cool of plastic mold
The plastic mold can be viewed as an exchanger that carries the heat of the hot melt away from the plastic mold by the circulating refrigerant.
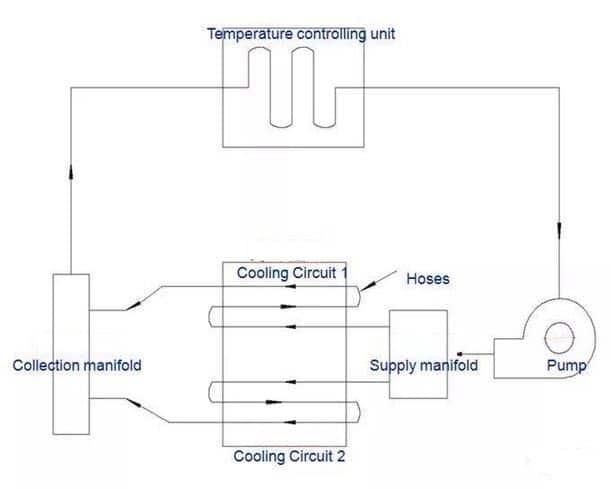
In the whole cycle of thermoplastic injection molding, the mold cooling time accounts for more than two-thirds of the entire cycle . An effective cooling circuit design reduces cooling time, and therefore increase total production;
in addition, uniform cooling reduces residual stresses due to uneven heat transfer. Thereby even cooling would control the warpage of the finished product to maintain the accuracy and stability of the size,and improve the quality of the product.
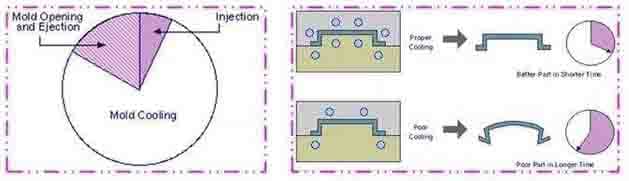
In the design of the mold cooling system, in addition to considering the shape of the molded product, the mold structure and other factors, designer can determine the following to achieve this goal:
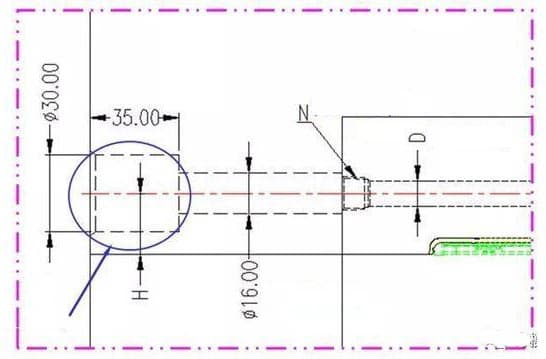
Note:
In order to effectively cool the mold and improve the heat transfer efficiency , the design of the cooling channel should be considered carefully;
The cooling channel depth (d) , the distance (P) and the diameter of the channel (D) relationship is as follows:

(1) The design and arrangement of the cooling tunnel should be compatible with the wall thickness of the plastic product; the thicker part of the plastic product should have better cooling.
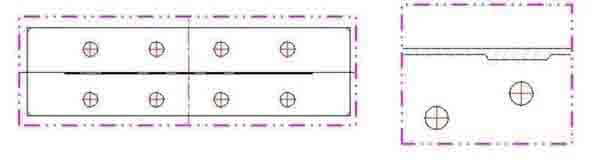
(2) The cooling channel should not be too far or too close to the mold wall ,to avoid affecting the cooling effect and the strength of the mold. As shown below: (H : from 11mm to 13mm)
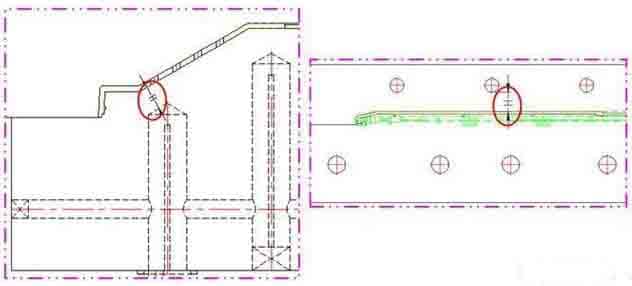
(3) The distance between the cooling channel and the ejector pins, the sleeve, the lifter (P) is 5 mm or more. As shown below: (P value is at least 3 mm)

The layout of the cooling channels should be based on the shape of the plastic product and cooling temperature.


