101 tips:low volume injection molding
In the world of injection molding, there are a variety of different techniques that can be employed in order to create the desired product. One such technique is low volume injection molding. This method is often used when production quantities are relatively low, or when prototypes need to be created quickly and efficiently. Low volume injection molding has a number of advantages over other methods, including its speed, flexibility, and cost-effectiveness.
Injection molding is a manufacturing process for creating parts by injecting material into a mold. Injection molding can be performed with a wide variety of materials, including metals, glasses, and elastomers. The process is commonly used for mass-producing plastic parts. Low volume injection molding is a variation of the process that is used to create smaller quantities of parts, typically between 1 and 1000 pieces.
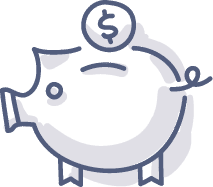
what is low volume injection molding?
Injection molding is a process in which melted plastic is injected into a mold to create a finished product. Low volume injection molding is a specialized form of this process that is used to create prototypes or limited production runs of a product.
The biggest advantage of low volume injection molding is that it allows manufacturers to produce parts quickly and cheaply as a whole. This type of molding also has a lower risk of defects, since the molds are usually less complex than those used for mass production.
Low volume injection molding is an ideal solution for companies who need parts quickly and don't have the budget for traditional manufacturing methods.
The benefits of low volume injection molding
Low volume injection molding is an excellent production method for short run, high-value products. Because of the low cost of the mold and tooling, it can be very cost effective to create a product in small quantities. Low volume injection molding is ideal for prototyping and small-scale production. It is a process that has many benefits.
One benefit is that it can be used to produce small batches of parts very quickly. This is important for companies that need to prototype new products or make small runs of parts for testing.
Low volume injection molding is also much less expensive than traditional injection molding as to a whole project, making it a good option for companies on a budget.
It is a cost-effective alternative to traditional manufacturing methods, such as CNC machining or 3D printing. In addition,low volume injection molding can be used to produce parts with very intricate designs. This makes it ideal for applications where precision is critical.
Why those important for injection molding cost
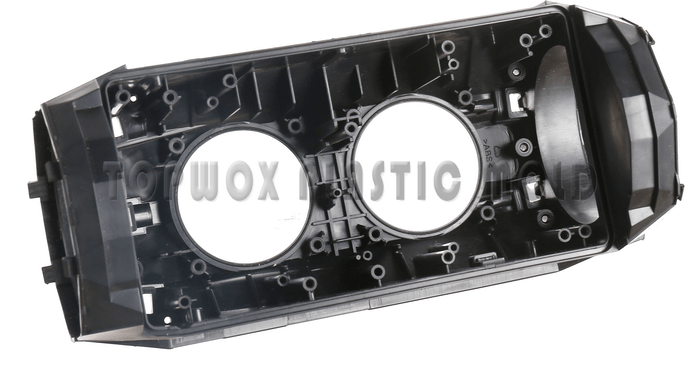
- Part size- bigger parts mean a bigger mold, which means that bigger steel will increase the steel cost for the injection mold.
- Part design- the more complex a part is, the more detailed the mold has to be. Some complicated parts will require special features to be added, such as lifters or sliders. Therefore, you should be open to advice from your mold maker and see if there’s anywhere that you can alter the part design to save on injection mold costs.
- Materials: Depending on the part material of choice, the injection mold will have to be made of a particular material. For instance, if corrosive plastic-like PVC is to be used, the mold will have to be stainless steel to avoid any damage, ultimately bump the price up.
- Part finish requirements- where parts have high gloss surface requirements, then more expensive steel and precise technical polishing will be vital, adding to the price.
- Production volume- higher volume molds need more cavities, and so the mold will be larger. They also require a higher steel grade to last for longer, which impacts the injection mold cost.
- Country of manufacture- different countries have different wage rates. If your mold is made in a country where labor costs are low, then you’ll naturally save money. In China, the average cost of an injection mold is around 40% less than in western nations.
