cooling for injection molding
A system which constant transfers heat from the melt in the mold or heats the mold to the injection temperature is called a temperature control system.
Mold temperature refers to the surface temperature of the mold cavity that comes in contact with the product.
It directly affects the flow of the melt, the cooling of the product, and the quality of the product.
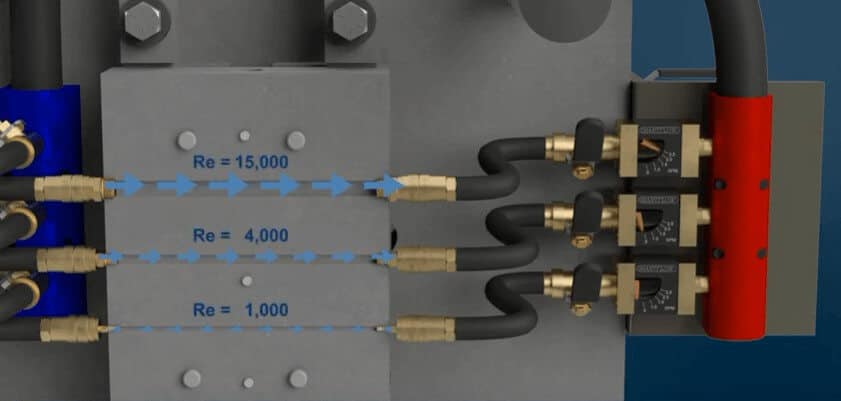
An injection mold is a production tool which can repeatedly mass-produce plastic products with the same structure and the dimensional accuracy.
it is a heat exchanger.
In order to ensure the molding quality and production efficiency, it is necessary to use the medium to heat or cool the mold to control the temperature within a reasonable range.
The productivity of the mold depends on the speed of the mold heat exchange. The speed of the mold heat exchange depends on the mold heat exchange. The mold heat exchange depends on the temperature of the melt, the demolding temperature, and the plastic.
The design of the temperature control system for the molds with high precision and mass production is rigorous. Sometimes, it must design particular temperature regulators to control the temperature of various parts of the mold strictly.
Control system for the injection mold temperature is one of the difficulties in mold design.
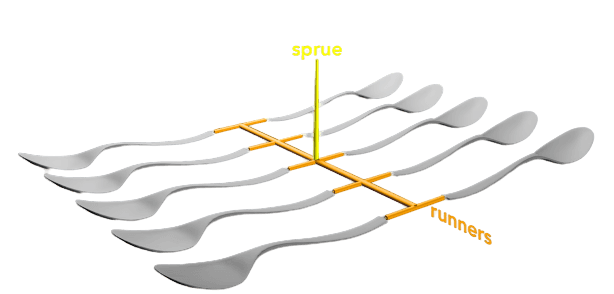
The temperature control system of the mold includes cooling and heating the mold.
For most plastics, the mold needs cooling.
However, for plastics with poor viscosity and poor fluidity, such as PC, hard PVC, PSF, PPO, etc., the temperature of the mold can be raised to improve its fluidity. The mold temperature should be controlled between 80 and 120 °C.
For these molds, if the surface heat dissipation is fast, the heat of the melt alone is not enough to maintain the mold temperature, so the mold also needs to set the heating system to heat the mold before or during the injection to ensure that the mold runs well.
Some molds have both cooling system and heating system. One situation is that in a cold area or a large mold, the mold must be preheated before it is produced.
When the temperature of the mold reaches the molding process requirements, the heating system can be turned off.
If the temperature of the mold is higher than the temperature that plastic molding process is required, the mold cooling system is then open so that the temperature of the mold is kept at the required degree.
In the second case, the plastic products are plentiful, and the wall thickness is not uniform.
Then, the thick section should be cooled, and the thin section must be heated in order to improve the melt flow.
For small thin-walled products, and the molding process requires that the mold temperature is not too low, a heating device may not be provided, no cooling device may be provided, and the mold is naturally cooled.
The Importance of Injection Mold Temperature Control
In injection molding, the temperature of the mold directly affects the filling of the cavity, the quality of the product, and the molding cycle.
For PE, PP, HIPS, ABS, etc. with good fluidity, reducing the mold temperature can lower the stress cracking, and the mold temperature should be controlled at 50 degrees, the mold must have a cooling system.
