equal to the runner, but it is usually reduced. So it is the smallest part of the entire runner system. The design of the gate is related to the size, shape, mold structure, injection conditions, and properties of the plastic parts.
The role of the gate :
- It could control the flow rate:
- The early solidification of the melt in this part can prevent backward flow:
- The molten material passing through is subjected to strong shearing to increase the temperature; thereby, it will lower the viscosity to increase the fluidity:
- It could facilitate the separation of products and the runner system.
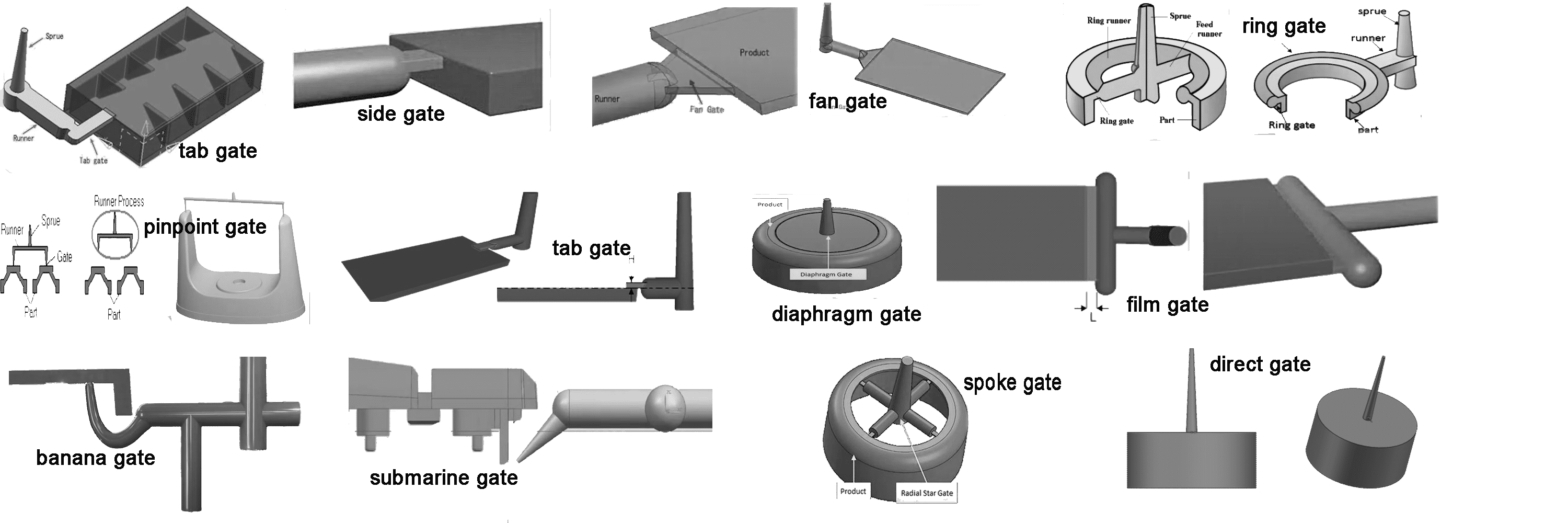
The design of the gate shape, size, and location depend on the plastic, the size, and the structure of the article.The shape of the cross-section of the gate is rectangular or circular, and the cross-sectional area should be small, and the length should be short.
Gate location should generally be selected where the product is thickest without affecting the appearance. The shape, quantity, size, and location of the gate will greatly influence the quality of the plastic parts. So gate selection is one of the key points in plastic mold design.
Direct Gate
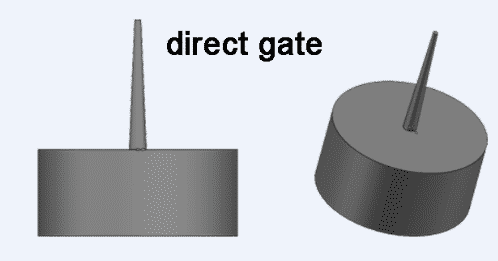
- Pros:
1) low-pressure loss;
2) the processing is simple.
- Cons:
1) the stress near the gate is large, and the product stress is uneven and easy to deform.