The drawbacks of low volume injection molding
As more and more product development teams look to low volume injection molding for their small-scale production needs, it's important to be aware of the potential drawbacks of this manufacturing process.
One of the biggest issues with low volume injection molding is the high cost per unit. Because the mold and tooling costs are fixed, and the production runs are so small, the per unit cost is often much higher than with traditional mass production methods.
This can be a major problem when trying to sell products made with low volume injection molding, as customers are often price-sensitive. It can also make it difficult to justify the upfront investment in tooling and mold creation.
Another issue with low volume injection molding is that it can be difficult to find a manufacturer who is willing to produce such small quantities. Low volume injection molding is also not for most inventors who are just starting out. The costs of tooling and molds, as well as the difficulty in finding low volume producers, make low volume injection molding a difficult manufacturing process to manage if you are inexperienced.
Who is low volume injection molding best suited for?
Low volume injection molding is best suited for companies that need small to medium sized production runs. It is a cost effective way to produce parts without the need for expensive tooling.
Injection molding is a process in which molten material is injected into a mold and then cooled to form a solid shape. Low volume injection molding is a process that uses the same basic principles as injection molding, but on a smaller scale. Low volume injection molding is often used for prototyping or for producing small quantities of parts.
low volume injection molding for market research
In market research, low volume injection molding is a process that is used to create prototypes and small batches of parts. This process is ideal for market research because it is less expensive and faster than traditional methods such as CNC machining or 3D printing. Low volume injection molding can be used to create parts with complex geometries, and the finished parts can be used for testing and evaluation.
low volume injection molding for plastic part modification
Low volume injection molding is a process that can be used to modify plastic parts. Using low volume injection molding for plastic part modification can be an effective way to verify modifications while saving on production costs. Low volume injection molding is a process that involves using an existing plastic part and injecting new material into it. The injection process can be used to inject new material, such as fiberglass, carbon fiber or other reinforcement materials into the product.
This method is best suited for small-scale production runs or prototype development where products modifciation verification are key.
Tips for successful low volume injection molding
In low volume injection molding, the key is to focus on quality over quantity. In order to produce high-quality parts, it is important to use a mold that is designed for low volume production. This type of mold is typically made of aluminum or steel and has a lower number of cavities than a standard production mold.it is also important to consider the cost of materials when doing low volume injection molding. Since there are typically fewer parts being produced, the cost per part will be higher.
Low volume injection molding is a great way to produce small batches of plastic parts. Here are some tips for success:
1. Use a reputable company: There are many companies that offer low volume injection molding services. Do your research and choose a company with a good track record.
2. Know your material: Injection molding involves injecting molten plastic into a mold. Different plastics have different properties, so it’s important to choose the right one for your project.
3. Design for manufacturability: The design of your part will affect the cost and feasibility of manufacturing it. Work with an experienced designer who understands injection molding to create a part that can be easily and affordably produced.
4. final assembly You ll want to design your part so that it can be easily assembled. If you re designing a product that will be assembled in the field, it s important to think about how users will interact with your product and make sure they can assemble it easily.
final words
As the industry looks for new ways to reduce waste and be more efficient, low volume injection molding is becoming an increasingly popular option. This type of molding is perfect for small runs of parts or prototypes, as it requires less material and time to set up than traditional injection molding.
There are a few things to keep in mind when considering low volume injection molding, however. First, it is important to find a reputable and experienced company who can produce high-quality parts. Second, the cost of labor and materials per unit can be higher than with traditional methods, so it is important to get accurate quotes before committing to a project.
Overall, low volume injection molding is a great option for companies looking for a more efficient way to produce parts or prototypes.
https://www.plasticmoulds.net/101-tipslow-volume-injection-molding.html?feed_id=535&_unique_id=63140dc1df5b0
Comments
Post a Comment