For plastics with poor fluidity such as PC, PPO, and PSF, increasing the mold temperature will help reduce the internal stress of the product.
The mold temperature should be controlled between 80 and 120°C. For this purpose, a heating system should be installed on the mold.
In addition, crystalline plastics (such as PE, PP, POM, PA, PET, etc.) and amorphous plastics (such as PS, HIPS,
The cooling process of PVC, PMMA, PC, ABS, polysulfone, etc. is different.
For crystalline plastics, when cooled medium through the crystalline area of the plastic, the hot is released, but the temperature of the plastic remains unchanged.
Only after the crystalline area is reached, the plastic can be further cooled. Therefore, the crystalline plastic needs to be taken away from the hot when compared with the non-crystalline plastics. need more.
[table id=2 /]
-----------
If the mold temperature is too high, the molding shrinkage is uneven. And the product is significantly deformed after demolding. Also, it is easy to cause flash and sticking.
If the mold temperature is too low, the melt fluidity is poor, the profile of the product is not clear, and the surface may have obvious defects such as silver streak or jetting.
When the temperature of the mold is not uniform, the temperature of the molded product after solidification in the mold cavity is not uniform.
This could result in uneven shrinkage of the product, internal stress, and finally deformation, cracking, and warpage of the product after the product is discharged. Therefore, the cooling of parts must be balanced.
The fluctuation of the mold temperature has a significant influence on the shrinkage, dimensional stability, deformation, stress cracking, and surface quality of the product.
Cooling time accounts for about 80% of the entire molding cycle.
The mold temperature is controlled well; the melt can be solidified in time, which would shorten the molding cycle, improve the labor productivity;
if mold temperature control is not good, the slow solidification will make the mold temperature drop very slowly. In the worst case, the mold operation would be stopped. the result was a longer cycle time and greatly affect the operation of molds.
In plastic injection molding, the temperature of the melt in the cavity is generally between 200 and 300 degrees: the melt is cooled and solidified into a product in the cavity.
When the product is taken out from the mold, the temperature is generally 60, the heat released from the melt is transferred to the mold.
To ensure normal production, the mold must transfer this heat quickly so that the temperature of the mold is always controlled within a reasonable range. The structure transferring the heat from the melt to the mold is called the cooling system.
The heat transfer methods are conduction, convection, and radiation. 95% of the heat in the mold is carried away by heat conduction. The medium for heat conduction in the mold is mainly water (including normal temperature water and frozen water), and sometimes oil and beryllium copper.
The convective heat transfer in the mold is primarily carried out using a fan or the like, and the circulation air naturally cools the mold.
Most molds require a cooling system, which is suitable for plastics with low viscosity and good fluidity, such as PE, PP, PS, ABS.
The higher the mold temperature is, the better the fluidity of the plastic melt in the cavity is.
The better the filling is, the longer the cooling time will be, plastic mold high temperature will increase the cycle time, which is not good for the mass production.
When the mold temperature is too low, the surface of the product will be poor, and in the case of glass fiber reinforced plastic is used, a high mold temperature can prevent the surface with fibers. also, it can also prevent the flow marks and weld marks.
That is, the high mold temperature is beneficial to the appearance of the product, but it will also increase the cycle time of the molding.
If the cooling is not complete, the surface of the thick wall will have the shrink and sink problem.
Although the wall thickness is appropriate, the various sections of the product are not uniformly cooled, or the cooling rate of the multiple sections is different, which will result in a different shrinkage rate, and the products may also be warped.
Therefore, the mold temperature needs to work in with the wall thickness, shape of the product and the plastic material.
The parts are kept at the same temperature so that the cooling rate of each section is uniform.
However, the faster and more uniform the cooling of the mold needs, the more the cooling water is required, which inevitably increases the size between the mold cavities and lengthens the cooling channel. mold size will increase.
When the molten plastic is filled in the cavity, if the mold temperature is low, it quickly solidifies, and the flow becomes slower.
For plastic to fill the cavity, the injection pressure must be increased. This is particularly noticeable for thin-walled products. The lower the mold temperature is , the greater the injection pressure will be, the greater the residual stress in the product.