2) it is necessary to remove the gate with extra works manually. Also, it will leave obvious gate marks on the product surface.
Application:
1) it is suitable for large and deep barrel-shaped parts. For plain parts, it is prone to warpage due to shrinkage and stress.
2) for parts that are not allowed to have gate marks on the surface, the gate can be set into the inner surface of the part, which is an inverted mold.
side gate
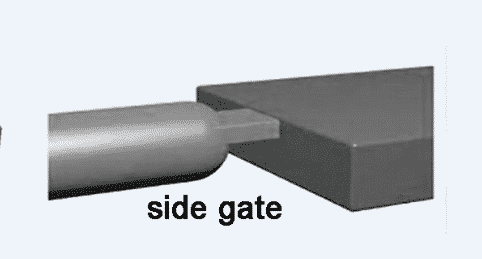
- Pros:
1) simple shape and easy machining.
2) it is easier to remove the gate.
- Cons:
1) gate can not separate from the product automatically.
2) the plastic part will leave the gate marks on the plastic part, obviously
Application:
Suitable for all kinds of parts, but not for long barrel profile parts.
pinpoint gate
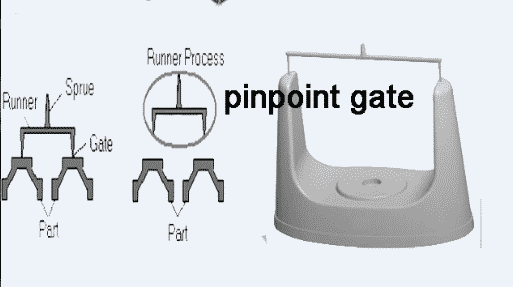
- Pros:
1)gate position could set on the most surface;
2) the gate can be separated from the part automatically.
3) the gate is small, and the gate marks the glue is small.
4) the stress near the gate location is small, and the injection molded parts are not easy to warp.
- Cons:
1) injection pressure is large, and it is not suitable to use plastic material with poor fluidity.
2) generally use 3 plate mold structure, the mold structure is complex, and the cost is high.
Application:
Because several gate points can be designed, it is often used for shell parts with a larger surface.
fan gate
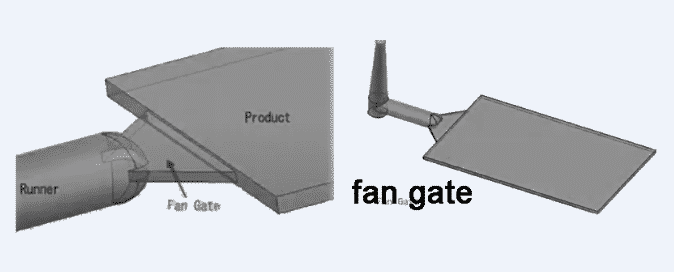
- Pros:
1) when the plastic flows through the gate, melt plastic distributes more evenly in the transverse direction and reduces the inner stress.
2) prevent air entry into the cavity and avoid defects, such as silver streaks and bubbles.
- Cons:
1) the part can not be separated from the gate automatically.
2) the remaining gate material will leave on the plastic part and be trimmed manually.
Application:
Commonly used to produce thin sheet and wide parts, and poor fluidity material, such as PC, PMMA, etc.
submarine gate (set on ejector pins or ribs)
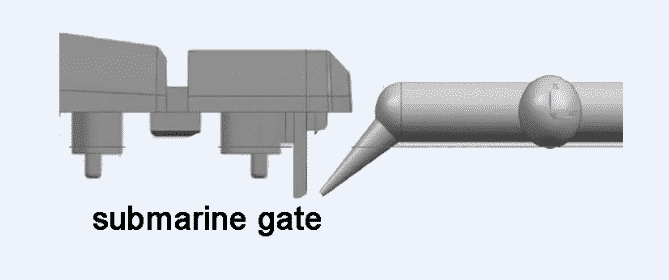
- Pros:
1) the choice of gate position is more flexible;
2) the gate can be separated from the plastic part automatically.
3) both the two plate die and the three plate die can be applied.
4) the gate can separate from the plastic part without post-processing of the gate
5) the gate location is inside the plastic parts and will not affect the appearance of the part.