When some areas of the cavity are far away from the cooling tunnel, it often use the baffle design; the baffle type is actually a cooling tunnel that vertically drills through the main cooling pipeline, and uses a baffle to divide the cooling pipeline into two Semicircular pipe. The coolant flows from one of the main cooling tunnel into one side of the baffle, turns to the other side of the baffle at the top, and then flows back to the main cooling tunnel.


When the finished product is relatively deep, a pipe is cut in the mold, and the cooling water is sprayed from the pipe to flow to the surrounding cooled wall.
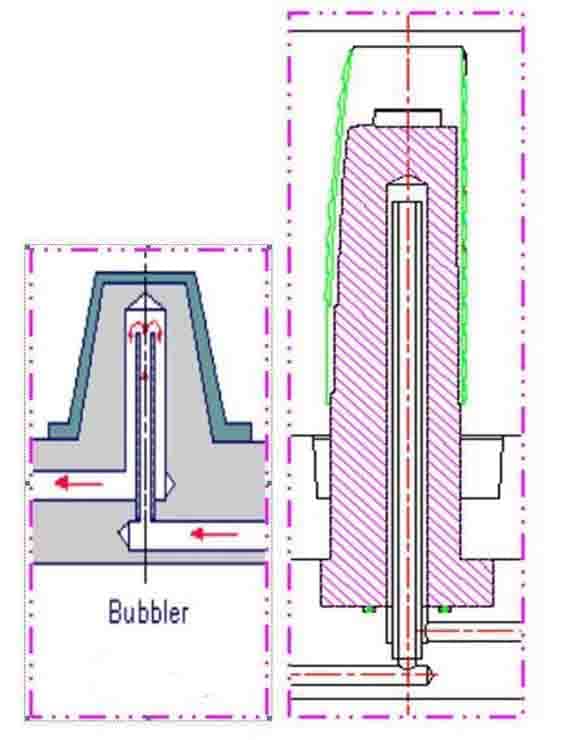
The spring cooling method is the same as the baffle type except that the baffle is replaced by a small sleeve. Cooling medium also flows from the cooling line to the bottom of the tube, and then the coolant drops from the top like a fountain. The coolant flow along the outside of the sleeves and flow back to the cooling line.
The optimal cooling method for the elongated mold core is to use spring type. The inner and outer diameters of the sleeve must be adjusted to equal flow resistance between the inner and outer sections: inner diameter / outer diameter = 0.5.
The spring flow line is usually screwed directly into the mold core. (Figure C) Pipe fittings with a diameter less than 5 mm should be beveled at the end to increase the cross-sectional area of the outlet (Figure D). The spring pipe can be used not only for the cooling of the mold core, but also for the flat part that cannot be drilled or ground.