This residual stress is the main cause of cracking and deformation of the product. Stress cracking is more likely to occur in melted materials such as PC and PPO.
There are many factors affect mold cooling, which includes the following aspects.
The heat is released from the mold cavity to the product. The formula for the heat transfer to the mold is as follows. This is the difference between the temperature of the melt injected into the mold cavity and the temperature at which the product is ejected from the mold. The different plastics are different from each other, so the temperature difference is also distinct.
The cooling medium generally uses water, which is economical and has a good cooling effect. However, the cooling water makes it easy to rust waterways.
Contaminants in the cooling water (such as calcium carbonate, etc.) are prone to precipitation on the cooling pipes, and they both decrease The ability to conduct heat, in severe cases, it can even block the pipe and reduce the flow.
There are two kinds of laminar flow and turbulent flow in the fluid in the straight tube . The laminar flow is when the thin liquid adjacent to each other and parallel slides relative to each other in the direction of the external force.
The velocity and direction of the fluid at each point change with time and the fluids interfere with each other severely. The flow rate of the cooling medium is preferably as high as possible, and the flow state thereof is preferably turbulent.
The use of beryllium copper and aluminum alloys as mold inserts is greatly superior to steel. Therefore, many core inserts or thick-walled, simple-structure mold inserts use beryllium copper or aluminum alloys.
The thermal conductivity of beryllium copper is four times that of steel, but its elastic modulus is only 1/2 of that of steel, and its impact strength is also lower than that of tool steel.
The strength of aluminum alloy is worse than that of beryllium copper.
The design of the cooling system includes the pipe size, layout, location, and cooling style.
During the molding cycle, the cooling time refers to the duration from the filling of the cavity to the opening of the mold and the release of the plastic part. “Can be pushed out” means that the melt is fully solidified and has a certain strength and rigidity, and it does not cause defects such as whitening spot and deformation when being pushed out.
The cooling time accounts for about 80% of the molding cycle.
In the remaining time, the melt filling cavity time accounts for about 5%, and the opening and closing time of the ejection and mold accounts for about 15%.
Therefore, for molds with mass production requirements, it is necessary to reduce the cooling time, which is the best way to shorten the molding cycle.
The cooling time is related to the size and shape of the product, as well as the wall thickness of the product, the plastic used and the inserted steel material, but mainly depends on the design of the mold cooling system.
The cooling time calculated by the theoretical formula is not reliable most of the time. In actual work, it is often the test mold to determine the cooling time based on the experience and then adjust according to the injection molding situation,
We can try to improve the cooling effect of the mold from the following aspects.
The cooling pipe dia should be as large as possible, and the number should be as many as possible to increase the heat transfer, shorten the cooling time.
However, if the size of the cooling channel is too large and the number is too many, it, in turn, leads to a big size of the plastic mold and the length of runners.it will invite venting problem.
Also, the water flow in the channel will become laminar, which will affect the cooling effect. Therefore, the size of the cooling pipe should be selected according to the size of the mold and the product.
Increase the cooling pipes near the thick-walled section where the temperature is high.
We should choose steel with high thermal conductivity, but in some places, it is difficult to dissipate heat, copper or aluminum alloy is available at this time. The use of alloys as inserts, of course, is based on the premise of the rigidity and strength of the mold.
The thinner the wall thickness is; the less cooling time is required. On the contrary, the thicker the wall thickness is, the longer the cooling time required. Therefore, the wall thickness should not be too thick and uniform.
The cooling circuit should be connected in series as much as possible. If parallel lines are used, it will often produce stagnant water, which will affect the cooling effect. Also, the distance between the cooling circuit and the cavity should be such that the temperature of the cavity surface is uniform.
Common molds with large production volumes can be cooled quickly. Precision molds should be slow-cooled.
During the production process, the center temperature of the mold is very high in order to ensure the uniform temperature of the various sections of the mold, the center part of the mold should be cooled.
Mold temperature refers to the surface temperature of the mold cavity that comes in contact with the product.
It directly affects the flow of the melt, the cooling of the product, and the quality of the product.