- Cons:
1) the cloudy area is hard to remove.
2) it should cut off the redundant gate relics artificially;
3) the pressure loss from the gate to the cavity is large.
4) the appearance of the plastic part surface may find fingerprinting marks.
5) the machining process is complex;
6) the unreasonable design would easily lead to break the gate and block the gate channel.
Application:
It is suitable for plastic parts with an external appearance with no gate marks allowed.
Commonly used for ABS, HIPS, not used for POM, PBT, and other crystalline materials, also unsuitable for PC, PMMA, and other rigid materials, design should prevent the arc gate from breaking and blocking the gate.
Sliders and lifters
Any structure that hinders the mold opening or ejection is referred to as an undercut. The way to handle the undercut on the mold includes sliders, lifters, core pulling, gear rotating, etc.
The most commonly used is the sliders and the lifters.
sliderThe slider could be set on the static or movement mold plate, and sliders on the movement plate the most widely used.
The slider generally consists of a slide body, locking block(heel), Gibbs, cam pin (angle pin), wear-resistant block, spring, and so on.
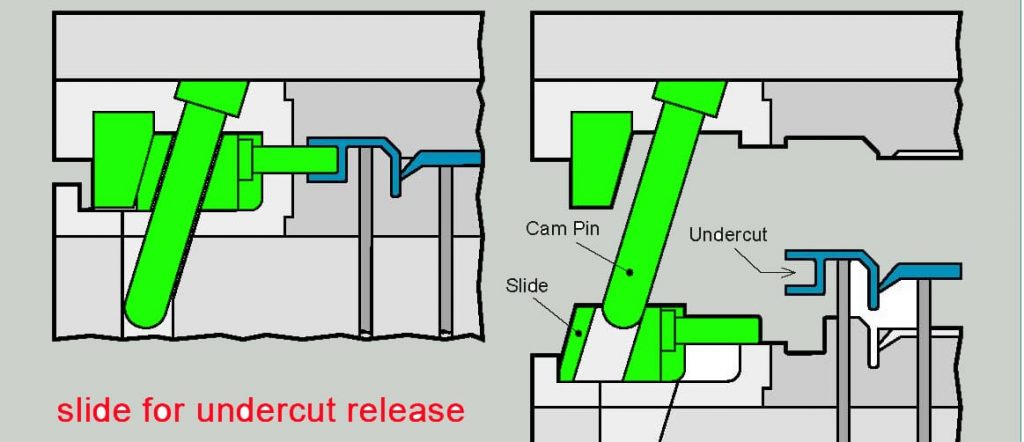
- lifter
The lifter generally is used to handle the undercut in the interior of the plastic part. At the same time, the slider generally treats with the external undercut of the plastic parts, but the lifter's structure is simpler than the slider structure.
The lifter has the function of releasing the internal undercut in the plastic parts, and it can also play the role of ejection.
So the design of the lifter on the mold generally reduces the arrangement of the ejector pins.
The lifter comprises an inclined top body, guide bushing, lifter seat, and wear-resistant block.
cost of plastic injection mold
The price of plastic mold depends on the size, material, and number of cavities. Usually, the cost of a injection molding tool is in the range of $300 to $5000 per cavity. The price of an injection molding tool can be calculated by multiplying its number of cavities and the price per cavity.
There are many different factors that affect the price of a plastic injection molding tool. Some of them are listed below:
the different size of the mold
Mold size is an important factor in determining the cost of a plastic injection mold. The larger the size of the mold, the more expensive it will be. For example, if you want to make a large number of products, you need to buy a large-scale mold. If you want to make small numbers of products at a time, then you can choose to buy a small-scale mold. The size of the mold also determines how much time it will take to produce the product. If you want to make large quantities of products at a time, then you need to buy a large-scale mold. This will allow you to save time and money as well.
the different size and complexity of the plastic parts
The size and complexity of the plastic parts are also important factors to consider. If you want to make a small number of products, then you can choose a simple design for your mold. However, if you want to make large quantities of products at once, then you need to buy an advanced-level mold with intricate designs. These types of molds are also more expensive than simple ones because they require more time and effort from the manufacturer.
