Hot runner system for injection mold
Hot runner system can be seen as an extension of injection molding machinery. The function of the hot runner system is to thermally insulated to send the thermoplastic melt to the plastic mold.
The hot runner can be heated independently while it is thermally insulated in the injection mold, which can compensate for heat loss caused by contact with the "cold" mold surface.
https://www.youtube.com/watch?v=QGq0YxrIHPs
Hot runner molds have been successfully used to shoot various plastic materials.
Almost all plastic materials that can be shot with cold runner molds can be processed with hot runner molds.
The minimum injection parts are less than 0.1g, and the maximum injection parts are more than 30kg.
Hot runner molds are widely used in electronics, automobiles, medical, daily necessities, toys, packaging, construction, office equipment and etc., industries
The most important two technical factors:
A typical hot runner system consists of the following parts:
When hot runner is adopted, the correct selection of gate type is very important. The gate directly determines the selection of hot runner system and the mold manufacture.
Therefore, according to different gate types, hot runner systems can be divided into three types:
Each type of hot runner system has its important characteristics and application.
Many factors need to be considered when selecting gate and hot runner system , among which the most important ones are plastic materials and additives, weight and wall thickness , quality requirements , tool life and production of parts, etc.
Pros:
Cons:
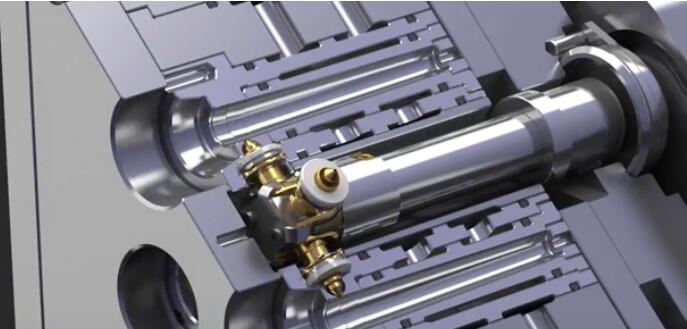
This system principle is that the HOT TIP located at the front end of the nozzle is matched with the cooling system to accurately adjust and control the plastic molding processing temperature at the gate.
Therefore, the material and shape of the nozzle HOT TIP are very important.
HOT TIP hot runner system can be used to process most crystalline and amorphous plastics such as PP, PE, PS, LCP, PA, PET, PBT, PEEK, POM, PEI, PMMA, ABSPVC, PC, PSU, TPU, etc.
Generally, hot tip gates are mostly used for manufacture small and medium-sized parts, especially for small size parts.
The gate section diameter is mostly between 0.5 mm and 2.0 mm.
The gate diameter is mainly determined by the weight and wall thickness of the parts, and of course, the quality of materials and parts profile should also be considered.
If the gate cross-section diameter is small, the gate will close quickly after the injection filling stage, the gate mark on the part will be small, and the surface of the part will be beautiful and of good quality.
Whereas, the diameter of the gate is too small, the shear rate of the plastic flowing through the gate will be too high, which will seriously damage the molecular chain structure of the plastic melt or additives in the plastic, resulting in unqualified products .
The usual method is to preliminarily determine the gate size according to the wall thickness at the gate of the part: gate diameter =(0.75-1.0) wall thickness at the gate of the part.
For plastics with low processing viscosity, the smaller value is taken; for plastics with high processing viscosity or those sensitive to shear, the larger value is taken.
Usually the hot tip gate is directly cut on the part, or it can be cut on the cold runner and then the cold gate can be opened on the part. This is a mold system that combines hot runner and cold runner.
When hot tip gates are used, there will always be gate marks on the parts. In many cases, the gate mark will be higher than the surface of the part, affecting the aesthetics of the part or the assembly with other parts.
Therefore, when selecting the gate location, the gate should be placed in the recessed shelter on the part as far as possible.
In a sprue hot runner system, plastic enters into the mold cavity through a sprue. The loss of pressure at the gate is small.
The sprue hot runner system is more suitable for injection molding of parts with medium size and weight.