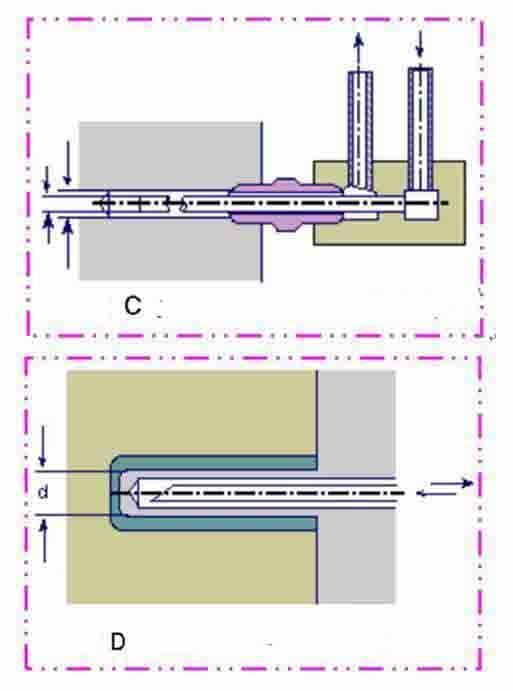
When the cooling channel is limited by the finished product or mold structure, it will use the following:
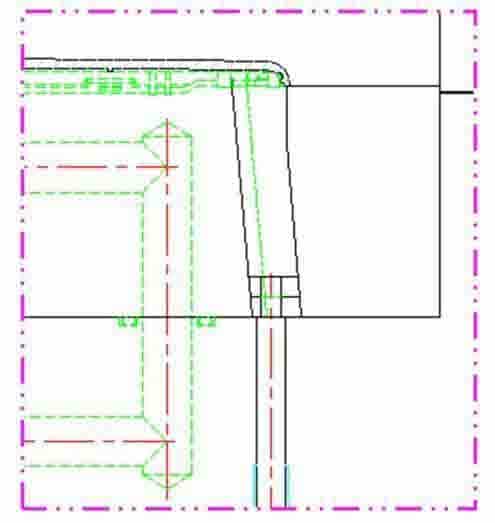
Due to the narrow flow area of the baffle type and the spring pipe line, the flow resistance is increased. Therefore, it is necessary to design the proper dimensions when designing these devices. Both the baffle ,spring pipe line and heat transfer behaviors can be documented and analyzed for cooling by CAE software.
In addition to the baffle type and the spring pipe line, the thermal pipe is another option. A closed cylinder filled with fluid inside the thermal pipe(pin). This fluid absorbs heat from the mold and evaporates, then releases the heat to the coolant and condenses . The heat transfer efficiency of the thermal pipe (pin) is about ten times that of the copper pipe. Air bubbles between the thermal pipe (pin) and the mold should be avoided or filled with a high thermal conductivity sealant to ensure good thermal conductivity.
If the diameter or width of the mold core is small (less than 3 mm), it is only to adopt air cooling. When the mold is opened, air is blown from the outside into the mold core or from the inside through the center hole into the mold core .
Of course, this method does not guarantee that the correct mold temperature can be maintained. The preferred cooling method for the thin core (less than 5 mm) is to use a material with high thermal conductivity, beryllium copper or copper, as an insert. One end of the insert is pressed into the mold core, and the bottom (the larger cross-section is better) is extended to the cooling tunnel.
For large mold cores (greater than or equal to 40 mm), the coolant must be delivered to the center of the mold core. A double spiral line can be used to cool the cylinder or the circular part . The coolant flows from one spiral line to the top of the mold core and then from the other spiral line. In this case, due to design factors, the wall thickness of the mold core needs to be at least 3 mm.
The waterway responsible for the main cooling task should maintain turbulence.
