The Future of Injection Molding: Embracing Innovation and Sustainability
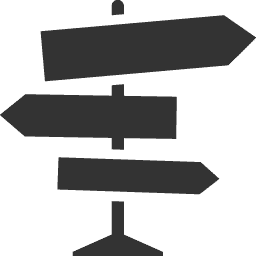
Hey there! If you're curious about the future of injection molding, you've come to the right place. In this blog, we'll dive into the latest trends and innovations shaping this ever-evolving industry.
We'll touch on plastic materials, molds, machines, automation, and surface treatments, all while highlighting some fascinating data. So, let's jump right in, shall we?
Plastic materials - Sustainability & bioplastics:
The future of injection molding is looking greener than ever, with a growing focus on sustainable materials. According to a study by Grand View Research, the global bioplastics market is expected to reach $35.47 billion by 2027, growing at a CAGR of 16.2% from 2020 to 2027. Manufacturers are increasingly turning to biodegradable and bio-based plastics, such as PLA, PHA, and bio-PET, to reduce their environmental footprint and meet consumer demands for eco-friendly products.
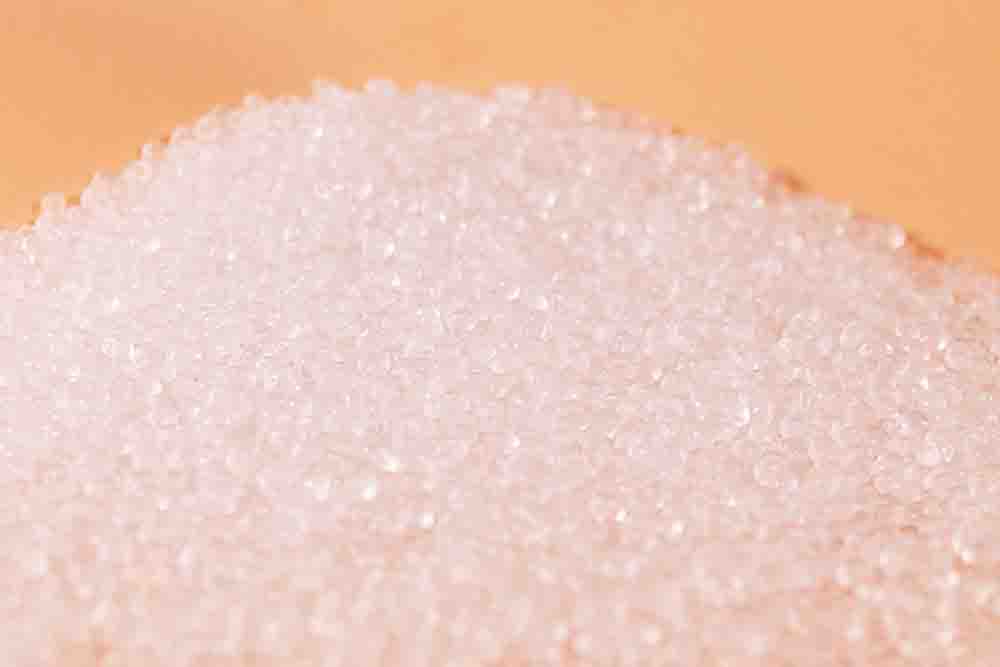
In addition to bioplastics, material development in injection molding is also focused on bio-composites and advanced polymers. Bio-composites, which combine natural fibers (like flax, hemp, or bamboo) with biodegradable resins, are gaining traction for their lightweight, high-strength, and eco-friendly properties. According to a report by MarketsandMarkets, the global natural fiber composites market is expected to reach $10.89 billion by 2024, at a CAGR of 11.0% from 2019 to 2024.
Advanced polymers, such as high-performance thermoplastics like PEEK, PEI, and PPSU, are being used in more demanding applications due to their exceptional mechanical, thermal, and chemical resistance properties. These advanced materials are particularly valuable in industries such as aerospace, automotive, and medical devices, where performance and durability are critical.