the different mold material
The type of mold material is also an important consideration to make. You can choose between steel, aluminum, and plastic. Steel is a popular choice because it’s durable and long-lasting but can be more expensive than other materials. Aluminum is another viable option because it’s lightweight and cheaper than steel but not as strong. Plastic is the least expensive option but can be flimsy and not as durable as other materials. The type of mold material you choose will depend on how much money you want to spend, how long you want it to last, and what types of products you’re making.
the different cavity number
s and sizes you can choose from. The number of cavities refers to how many separate spaces are inside the mold. You can choose between one, two, or eight cavities depending on your needs. If you’re making just a few products at a time and don’t have a large budget for molds then one cavity is probably best for you.
the difference of using hot runner or cold runner
hot runner molds are the best for mass production because they allow you to pump out your product at a much faster rate. This is because there is a channel that runs through the mold and connects each cavity, allowing you to pour in liquid plastic or resin and get several pieces at once. Cold runner molds don’t have this feature, so it takes longer to produce your products.
the different mold base steel
There are many different types of steel for molds and each one has its own set of pros and cons. This is because all steels have different properties when it comes to hardness, strength, corrosion resistance, etc. For example, stainless steel doesn’t rust but isn’t as strong as carbon steel; however, this makes it much better for mold applications that will require less wear and tear.
the different hardness for mold parts
When you’re looking into different types of steel for molds, there are three hardness grades that should be considered: HRA, HRC and HRB. HRA stands for hardened and annealed; this type of steel has been quenched in a liquid bath of molten salts to harden it but does not have any tempering or stress relieving done afterwards. This means that the parts can easily break during mold assembly or later on when running through machines due to their brittle nature.
The different mold structure standard
Such as the American Society of Mechanical Engineers (ASME) and International Organization for Standardization (ISO), have different requirements for HRA steel. For example, ASME requires that all parts made from hardened and annealed steel have an HRC rating of at least 20; this ensures that they will not easily break or bend during operation.
Troubleshooting of Plastic Mold Design
To summarize the causes and cures of faults in injection molded components, the Table below should be consulted.
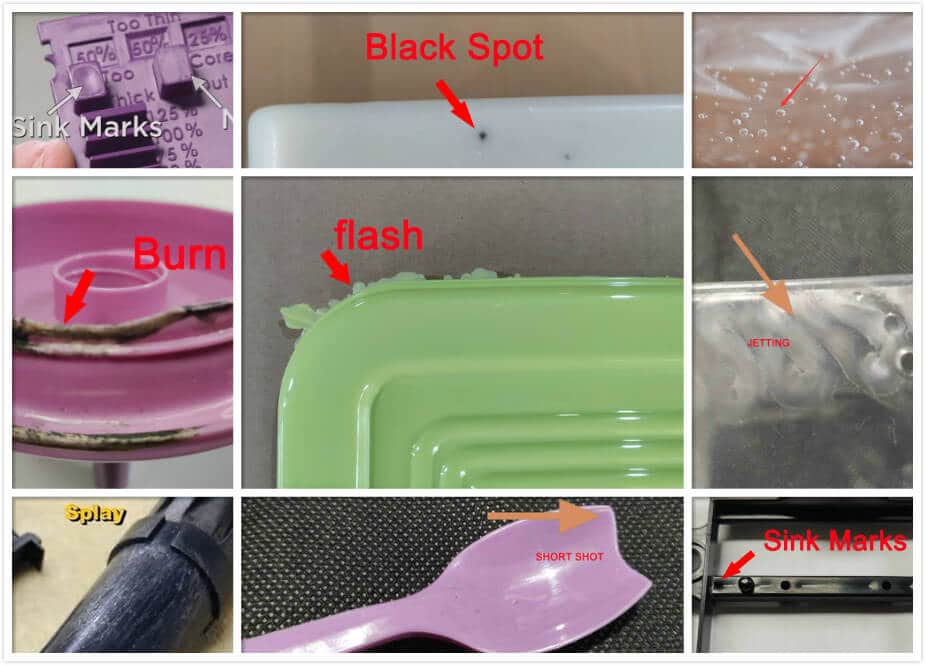
Comments
Post a Comment