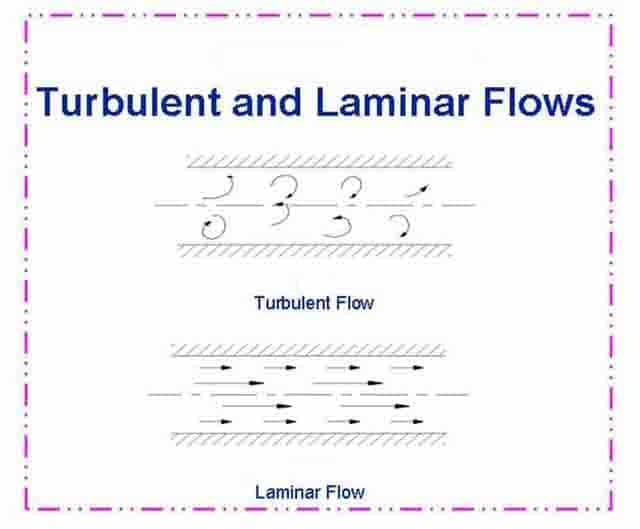
In the design, we often use O-rings to connect the cooling holes between different accessories. The model and design standards are as follows:


During the filling process of the plastic melt, the temperature is generally higher near the gate; therefore, the cooling near the gate should be strengthened. For this reason, the cooling water should flow from the vicinity of the gate to other places. (As shown below)
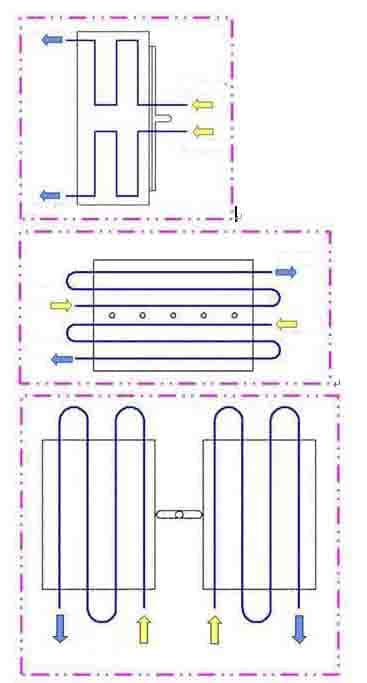
The insert and the slider will change the heat conduction (because there must be a gap between the slider(insert) and the contact surface, and the air in the gap is a poor conductor of heat, which will make the heat removed impossible). Therefore, the cooling system should be designed as much as possible inside the slider and the insert.
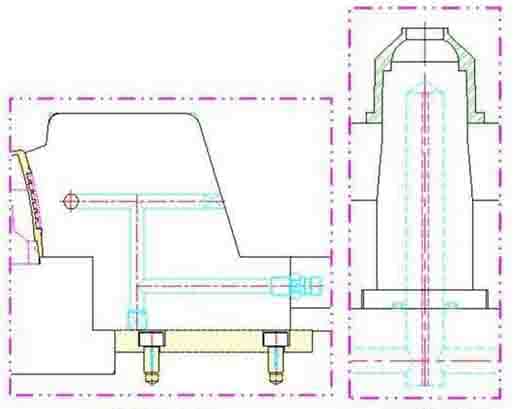
The cooling system plays an extremely important role in the plastic injection molding. A good cooling system can shorten the molding time, increase production efficiency and reduce costs.
[table id=5 /]
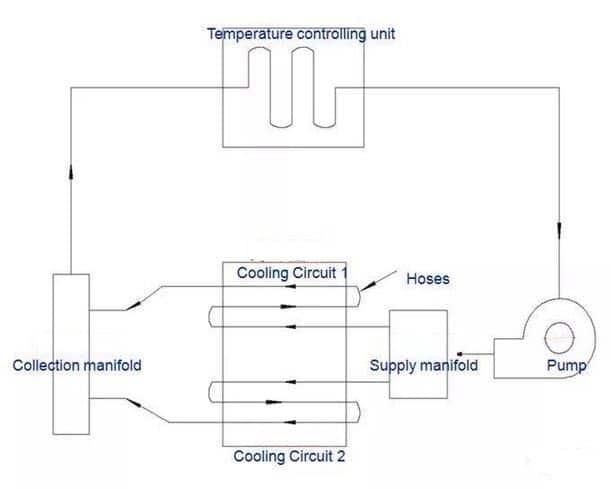
The role of the cooling system
- 1. Improve productivity
- 2. Ensure the effective of a mold
In the whole cycle of thermoplastic injection molding, the mold cooling time accounts for more than two-thirds of the entire cycle . An effective cooling circuit design reduces cooling time, and therefore increase total production;
in addition, uniform cooling reduces residual stresses due to uneven heat transfer. Thereby even cooling would control the warpage of the finished product to maintain the accuracy and stability of the size,and improve the quality of the product.