Molds - Additive manufacturing & micro-molding:
The mold-making process is undergoing a paradigm shift, with additive manufacturing (AM) technologies, like 3D printing, gaining traction. AM enables rapid prototyping and shorter lead times, allowing for more flexible and cost-effective mold production. Furthermore, micro-molding - the production of intricate, high-precision parts - is gaining popularity, especially in industries like medical devices and electronics. In fact, the global micro injection molding market is estimated to reach $1.58 billion by 2027, growing at a CAGR of 11.4% from 2020.
Machines - Energy efficiency & all-electric machines:
As the industry moves toward greener practices, energy-efficient injection molding machines are becoming more widespread. All-electric machines, known for their precision and energy savings of up to 50% compared to hydraulic machines, are becoming the go-to choice for manufacturers. According to a report by Fortune Business Insights, the global electric injection molding machines market is projected to grow at a CAGR of 4.6% between 2021 and 2028.
In addition to all-electric machines, multi-material injection molding machines are also making waves in the industry. These machines enable the production of complex, multi-component parts by injecting different materials in a single cycle. This capability not only enhances design flexibility but also reduces assembly costs and simplifies supply chains.
In-mold sensors are another innovation in injection molding machines, providing real-time feedback on process parameters like temperature, pressure, and flow rate. These sensors allow for better process control, ensuring consistent part quality and reducing the risk of defects. Moreover, the data collected by these sensors can be analyzed to identify trends and optimize the molding process further.
Automation - Robotics & Industry 4.0:
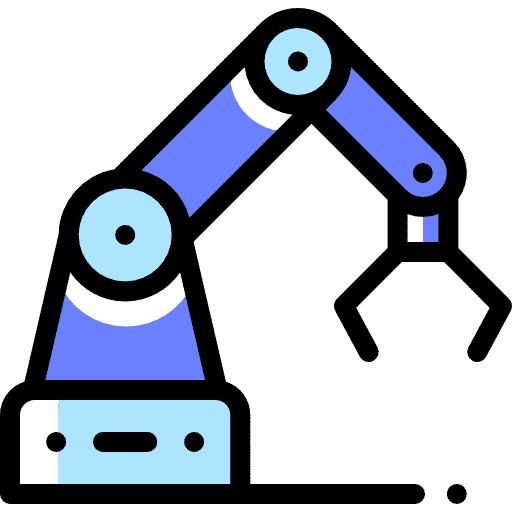
The future of injection molding is all about automation. Collaborative robots (cobots) and advanced automation systems are becoming increasingly prevalent, streamlining production and reducing labor costs. Embracing Industry 4.0, injection molding facilities are integrating smart technologies, such as IoT, AI, and Big Data analytics, to optimize processes and drive efficiency. One study by McKinsey & Company suggests that adopting Industry 4.0 technologies could increase productivity in the plastics sector by 15-20%.
In the realm of automation, vision systems are playing an increasingly important role in the injection molding process. These systems utilize cameras and sensors to inspect parts for defects, ensuring quality control and reducing waste. By integrating AI and machine learning, vision systems can adapt and improve over time, further enhancing their accuracy and efficiency.
Digital twin technology is another trend that's revolutionizing the injection molding industry. A digital twin is a virtual replica of a physical asset, such as an injection molding machine or an entire production line. By simulating and optimizing the molding process in a digital environment, manufacturers can identify potential issues, test various scenarios, and implement improvements before making changes to the actual production process. According to Gartner, 75% of organizations implementing IoT will have adopted digital twin technology by 2023.
Surface treatments - Multi-functional coatings & nano-technology:
Last but not least, innovative surface treatments are revolutionizing injection molded parts. Multi-functional coatings, such as hydrophobic, and self-healing coatings, are enhancing the performance and durability of plastic parts. Additionally, nano-technology is enabling the development of new materials with unique properties, like superior strength and thermal conductivity, opening up a world of possibilities for injection molding.
There you have it! The future of injection molding is shaping up to be an exciting blend of sustainability, technological advancements, and innovative materials. As we continue to push the boundaries of what's possible, one thing's for sure - this industry is not slowing down anytime soon. So, stay tuned for more cutting-edge developments in the world of injection molding!
https://www.plasticmoulds.net/the-future-of-injection-molding-embracing-innovation-and-sustainability.html?feed_id=1234&_unique_id=642b913e60206
Comments
Post a Comment