The advantages of the sprue hot runner system are that the plastic has low shear rate when flowing through the gate to fill the mold, the residual stress after injection molding and the degree of deformation is small and the mechanical strength of the part is relatively good.
Compared with hot tip gate, the size of sprue gate is larger, so the gate marks may also be larger.
Therefore, in general, the hot-tip system is often used for molds with strict aesthetic requirements.
However, structural parts that do not require high aesthetic standards can be manufactured by the sprue hot runner system.
People also often use the sprue gate in combination with the cold runner, that is, the sprue is used as the main runner and the it is opened on the cold runner.
In this kind of application, the sprue can be opened larger to facilitate plastic flow, because the sprue mark on the cold runner is not important for looking.
Similar to the application of hot-tip hot runner system, the control of plastic temperature and mold temperature at the gate is extremely important.
It is necessary to set up a separate cooling circuit around the gate. Because the size of the sprue gate is relatively large, if the temperature at the gate is not well controlled, the drooling that the gate cannot seal the plastic flowing after the mold is opened will occur.
The sprue insert of the hot runner system also has a variety of sizes, shapes and manufacturing materials, which should be comprehensively considered with the type of plastic (such as crystalline plastic or amorphous plastic) and the cooling condition of the gate.
The needle valve hot runner system uses the mechanical movement of the needle to open and close the nozzle .
The valve needle is generally controlled by mechanical pneumatic or hydraulic pressure.
In the latter part of the holding time, the hot nozzle opening is closed before the product is completely condensed, which shortens the molding cycle of the plastic parts.
https://www.youtube.com/watch?v=1GCBDx3-RUg
By controlling the gate opening time, needle valve hot runner can ensure smooth cavity filling and melt flow balance, eliminate weld marks.
Two or more hot gates are usually required to fill large injection molded parts. For the common hot runner system, the cavity will be filled at the same time when the injection starts.
This filling style inevitably has weld marks defect, that is, when the two melt fronts meet, because the two melts cannot completely melt into one , a weld mark occur.
Although it can be improved by increasing the melt temperature and the holding pressure , the actual improvement is limited.
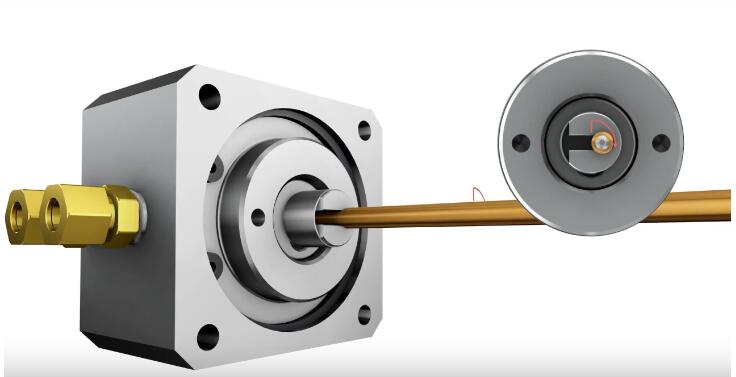
Needle valve hot runner can realize the program control of the opening and closing of each valve gate, and it means that it will open the second gate when the first melt just flows through.
At this time, the first gate can be opened or closed as required, and the process continues until all gates are opened and the mold cavity is filled, so that the melt is completely weld, and a product without weld marks is achieved.
Needle valve hot nozzles have many advantages:
The hot runner can be heated independently while it is thermally insulated in the injection mold, which can compensate for heat loss caused by contact with the "cold" mold surface.
https://www.youtube.com/watch?v=QGq0YxrIHPs
Hot runner molds have been successfully used to shoot various plastic materials.
Almost all plastic materials that can be shot with cold runner molds can be processed with hot runner molds.
The minimum injection parts are less than 0.1g, and the maximum injection parts are more than 30kg.
Hot runner molds are widely used in electronics, automobiles, medical, daily necessities, toys, packaging, construction, office equipment and etc., industries
The most important two technical factors:
- The control of plastic temperature;
- The control of plastic flow.