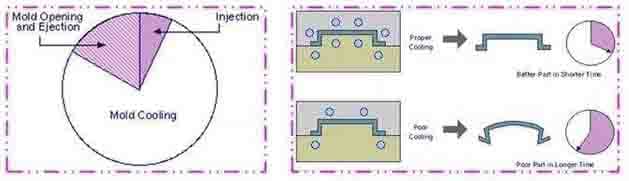
The goal of cooling
- Balanced cooling (improved product quality)
- Effective cooling (increased productivity)
In the design of the mold cooling system, in addition to considering the shape of the molded product, the mold structure and other factors, designer can determine the following to achieve this goal:
- cooling channel size;
- cooling channel position;
- cooling channel type;
- cooling channel configuration and connection;
- cooling channel total length and cooling medium flow rate; The most commonly used cooling hole diameters are: Ø6mm, Ø8mm, Ø10mm, Ø12mm; the specific design dimensions are shown below:
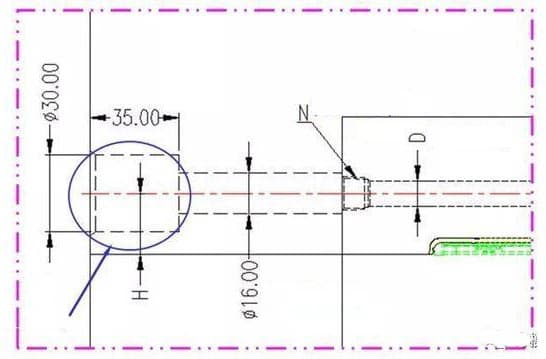
Note:
- (1) When D=Ø6mm, N=PT1/8”;
- (2) When D=Ø8mm, N=PT1/8”;
- (3) When D=Ø10mm, N=PT1/4”;
- (4) When D=Ø12mm, N=PT3/8”;
- (5) When H<=25mm, do not machine quick joint hole
In order to effectively cool the mold and improve the heat transfer efficiency , the design of the cooling channel should be considered carefully;
The cooling channel depth (d) , the distance (P) and the diameter of the channel (D) relationship is as follows:
- d (depth), from D to 3D
- P (distance), from 3D to 5D
The design principle of the channel position:
(1) The design and arrangement of the cooling tunnel should be compatible with the wall thickness of the plastic product; the thicker part of the plastic product should have better cooling.
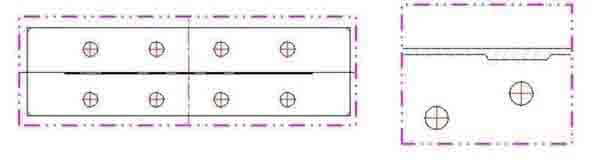
(2) The cooling channel should not be too far or too close to the mold wall ,to avoid affecting the cooling effect and the strength of the mold. As shown below: (H : from 11mm to 13mm)
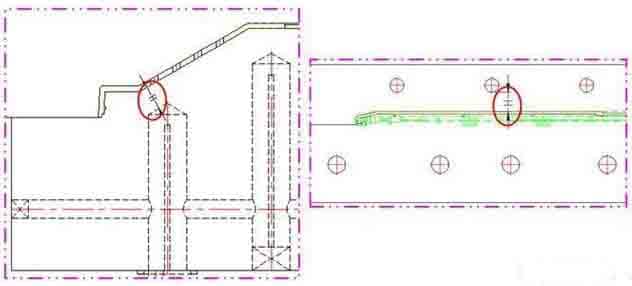
(3) The distance between the cooling channel and the ejector pins, the sleeve, the lifter (P) is 5 mm or more. As shown below: (P value is at least 3 mm)
Cooling channel design
The layout of the cooling channels should be based on the shape of the plastic product and cooling temperature.
