Protect Your Plant from Injection Molding Risks with Secure Safeguards!
When making injection molding, it is important to have various safety measures in place to protect both the workers and the equipment. Some common safety precautions in an injection molding plant include:
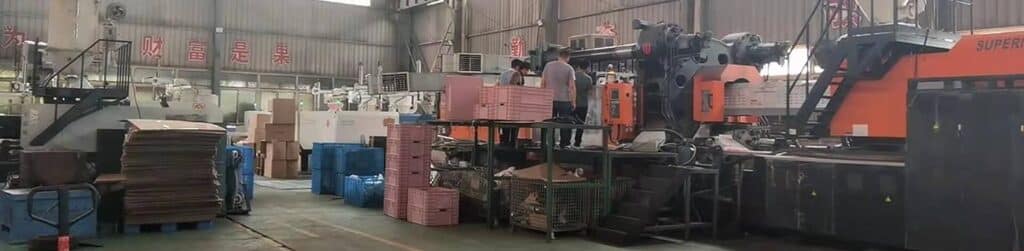
Personal protective equipment:
Workers should wear gloves, safety glasses, and other protective gear to minimize the risk of injury for it is easy for workers to contact the hot nozzle,melt material and hot products.
Personal protective equipment (PPE) is an important aspect of safety in an injection molding plant. It is designed to protect workers from potential hazards such as chemicals, heat, noise, and machinery. Some common types of PPE used in injection molding include:
Gloves: Workers handling hot or sharp components should wear gloves to protect their hands from burns or cuts.Some plastic items are 60 degree when ejected from the injection mold.
Safety glasses: Workers should wear safety glasses to protect their eyes from flying debris, chemicals, or hot splashes.
Respirators: In some cases, workers may be exposed to fumes or dust (POM injection molding would lead to pungent odor )generated during the molding process. Respirators can help filter out harmful particles and protect workers from respiratory problems.
Protective footwear: Workers should wear closed-toe shoes with non-slip soles to prevent slips, trips, and falls.
Hard hats: Workers should wear hard hats to protect their heads from falling objects or from bumping into overhead structures.
Machine guards:
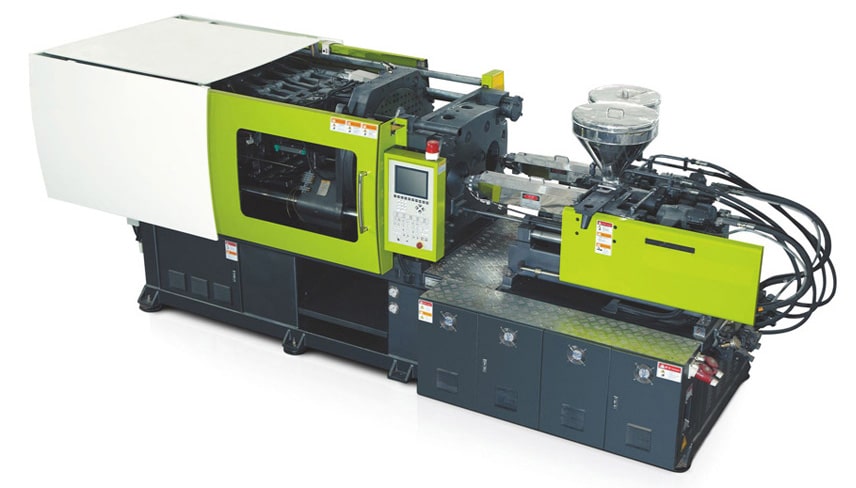
Machine guards are an important safety feature in an injection molding plant. They are designed to physically protect workers from moving platens and hot surfaces on the injection molding machine.
There are several types of machine guards commonly used in injection molding, including:
Light curtains: Light curtains are safety devices that emit beams of light across the opening of injection molding machine. If the beams are broken by a person or object, the machine will stop closing automatically,wich is very important for big mould,for workers have to go into the machine and stand between 2 mould halves to taks the plastic part.