A typical hot runner system consists of the following parts:
- Hot runner manifold;
- Nozzle;
- Temperature controller;
- Auxiliary parts.
Types and Applications
When hot runner is adopted, the correct selection of gate type is very important. The gate directly determines the selection of hot runner system and the mold manufacture.
Therefore, according to different gate types, hot runner systems can be divided into three types:
- Hot tip hot runner system,
- Sprue hot runner system
- valve hot runner system.
Each type of hot runner system has its important characteristics and application.
Many factors need to be considered when selecting gate and hot runner system , among which the most important ones are plastic materials and additives, weight and wall thickness , quality requirements , tool life and production of parts, etc.
Pros:
- Shortening the cycle time ;
- Save plastic raw materials;
- Reduce waste products and improve product quality;
- Eliminate of secondary processes, which is conducive to full automation;
- Expand the application of injection molding.
Cons:
- Higher cost of mold,
- Higher requirements for manufacturing process equipment,
- Complicated operation and maintenance, etc.
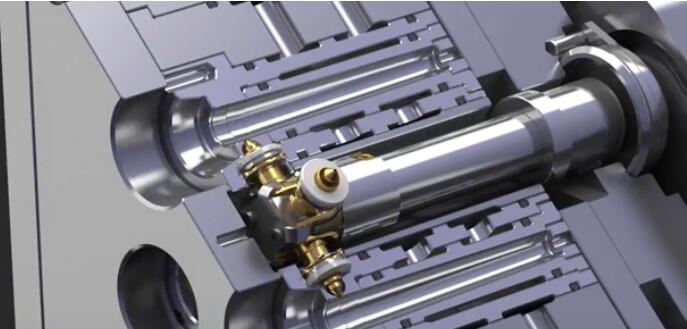
HOT TIP hot runner system
This system principle is that the HOT TIP located at the front end of the nozzle is matched with the cooling system to accurately adjust and control the plastic molding processing temperature at the gate.
Therefore, the material and shape of the nozzle HOT TIP are very important.
HOT TIP hot runner system can be used to process most crystalline and amorphous plastics such as PP, PE, PS, LCP, PA, PET, PBT, PEEK, POM, PEI, PMMA, ABSPVC, PC, PSU, TPU, etc.
Generally, hot tip gates are mostly used for manufacture small and medium-sized parts, especially for small size parts.
The gate section diameter is mostly between 0.5 mm and 2.0 mm.
The gate diameter is mainly determined by the weight and wall thickness of the parts, and of course, the quality of materials and parts profile should also be considered.
If the gate cross-section diameter is small, the gate will close quickly after the injection filling stage, the gate mark on the part will be small, and the surface of the part will be beautiful and of good quality.
Whereas, the diameter of the gate is too small, the shear rate of the plastic flowing through the gate will be too high, which will seriously damage the molecular chain structure of the plastic melt or additives in the plastic, resulting in unqualified products .
The usual method is to preliminarily determine the gate size according to the wall thickness at the gate of the part: gate diameter =(0.75-1.0) wall thickness at the gate of the part.
For plastics with low processing viscosity, the smaller value is taken; for plastics with high processing viscosity or those sensitive to shear, the larger value is taken.
Usually the hot tip gate is directly cut on the part, or it can be cut on the cold runner and then the cold gate can be opened on the part. This is a mold system that combines hot runner and cold runner.
When hot tip gates are used, there will always be gate marks on the parts. In many cases, the gate mark will be higher than the surface of the part, affecting the aesthetics of the part or the assembly with other parts.
Therefore, when selecting the gate location, the gate should be placed in the recessed shelter on the part as far as possible.
SPRUE GATE hot runner system
In a sprue hot runner system, plastic enters into the mold cavity through a sprue. The loss of pressure at the gate is small.
The sprue hot runner system is more suitable for injection molding of parts with medium size and weight.
The advantages of the sprue hot runner system are that the plastic has low shear rate when flowing through the gate to fill the mold, the residual stress after injection molding and the degree of deformation is small and the mechanical strength of the part is relatively good.
Compared with hot tip gate, the size of sprue gate is larger, so the gate marks may also be larger.