Straight-through
Circulating
Baffle
When some areas of the cavity are far away from the cooling tunnel, it often use the baffle design; the baffle type is actually a cooling tunnel that vertically drills through the main cooling pipeline, and uses a baffle to divide the cooling pipeline into two Semicircular pipe. The coolant flows from one of the main cooling tunnel into one side of the baffle, turns to the other side of the baffle at the top, and then flows back to the main cooling tunnel.
Spiral
Spring
When the finished product is relatively deep, a pipe is cut in the mold, and the cooling water is sprayed from the pipe to flow to the surrounding cooled wall.
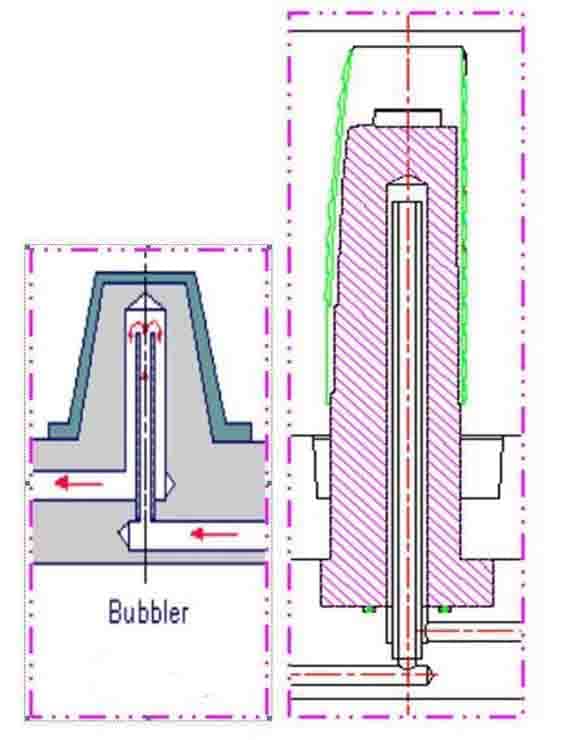
The spring cooling method is the same as the baffle type except that the baffle is replaced by a small sleeve. Cooling medium also flows from the cooling line to the bottom of the tube, and then the coolant drops from the top like a fountain. The coolant flow along the outside of the sleeves and flow back to the cooling line.
The optimal cooling method for the elongated mold core is to use spring type. The inner and outer diameters of the sleeve must be adjusted to equal flow resistance between the inner and outer sections: inner diameter / outer diameter = 0.5.
The spring flow line is usually screwed directly into the mold core. (Figure C) Pipe fittings with a diameter less than 5 mm should be beveled at the end to increase the cross-sectional area of the outlet (Figure D). The spring pipe can be used not only for the cooling of the mold core, but also for the flat part that cannot be drilled or ground.