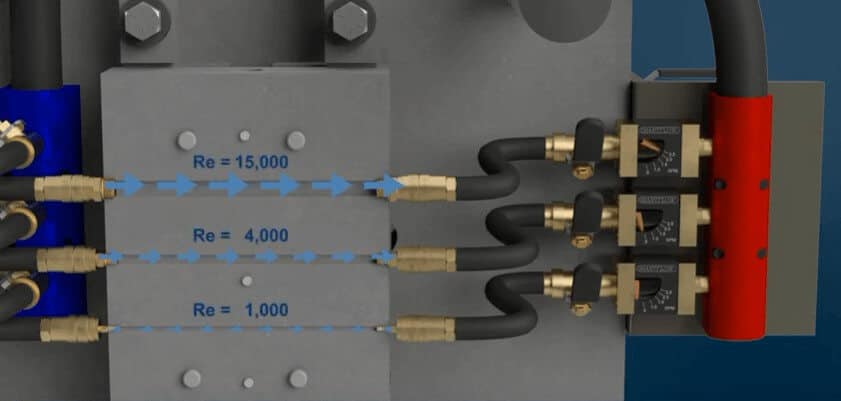
An injection mold is a production tool which can repeatedly mass-produce plastic products with the same structure and the dimensional accuracy.
it is a heat exchanger.
In order to ensure the molding quality and production efficiency, it is necessary to use the medium to heat or cool the mold to control the temperature within a reasonable range.
The productivity of the mold depends on the speed of the mold heat exchange. The speed of the mold heat exchange depends on the mold heat exchange. The mold heat exchange depends on the temperature of the melt, the demolding temperature, and the plastic.
The design of the temperature control system for the molds with high precision and mass production is rigorous. Sometimes, it must design particular temperature regulators to control the temperature of various parts of the mold strictly.
Control system for the injection mold temperature is one of the difficulties in mold design.
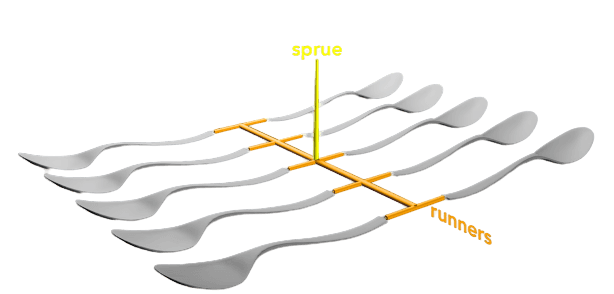
The temperature control system of the mold includes cooling and heating the mold.
For most plastics, the mold needs cooling.
However, for plastics with poor viscosity and poor fluidity, such as PC, hard PVC, PSF, PPO, etc., the temperature of the mold can be raised to improve its fluidity. The mold temperature should be controlled between 80 and 120 °C.
For these molds, if the surface heat dissipation is fast, the heat of the melt alone is not enough to maintain the mold temperature, so the mold also needs to set the heating system to heat the mold before or during the injection to ensure that the mold runs well.
Some molds have both cooling system and heating system. One situation is that in a cold area or a large mold, the mold must be preheated before it is produced.
When the temperature of the mold reaches the molding process requirements, the heating system can be turned off.
If the temperature of the mold is higher than the temperature that plastic molding process is required, the mold cooling system is then open so that the temperature of the mold is kept at the required degree.
In the second case, the plastic products are plentiful, and the wall thickness is not uniform.
Then, the thick section should be cooled, and the thin section must be heated in order to improve the melt flow.
For small thin-walled products, and the molding process requires that the mold temperature is not too low, a heating device may not be provided, no cooling device may be provided, and the mold is naturally cooled.
The Importance of Injection Mold Temperature Control
In injection molding, the temperature of the mold directly affects the filling of the cavity, the quality of the product, and the molding cycle.
Different Mold Temperature for a different material
For PE, PP, HIPS, ABS, etc. with good fluidity, reducing the mold temperature can lower the stress cracking, and the mold temperature should be controlled at 50 degrees, the mold must have a cooling system.
For plastics with poor fluidity such as PC, PPO, and PSF, increasing the mold temperature will help reduce the internal stress of the product.
The mold temperature should be controlled between 80 and 120°C. For this purpose, a heating system should be installed on the mold.
In addition, crystalline plastics (such as PE, PP, POM, PA, PET, etc.) and amorphous plastics (such as PS, HIPS,
The cooling process of PVC, PMMA, PC, ABS, polysulfone, etc. is different.