Safety interlocks:
Safety interlocks are physical barriers that prevent access to dangerous parts of the injection molding machine. They can be doors, gates, or covers that must be closed before the machine will operate.If the this interlocks dont recover its position,the machine wont work.
Barrier guards:
Barrier guards are physical barriers that surround the moving parts of the machine to prevent workers from coming into direct contact with them.As to the injection molding machine,it is safe door which separate workers and injection molds.
Emergency stop buttons:
Emergency stop buttons, or emergency shutdown buttons, are a critical safety feature in an injection molding plant,a very big red button on the control panel. They provide a quick and easy way for workers to shut down the molding machine in the event of an emergency, such as a machine malfunction, operator error, or a fire.
Emergency stop buttons should be easily accessible and clearly marked (red for injection machine) so that workers can quickly locate and activate them in an emergency. They should also be connected to the molding machine's control system to immediately stop all movement and power to the machine when activated.
Proper ventilation:
Proper ventilation is crucial in an injection molding plant to maintain a safe and healthy working environment for employees. During the molding process, various fumes and vapors can be produced from the plastic materials (it is cery common for PA and POM injection molding), solvents, and other chemicals(FR material) used in the process. These fumes can be hazardous to human health if not properly removed from the work area.
A good ventilation system should be designed to capture and remove fumes and vapors from the molding area, to prevent workers from breathing in harmful substances. This can be achieved through the use of exhaust fans, ductwork, and scrubbers, which clean the air before it is expelled from the building.
In addition to removing fumes and vapors, proper ventilation can also help regulate the temperature and humidity(Too much water will lead to issues on the PA injection molding surface) in the molding area. This can help prevent overheating and condensation, which can affect the quality of the molded product and create a potential safety hazard.
lifting safety:
To follow safe lifting techniques, workers should:
Use proper lifting posture: Workers should keep their backs straight and bend at the knees when lifting heavy materials(full bag plastic material & mold steel plates) to minimize the risk of back injury.
Use proper grip: Workers should use a firm grip and hold the material close to their body when lifting to minimize the risk of dropping the load.
Ask for help: Workers should not hesitate to ask for help when lifting heavy or awkward materials to prevent injury.
Use proper equipment: Workers should use forklifts,which is used to lift the mold and its components, pallet jacks, and other equipment designed for material handling to minimize the risk of injury and make handling heavy materials easier.
Fire protection:
Fire extinguishers and other fire suppression equipment are essential for protecting an injection molding and EDM plant from the risk of fire. Here are some key points to consider:
Readily available: Fire extinguishers and other fire suppression equipment should be located in easily accessible areas throughout the molding plant and EDM machine,EDM remove steel by sparking, so electrical sparks can easily cause fires - they can be quickly and easily reached in the event of a fire.
Proper types: The type of fire extinguisher or suppression equipment needed will depend on the specific materials and conditions in the molding plant. Common fire suppression methods for plastic manufacturing include dry chemical extinguishers, CO2 extinguishers for the fire caused by electricity, and foam systems..
Regular training:
Workers should be trained on how to safely operate the injection molding machine, including how to start and stop the machining machine(lathe,drilling machine...), how to set up and adjust molds(mold fitting is a very importsnt step, and how to monitor the production process. They should also be trained on the proper use of PPE, such as gloves, safety glasses, and hearing protection, to protect themselves from potential hazards such as hot surfaces, moving parts, and loud noise.
In addition to machine operation training, workers should also be trained on safety procedures for handling raw materials, molded products, and waste. This can include information on safe lifting techniques, the proper storage and disposal of waste materials, and the handling of hazardous materials.
FINAL
Adhering to these safety precautions and regularly reviewing and updating safety procedures can help ensure a safe and efficient injection molding process.
https://www.plasticmoulds.net/protect-your-plant-from-injection-molding-risks-with-secure-safeguards.html?feed_id=1184&_unique_id=63de4a635cb58
Comments
Post a Comment