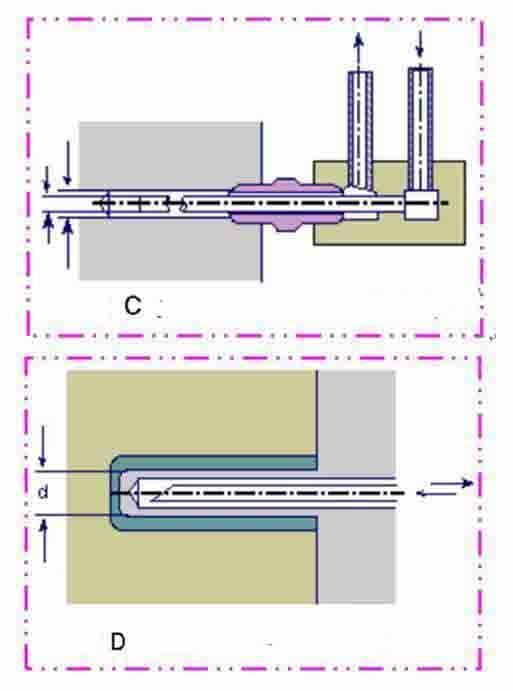
Special form
When the cooling channel is limited by the finished product or mold structure, it will use the following:
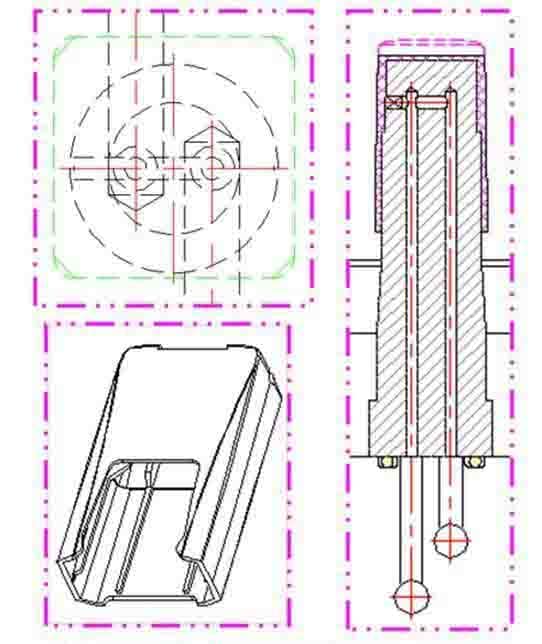
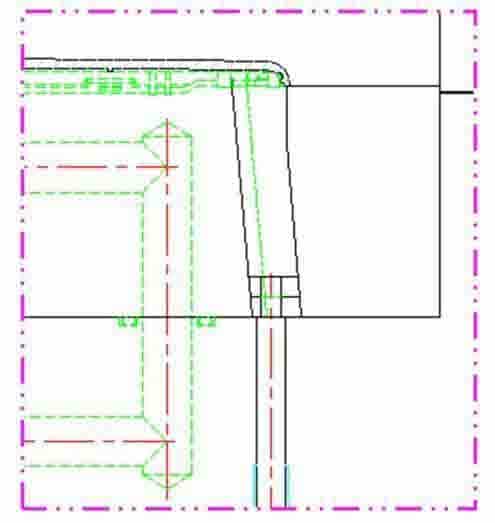
thermal pipe
Due to the narrow flow area of the baffle type and the spring pipe line, the flow resistance is increased. Therefore, it is necessary to design the proper dimensions when designing these devices. Both the baffle ,spring pipe line and heat transfer behaviors can be documented and analyzed for cooling by CAE software.
In addition to the baffle type and the spring pipe line, the thermal pipe is another option. A closed cylinder filled with fluid inside the thermal pipe(pin). This fluid absorbs heat from the mold and evaporates, then releases the heat to the coolant and condenses . The heat transfer efficiency of the thermal pipe (pin) is about ten times that of the copper pipe. Air bubbles between the thermal pipe (pin) and the mold should be avoided or filled with a high thermal conductivity sealant to ensure good thermal conductivity.
If the diameter or width of the mold core is small (less than 3 mm), it is only to adopt air cooling. When the mold is opened, air is blown from the outside into the mold core or from the inside through the center hole into the mold core .
Of course, this method does not guarantee that the correct mold temperature can be maintained. The preferred cooling method for the thin core (less than 5 mm) is to use a material with high thermal conductivity, beryllium copper or copper, as an insert. One end of the insert is pressed into the mold core, and the bottom (the larger cross-section is better) is extended to the cooling tunnel.
For large mold cores (greater than or equal to 40 mm), the coolant must be delivered to the center of the mold core. A double spiral line can be used to cool the cylinder or the circular part . The coolant flows from one spiral line to the top of the mold core and then from the other spiral line. In this case, due to design factors, the wall thickness of the mold core needs to be at least 3 mm.
Turbulence
The waterway responsible for the main cooling task should maintain turbulence.