Therefore, in general, the hot-tip system is often used for molds with strict aesthetic requirements.
However, structural parts that do not require high aesthetic standards can be manufactured by the sprue hot runner system.
People also often use the sprue gate in combination with the cold runner, that is, the sprue is used as the main runner and the it is opened on the cold runner.
In this kind of application, the sprue can be opened larger to facilitate plastic flow, because the sprue mark on the cold runner is not important for looking.
Similar to the application of hot-tip hot runner system, the control of plastic temperature and mold temperature at the gate is extremely important.
It is necessary to set up a separate cooling circuit around the gate. Because the size of the sprue gate is relatively large, if the temperature at the gate is not well controlled, the drooling that the gate cannot seal the plastic flowing after the mold is opened will occur.
The sprue insert of the hot runner system also has a variety of sizes, shapes and manufacturing materials, which should be comprehensively considered with the type of plastic (such as crystalline plastic or amorphous plastic) and the cooling condition of the gate.
NEEDLE VALVE hot runner system
The needle valve hot runner system uses the mechanical movement of the needle to open and close the nozzle .
The valve needle is generally controlled by mechanical pneumatic or hydraulic pressure.
In the latter part of the holding time, the hot nozzle opening is closed before the product is completely condensed, which shortens the molding cycle of the plastic parts.
https://www.youtube.com/watch?v=1GCBDx3-RUg
By controlling the gate opening time, needle valve hot runner can ensure smooth cavity filling and melt flow balance, eliminate weld marks.
Two or more hot gates are usually required to fill large injection molded parts. For the common hot runner system, the cavity will be filled at the same time when the injection starts.
This filling style inevitably has weld marks defect, that is, when the two melt fronts meet, because the two melts cannot completely melt into one , a weld mark occur.
Although it can be improved by increasing the melt temperature and the holding pressure , the actual improvement is limited.
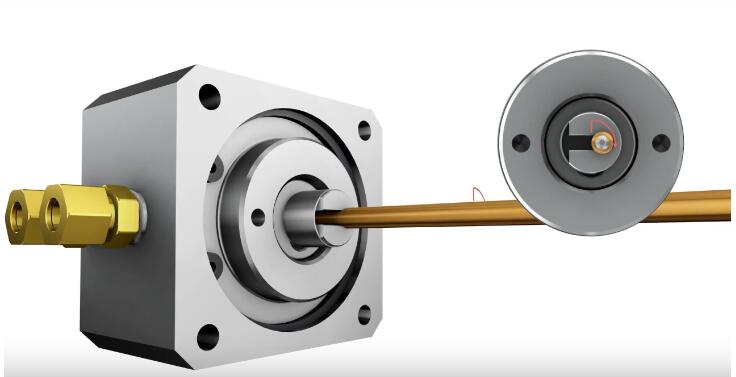
Needle valve hot runner can realize the program control of the opening and closing of each valve gate, and it means that it will open the second gate when the first melt just flows through.
At this time, the first gate can be opened or closed as required, and the process continues until all gates are opened and the mold cavity is filled, so that the melt is completely weld, and a product without weld marks is achieved.
Needle valve hot nozzles have many advantages:
- There is little or no trace on the contact surface between valve needle and product . For plastic parts with strict surface requirements, needle valve type is the best choice.
- The gate size is large enough. Large diameter gate can reduce the loss of shear heat and pressure, make the cavity fill faster, help to reduce product stress, reduce product deformation, and improve the quality of plastic parts with complex structures.
- Prevent gate drooling during mold opening, improve product appearance and product consistency.
- When the screw moves backward, the material can be prevented from flowing back from the mold cavity.
- The mechanical movement of the valve needle makes the needle valve hot runner system have better balance and re-peatability.
- More effective control of packing and molding cycle. Needle valve hot runner can use a gate with a larger diameter, which can speed up the flow of melt into the mold cavity, thus shortening the molding cycle time and better maintaining pressure.
[…] hot runner mold integrate the advantages of simple action of the two plate mold and the melt of the three plate mold entering from any point […]
ReplyDelete