For crystalline plastics, when cooled medium through the crystalline area of the plastic, the hot is released, but the temperature of the plastic remains unchanged.
Only after the crystalline area is reached, the plastic can be further cooled. Therefore, the crystalline plastic needs to be taken away from the hot when compared with the non-crystalline plastics. need more.
[table id=2 /]
-----------
mold temperature effect on product accuracy
If the mold temperature is too high, the molding shrinkage is uneven. And the product is significantly deformed after demolding. Also, it is easy to cause flash and sticking.
If the mold temperature is too low, the melt fluidity is poor, the profile of the product is not clear, and the surface may have obvious defects such as silver streak or jetting.
When the temperature of the mold is not uniform, the temperature of the molded product after solidification in the mold cavity is not uniform.
This could result in uneven shrinkage of the product, internal stress, and finally deformation, cracking, and warpage of the product after the product is discharged. Therefore, the cooling of parts must be balanced.
The fluctuation of the mold temperature has a significant influence on the shrinkage, dimensional stability, deformation, stress cracking, and surface quality of the product.
Effect of Mold Temperature on Injection Cycle
Cooling time accounts for about 80% of the entire molding cycle.
The mold temperature is controlled well; the melt can be solidified in time, which would shorten the molding cycle, improve the labor productivity;
if mold temperature control is not good, the slow solidification will make the mold temperature drop very slowly. In the worst case, the mold operation would be stopped. the result was a longer cycle time and greatly affect the operation of molds.
The concept of Injection Mold Cooling
In plastic injection molding, the temperature of the melt in the cavity is generally between 200 and 300 degrees: the melt is cooled and solidified into a product in the cavity.
When the product is taken out from the mold, the temperature is generally 60, the heat released from the melt is transferred to the mold.
To ensure normal production, the mold must transfer this heat quickly so that the temperature of the mold is always controlled within a reasonable range. The structure transferring the heat from the melt to the mold is called the cooling system.
The heat transfer methods are conduction, convection, and radiation. 95% of the heat in the mold is carried away by heat conduction. The medium for heat conduction in the mold is mainly water (including normal temperature water and frozen water), and sometimes oil and beryllium copper.
The convective heat transfer in the mold is primarily carried out using a fan or the like, and the circulation air naturally cools the mold.
Most molds require a cooling system, which is suitable for plastics with low viscosity and good fluidity, such as PE, PP, PS, ABS.
The contradiction of Mold Temperature Requirements
The contradiction between the fluidity and the cycle time
The higher the mold temperature is, the better the fluidity of the plastic melt in the cavity is.
The better the filling is, the longer the cooling time will be, plastic mold high temperature will increase the cycle time, which is not good for the mass production.
Contradictions between the appearance and the cycle time
When the mold temperature is too low, the surface of the product will be poor, and in the case of glass fiber reinforced plastic is used, a high mold temperature can prevent the surface with fibers. also, it can also prevent the flow marks and weld marks.
That is, the high mold temperature is beneficial to the appearance of the product, but it will also increase the cycle time of the molding.
Contradictions between the cycle time and the size of the mold
If the cooling is not complete, the surface of the thick wall will have the shrink and sink problem.
Although the wall thickness is appropriate, the various sections of the product are not uniformly cooled, or the cooling rate of the multiple sections is different, which will result in a different shrinkage rate, and the products may also be warped.
Therefore, the mold temperature needs to work in with the wall thickness, shape of the product and the plastic material.
The parts are kept at the same temperature so that the cooling rate of each section is uniform.
However, the faster and more uniform the cooling of the mold needs, the more the cooling water is required, which inevitably increases the size between the mold cavities and lengthens the cooling channel. mold size will increase.
Contradictions between mold temperature and injection pressure
When the molten plastic is filled in the cavity, if the mold temperature is low, it quickly solidifies, and the flow becomes slower.
For plastic to fill the cavity, the injection pressure must be increased. This is particularly noticeable for thin-walled products. The lower the mold temperature is , the greater the injection pressure will be, the greater the residual stress in the product.
This residual stress is the main cause of cracking and deformation of the product. Stress cracking is more likely to occur in melted materials such as PC and PPO.
Factors Affecting Mold Cooling
There are many factors affect mold cooling, which includes the following aspects.