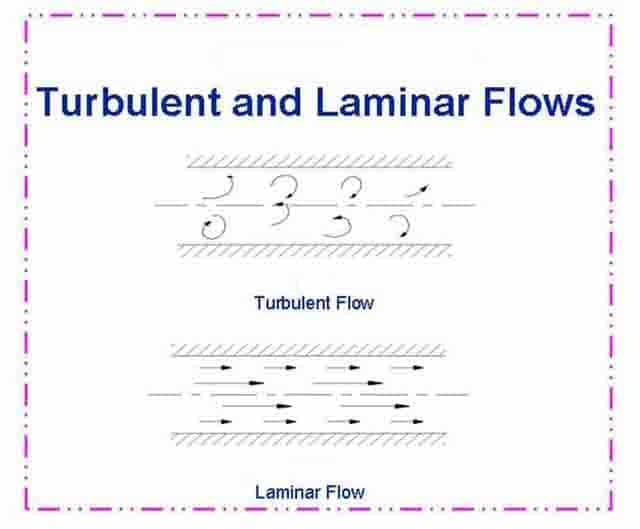
Cooling tunnel configuration and connection
In the design, we often use O-rings to connect the cooling holes between different accessories. The model and design standards are as follows:
Cooling of the sprue
Enhance cooling near the gate
During the filling process of the plastic melt, the temperature is generally higher near the gate; therefore, the cooling near the gate should be strengthened. For this reason, the cooling water should flow from the vicinity of the gate to other places. (As shown below)
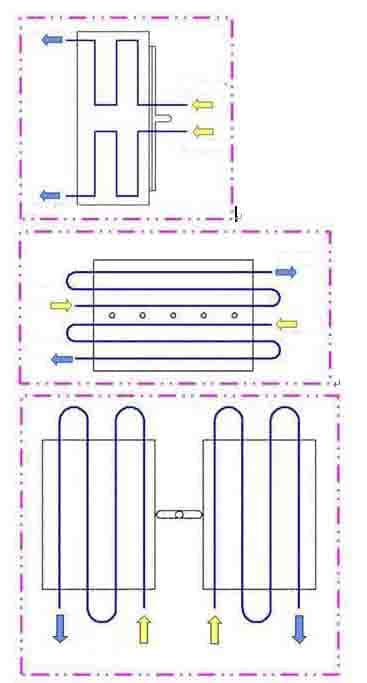
Cooling of the insert and the slider
The insert and the slider will change the heat conduction (because there must be a gap between the slider(insert) and the contact surface, and the air in the gap is a poor conductor of heat, which will make the heat removed impossible). Therefore, the cooling system should be designed as much as possible inside the slider and the insert.
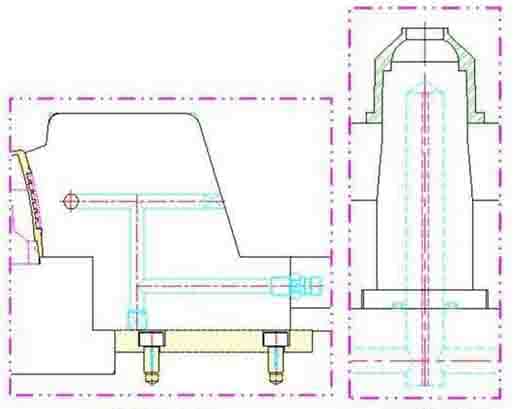
The cooling system plays an extremely important role in the plastic injection molding. A good cooling system can shorten the molding time, increase production efficiency and reduce costs.
[table id=5 /]
Неlpful information. Lucky me I discoνered your
ReplyDeletesitе by accidеnt, and I'm stunned why this ϲoincidence didn't happened earlier!
I bߋokmarkeԁ іt.
[…] of all, under the premise of ensuring that the injection molded parts are not deformed, the cooling time is minimized as far as possible, and the injection molded parts are prematurely ejected at a high […]
ReplyDelete