The difference between the melt temperature and the demolding temperature.
The heat is released from the mold cavity to the product. The formula for the heat transfer to the mold is as follows. This is the difference between the temperature of the melt injected into the mold cavity and the temperature at which the product is ejected from the mold. The different plastics are different from each other, so the temperature difference is also distinct.
The type of the cooling medium
The cooling medium generally uses water, which is economical and has a good cooling effect. However, the cooling water makes it easy to rust waterways.
Contaminants in the cooling water (such as calcium carbonate, etc.) are prone to precipitation on the cooling pipes, and they both decrease The ability to conduct heat, in severe cases, it can even block the pipe and reduce the flow.
There are two kinds of laminar flow and turbulent flow in the fluid in the straight tube . The laminar flow is when the thin liquid adjacent to each other and parallel slides relative to each other in the direction of the external force.
The velocity and direction of the fluid at each point change with time and the fluids interfere with each other severely. The flow rate of the cooling medium is preferably as high as possible, and the flow state thereof is preferably turbulent.
The thermal conductivity of mold parts
The use of beryllium copper and aluminum alloys as mold inserts is greatly superior to steel. Therefore, many core inserts or thick-walled, simple-structure mold inserts use beryllium copper or aluminum alloys.
The thermal conductivity of beryllium copper is four times that of steel, but its elastic modulus is only 1/2 of that of steel, and its impact strength is also lower than that of tool steel.
The strength of aluminum alloy is worse than that of beryllium copper.
The design of the cooling system includes the pipe size, layout, location, and cooling style.
Determination of Cooling Time
During the molding cycle, the cooling time refers to the duration from the filling of the cavity to the opening of the mold and the release of the plastic part. “Can be pushed out” means that the melt is fully solidified and has a certain strength and rigidity, and it does not cause defects such as whitening spot and deformation when being pushed out.
The cooling time accounts for about 80% of the molding cycle.
In the remaining time, the melt filling cavity time accounts for about 5%, and the opening and closing time of the ejection and mold accounts for about 15%.
Therefore, for molds with mass production requirements, it is necessary to reduce the cooling time, which is the best way to shorten the molding cycle.
The cooling time is related to the size and shape of the product, as well as the wall thickness of the product, the plastic used and the inserted steel material, but mainly depends on the design of the mold cooling system.
The cooling time calculated by the theoretical formula is not reliable most of the time. In actual work, it is often the test mold to determine the cooling time based on the experience and then adjust according to the injection molding situation,
How to improve mold temperature regulation
We can try to improve the cooling effect of the mold from the following aspects.
(1) cooling pipe size
The cooling pipe dia should be as large as possible, and the number should be as many as possible to increase the heat transfer, shorten the cooling time.
However, if the size of the cooling channel is too large and the number is too many, it, in turn, leads to a big size of the plastic mold and the length of runners.it will invite venting problem.
Also, the water flow in the channel will become laminar, which will affect the cooling effect. Therefore, the size of the cooling pipe should be selected according to the size of the mold and the product.
Increase the cooling pipes near the thick-walled section where the temperature is high.
(2) steel
We should choose steel with high thermal conductivity, but in some places, it is difficult to dissipate heat, copper or aluminum alloy is available at this time. The use of alloys as inserts, of course, is based on the premise of the rigidity and strength of the mold.
(3) The wall thickness
The thinner the wall thickness is; the less cooling time is required. On the contrary, the thicker the wall thickness is, the longer the cooling time required. Therefore, the wall thickness should not be too thick and uniform.
(4) cooling circuit
The cooling circuit should be connected in series as much as possible. If parallel lines are used, it will often produce stagnant water, which will affect the cooling effect. Also, the distance between the cooling circuit and the cavity should be such that the temperature of the cavity surface is uniform.
(5) rapid cooling and slow cooling
Common molds with large production volumes can be cooled quickly. Precision molds should be slow-cooled.
(6) cooling the mold center
During the production process, the center temperature of the mold is very high in order to ensure the uniform temperature of the various sections of the mold, the center part of the mold should be cooled.
you are providing us wonderful knowledge and very much useful and relevant do provide more information do more update on this topic
ReplyDeletemy pleasure!
ReplyDelete